With the implementation of the “Three Guarantees” responsibility system in the international automobile industry, the quality requirements of automobile parts are becoming higher and higher. For the cylinder head of the key parts of the automobile engine, the product quality requirements are to keep improving, and the quality control requirements of the production process are more comprehensive and detailed.
1.Existing problems
At present, an aluminum alloy cylinder head is produced together with a domestic main engine factory, and the product delivery status is semi-finished product. During the simulation analysis of casting process design, the tendency of shrinkage porosity and shrinkage crack casting defects was not identified, and no relevant shrinkage crack casting defects were found during the casting production inspection. However, after the deep processing of the customer, it was found that there were obvious crack casting defects visible to the naked eye at the big end anti-collision beam, as shown in Figure 1.
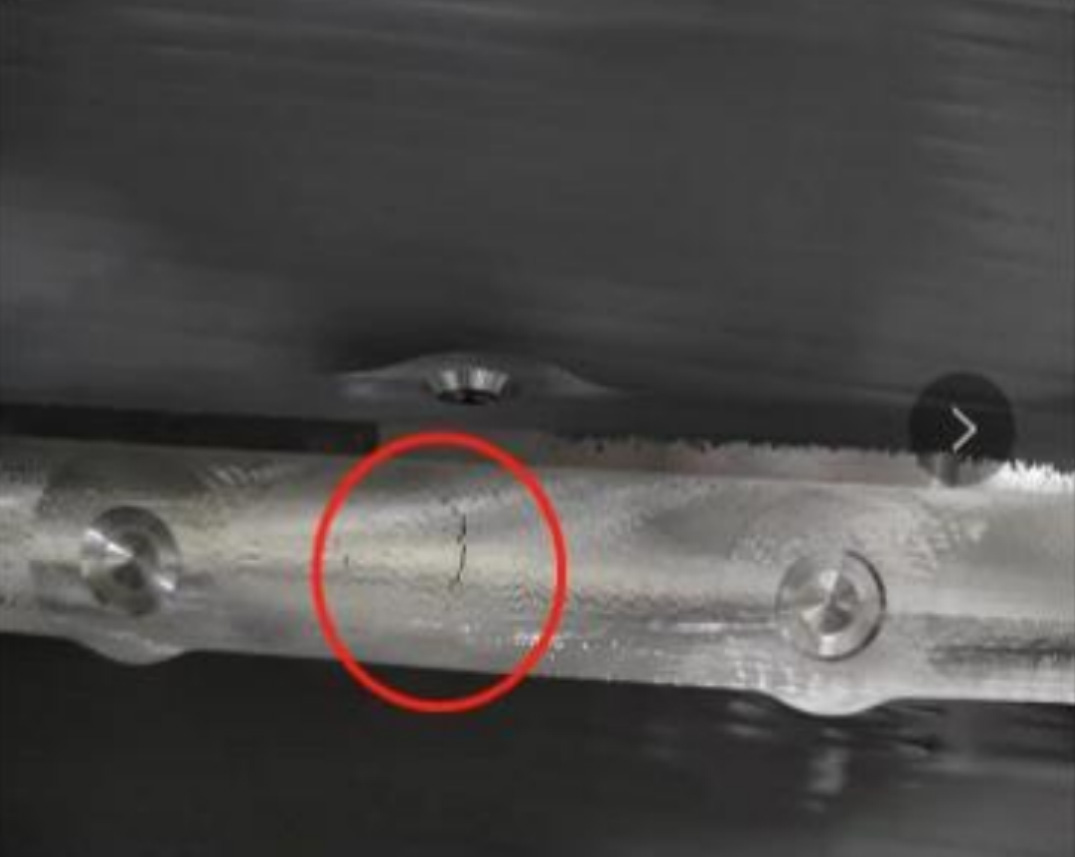
2.Defect phenomenon and cause analysis
In the technical requirements of all cylinder heads, the casting cracks do not meet the customer’s acceptance conditions. If there are hidden cracks, there is a risk that the crack casting defects will expand during the subsequent installation and use, affecting the driving safety. In order to solve the crack casting defect, we analyzed it from the aspects of human, machine, material, method and ring, and also took metallographic samples according to the phenomenon of crack casting defects, so as to provide a theoretical basis for the types of crack casting defects.
Finally, it was determined that the defect was a shrinkage crack casting defect. The cause was that during the solidification process of the casting, the cooling speed of the metal mold around the thick part was too fast, and the aluminum liquid in the center of the anti-collision beam of the casting contracted without enough feeding channels, resulting in the non compact structure of the anti-collision beam lap center. The dense layer on the surface of the casting was removed by rough machining, and the shrinkage crack casting defects were exposed only after deep machining.
3.Implementation plan
Based on the above analysis, we optimized the existing mold structure, connected the exposed riser above the anti-collision beam with the original riser, and increased the feeding channel of the anti-collision beam adapter. After trial production, processing and verification, the shrinkage crack casting defects have been completely solved, as shown in Figure 2.
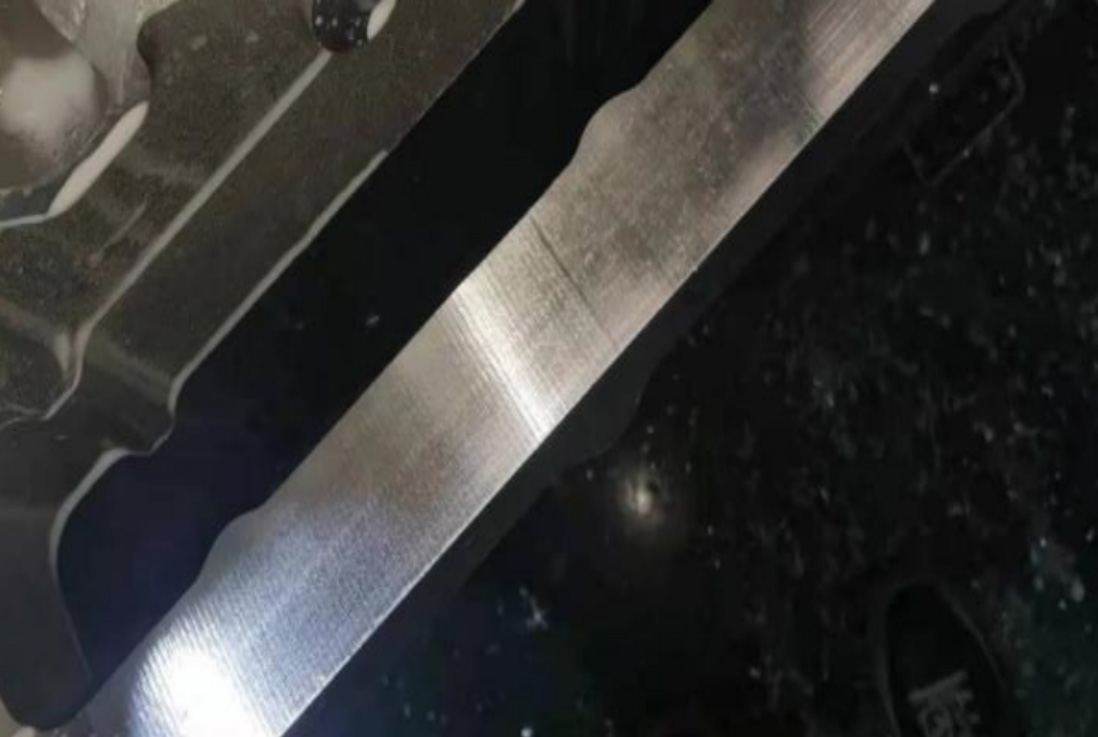
The solution of shrinkage crack casting defects reduces the quality responsibility risk of the product, improves the comprehensive qualification rate of the casting, reduces the waste loss and casting manufacturing cost of the product, and makes the product occupy a leading market position.