In the realm of sand casting, porosity is a common challenge that can drastically affect the final product’s mechanical properties and structural integrity. This article explores how porosity occurs, its impact on casting, and the importance of preventive strategies.
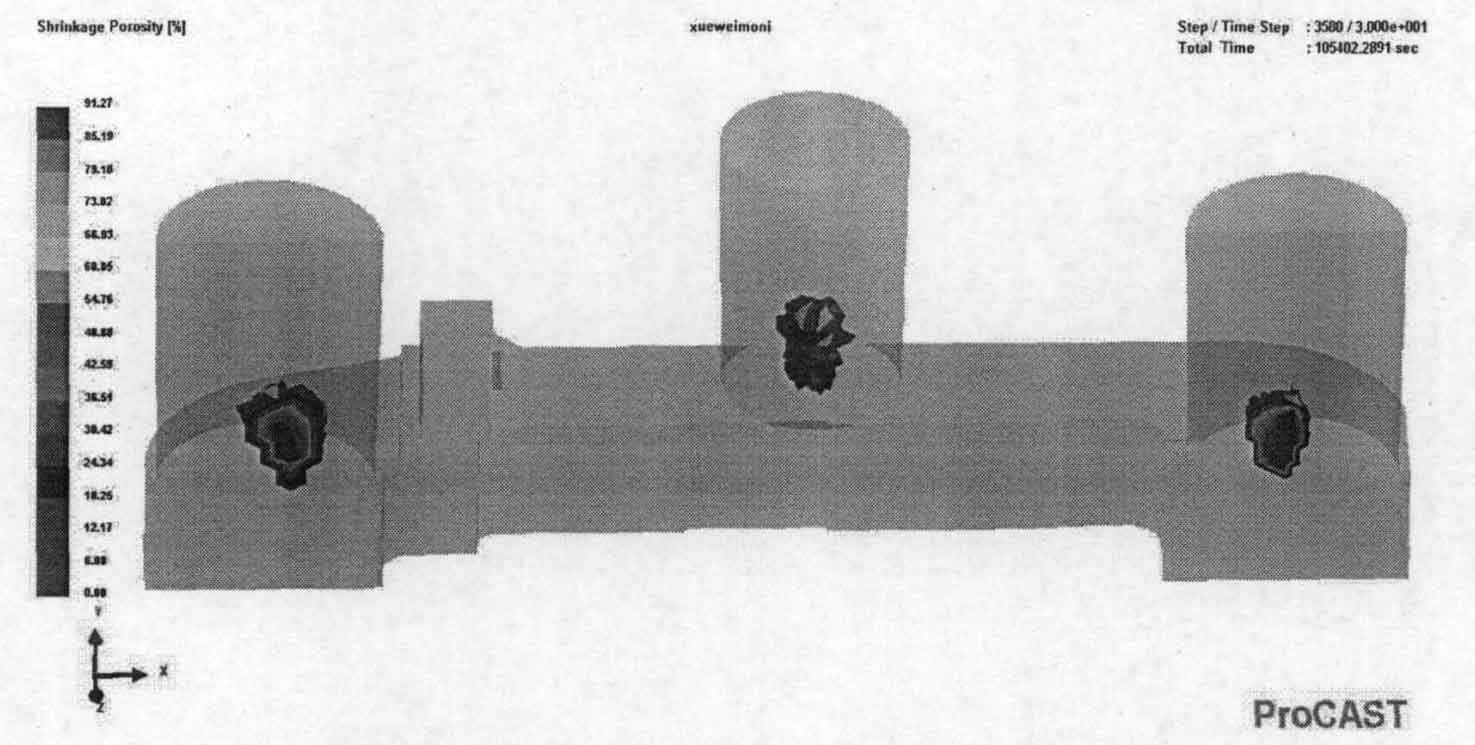
Understanding Porosity:
Porosity in sand casting is a condition where voids or pores form within the cast part. The two main causes of porosity are gas entrapment and shrinkage. Gas entrapment occurs when gases present in the molten metal or released from the mold get trapped during solidification. Shrinkage, on the other hand, occurs when the metal contracts as it cools, creating voids if the shrinkage is not properly compensated for.
Effects of Porosity:
- Mechanical Properties: The presence of pores within the material disrupts the uniform structure, resulting in a decrease in mechanical properties. Porosity can lead to reduced tensile strength, fatigue strength, impact toughness, and ductility. Cast parts with high porosity are more likely to fail under stress, leading to premature failure in service.
- Structural Integrity: Porosity not only affects the overall strength of the cast part but also its durability. Porous areas act as points of weakness where cracks can start and propagate, making the part more susceptible to damage over time.
- Aesthetics: In addition to its mechanical effects, porosity can also affect the appearance of the cast part. Porosity can lead to a rough or pitted surface that can affect the part’s visual appeal and may require additional finishing processes to rectify.
Mitigating Porosity:
While porosity can have significant effects, there are several strategies manufacturers can employ to mitigate its occurrence. These include proper mold and riser design, controlled pouring techniques, and preparation of the molten metal and molding sand. Regular inspection and testing of the cast parts can also help to detect and address porosity issues promptly.
Porosity in sand casting can have significant implications for the mechanical properties and structural integrity of the cast part. By understanding the causes and effects of porosity, manufacturers can develop effective strategies to minimize its occurrence, leading to improved casting quality and performance.