The as cast microstructure of ductile iron with modulus Ms = 1.25cm is 6.0% pearlite + 94.0% ferrite. Several samples with the size of Φ 10cm × 10cm were cut from the ductile iron test bar, and then they were isothermal transformed at 920 ℃ / 2H + X / 1.5h (x = 280 ℃, 330 ℃, 380 ℃), and then air cooled to room temperature. Figure 4-1 shows the XRD patterns of Austempered Ductile Iron at different isothermal transformation temperatures.
Through jade 6.5 software, it was found that the matrix structure of austempered ductile iron was composed of graphite, austenite and ferrite at 280 ℃, 330 ℃ and 380 ℃, respectively, and no carbide was found. But the difference is that the diffraction peaks corresponding to austenite phase and ferrite phase in the isothermally quenched nodular cast iron processed at different isothermal transformation temperatures deviate from each other at different angles, which is mainly related to the change of lattice and lattice constant due to the solid solution of carbon, silicon, manganese, nickel and copper in γ – Fe and α – Fe.
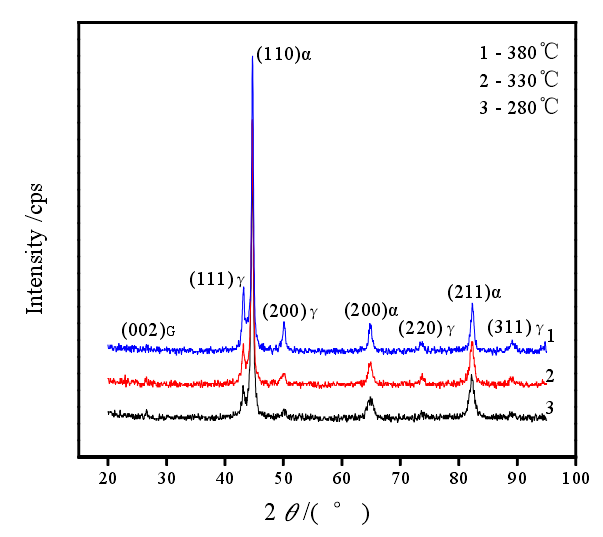
It can be found from the figure that with the increase of isothermal transformation temperature, the intensity of each diffraction peak of γ – Fe gradually increases, and the diffraction angle of each diffraction peak gradually decreases, which indicates that the amount of austenite in the matrix of austempered ductile iron increases gradually, and the carbon content in austenite increases. Correspondingly, the amount of ferrite in the matrix of austempered ductile iron decreases with the increase of isothermal transformation temperature.