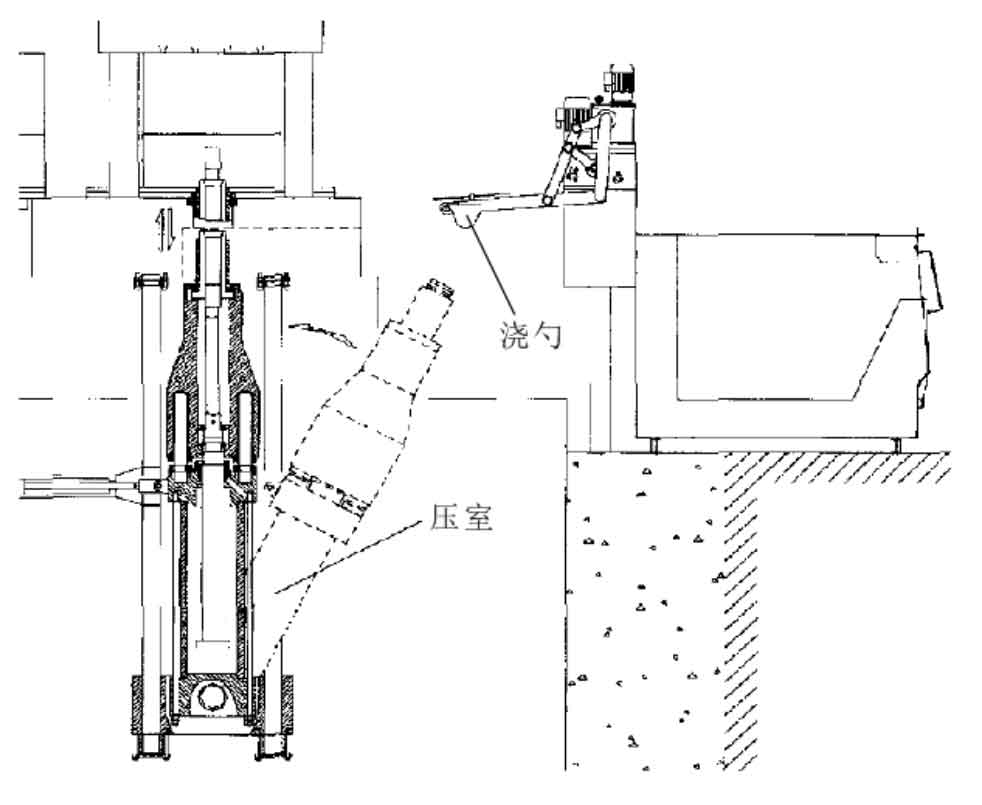
In the early application of squeeze casting technology, the melt transportation was basically manual transportation and mold filling. The labor intensity of workers was high, and the production efficiency was low. During the mold filling process, the high-temperature molten metal was prone to oxidation, which affected the performance of castings. At the same time, in the process of squeeze casting, the pressure of the punch will extrude the excess molten metal out of the mold cavity. If the amount of molten metal filled is too large, splashing will occur, resulting in potential safety hazards. With the development of industrial level, automatic conveying systems such as manipulator conveying system (as shown in Figure 1), electromagnetic pump molten liquid conveying system (as shown in Figure 2) and pneumatic molten liquid conveying system (as shown in Figure 3) have been gradually used.
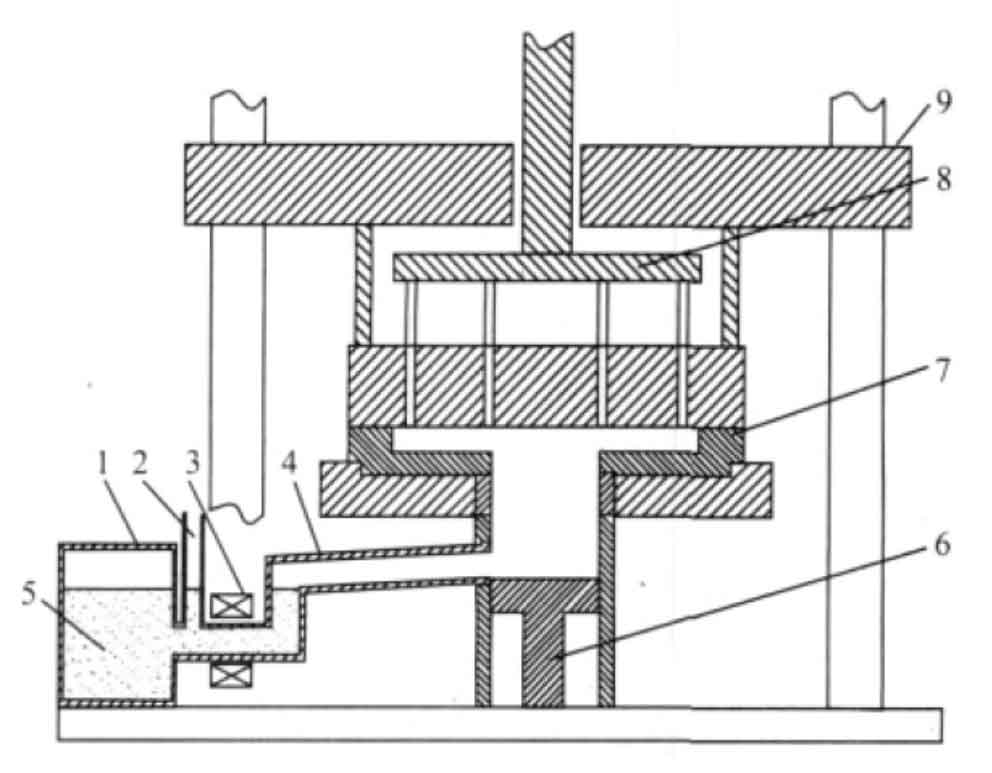
According to the production system design theory, the production logistics of squeeze casting equipment can be described by the production logistics system, which is composed of melt conveying system, mold filling system, part taking system and other subsystems, corresponding to the process of melt conveying, injection, part taking and other material transfer. With the development of automation technology, the development of parts taking system at home and abroad has been very mature, and various types of parts taking devices and control systems emerge in endlessly. However, there is still considerable room for the development of melt conveying system and mold filling system, especially for the special process requirements of squeeze casting for large castings, the melt conveying system has a great impact on the quality and production efficiency of castings. Dengjianxin put forward the method of using the simulation software Flexsim in the field of logistics to simulate the logistics of squeeze casting, and simulated the general indirect squeeze casting process. In the simulation, it is found that the production logistics system in the squeeze casting equipment operates normally, but the utilization rate of various auxiliary devices such as mold filling hand and part taking hand is very low, which not only has reference value for the further optimization of the equipment, but also can be used as a reference for the logistics simulation of the production logistics system of the composite squeeze casting system of large castings.
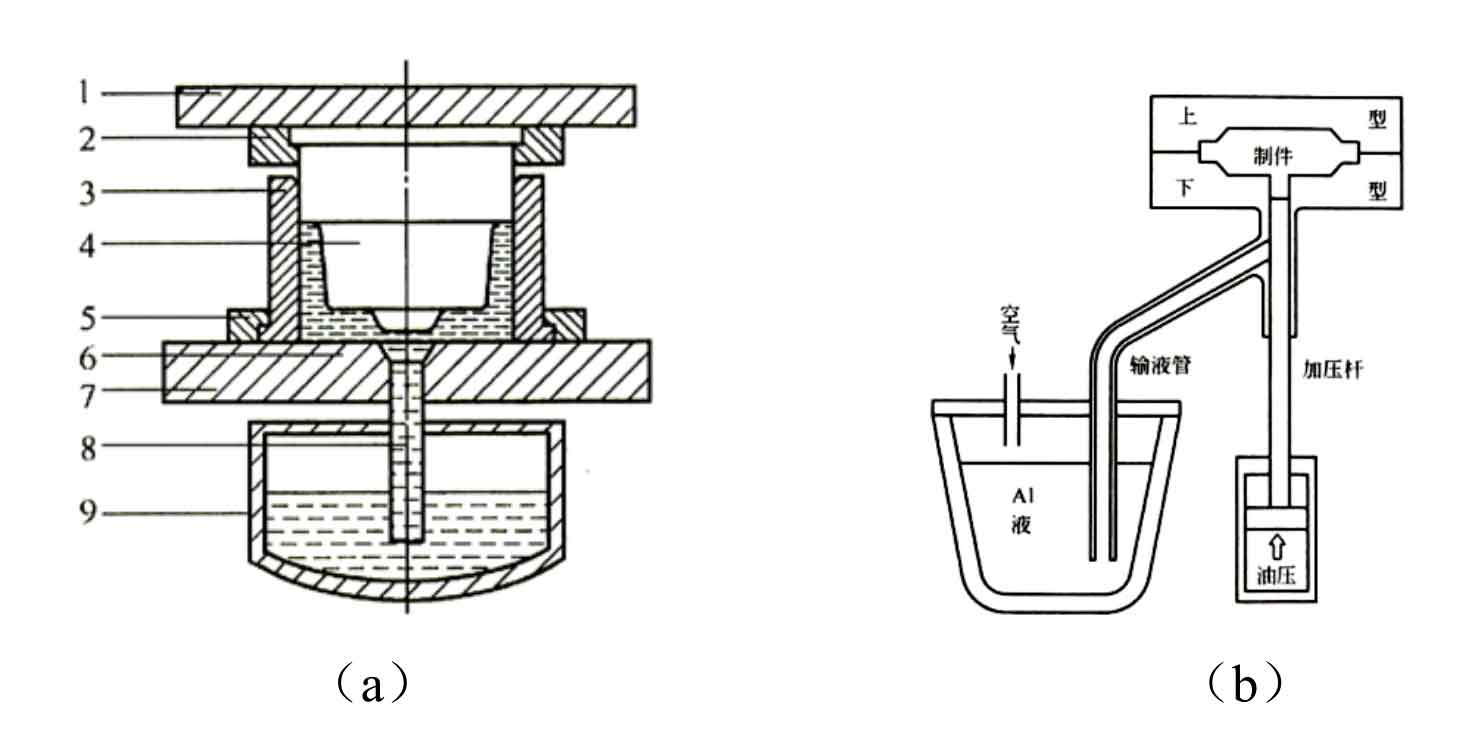
The compound squeeze casting method is proposed for the squeeze casting of large castings. It is a very important research content of this paper to successfully develop a melt conveying system that can meet the process requirements. The establishment of a system model for the production logistics system logistics simulation can optimize the design and shorten the equipment development cycle.