Shrinkage porosity is a common casting defect that occurs due to the shrinkage of metal during solidification. It can lead to reduced mechanical properties, compromised structural integrity, and overall decreased casting quality. Overcoming shrinkage porosity requires a combination of strategies and careful considerations throughout the casting production process. In this article, we explore various strategies and considerations for effectively addressing shrinkage porosity in casting production.
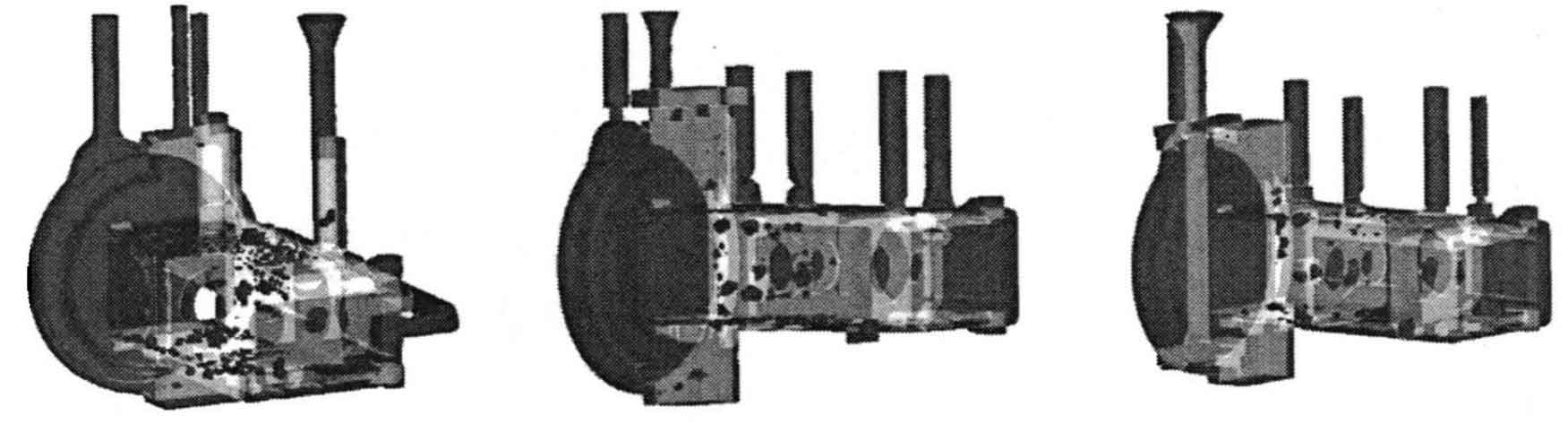
- Proper Alloy Selection: The selection of the casting alloy plays a significant role in managing shrinkage porosity. Some alloys are more prone to shrinkage than others due to their solidification characteristics. By choosing alloys with lower solidification shrinkage and improved feeding characteristics, the susceptibility to shrinkage porosity can be reduced.
- Optimized Casting Design: Well-designed casting geometries can help minimize the occurrence of shrinkage porosity. Considerations such as avoiding sharp corners, thick sections, and sudden changes in wall thickness can help promote uniform solidification and reduce the likelihood of shrinkage defects. Employing smooth transitions and fillets can facilitate a more balanced solidification and minimize the formation of shrinkage porosity.
- Riser and Gating System Design: Proper riser and gating system design is crucial for providing sufficient feeding of molten metal during solidification. Well-designed risers and gating systems ensure a continuous supply of molten metal to compensate for the volume contraction and solidification shrinkage. This promotes the proper feeding of the casting, minimizing the formation of shrinkage porosity.
- Optimized Cooling and Solidification Control: The control of cooling and solidification rates during casting plays a vital role in managing shrinkage porosity. Proper control of mold and core temperatures, as well as the use of insulating materials, can influence the solidification behavior and minimize shrinkage defects. Employing cooling techniques such as controlled cooling rates, directional solidification, and the use of chill plates can also help minimize shrinkage porosity.
- Mold and Core Design: The design of the mold and core can affect the solidification behavior and subsequent shrinkage porosity. Considerations such as the use of suitable mold materials, the placement of chills or cooling channels in critical areas, and the utilization of effective mold coatings can help optimize the solidification process and minimize shrinkage defects.
- Heat Treatment and Stress Relief: Heat treatment processes such as solution heat treatment and stress relief can be employed after casting to minimize residual stresses and alleviate shrinkage porosity. Heat treatment helps in improving the microstructure and reducing internal stresses, contributing to the reduction of shrinkage defects.
- Quality Control and Inspection: Implementing comprehensive quality control measures and inspection techniques is essential in detecting and addressing shrinkage porosity. Non-destructive testing methods such as X-ray, ultrasonic testing, and penetrant testing can be employed to identify any shrinkage-related defects and ensure casting integrity.
Overcoming shrinkage porosity in casting production requires a holistic approach that involves careful consideration of alloy selection, optimized casting design, riser and gating system design, cooling and solidification control, mold and core design, heat treatment, and robust quality control. By implementing these strategies and considerations, foundries can effectively minimize shrinkage porosity, resulting in high-quality castings with improved structural integrity and mechanical properties.