Surface defects, such as overheating and burning, can occur during heat treatment and have a significant impact on the quality and performance of treated components. These defects can lead to reduced mechanical properties, dimensional inaccuracies, and compromised surface integrity. Here are some strategies to avoid surface defects in heat treatment:
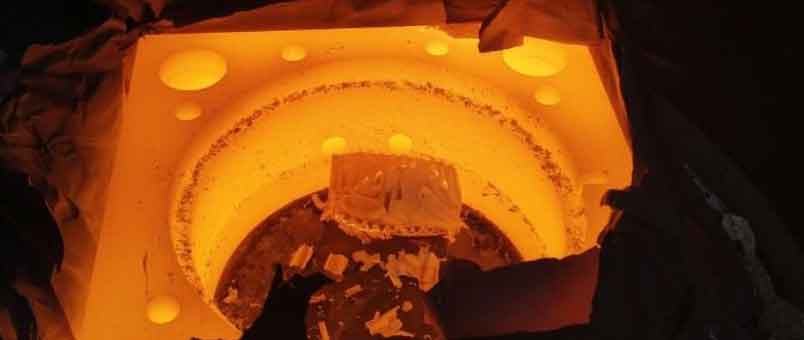
1.Proper Temperature Control:
Ensure accurate and controlled temperature management throughout the heat treatment process. Use calibrated and reliable temperature monitoring equipment to prevent overheating and maintain the desired heat treatment parameters.
2.Optimal Heating Rates:
Avoid rapid and uneven heating rates that can result in localized overheating. Implement controlled heating rates that promote uniform temperature distribution throughout the component.
3.Surface Protection:
Protect the surface of the components during heat treatment to prevent direct contact with heating elements or atmosphere. Methods for surface protection include using protective coatings, protective gas environments, or using fixtures to shield the surfaces from direct contact.
4.Proper Quenching Techniques:
Implement appropriate quenching techniques to avoid burning or overheating of the component surface. Ensure the quenching medium is suitable for the specific material and component geometry. Proper agitation or circulation of the quenching medium can help maintain uniform cooling rates.
5.Atmosphere Control:
Maintain proper atmosphere control during heat treatment to prevent surface oxidation or decarburization. Utilize appropriate atmosphere compositions, such as inert gases or controlled gas mixtures, to minimize the risk of surface defects.
6.Heat Treatment Equipment Maintenance:
Regularly inspect and maintain heat treatment equipment to ensure it is in good working condition. This includes checking heating elements, thermocouples, insulation, and control systems to ensure they are functioning properly and accurately.
7.Surface Cleaning:
Thoroughly clean the component surfaces before heat treatment to remove contaminants, such as oils, greases, or dirt. Contaminants can cause localized overheating or contribute to surface defects.
8.Process Optimization:
Continuously monitor and optimize the heat treatment process to prevent surface defects. This includes evaluating process parameters, such as time, temperature, quenching media, and atmosphere composition, to achieve the desired heat treatment results while avoiding surface issues.
9.Quality Control and Inspection:
Implement regular quality control measures and inspections to detect surface defects early. Utilize non-destructive testing techniques, visual inspection, or surface roughness measurements to identify any surface irregularities or deviations from the desired specifications.
10.Operator Training and Expertise:
Provide proper training to heat treatment operators to ensure they have a thorough understanding of the heat treatment process, including the risks associated with surface defects. Operators should be knowledgeable about process control, material behavior, and the appropriate handling of components during heat treatment.
By following these preventive measures and maintaining a high level of process control, it is possible to minimize surface defects such as overheating and burning in heat-treated components. Collaboration between heat treatment experts, quality control personnel, and metallurgists can help identify potential risks and develop effective strategies for surface defect prevention.