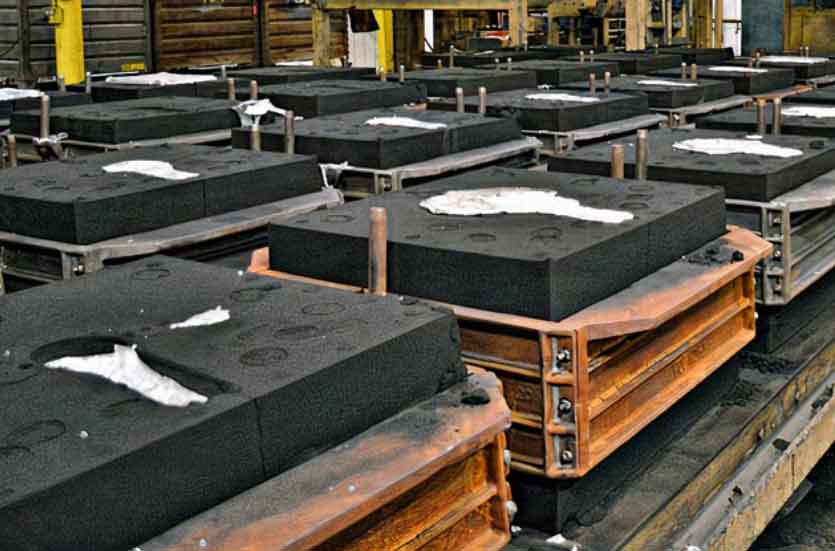
Precision engineering with resin sand casting enables the production of complex metal components with high accuracy and intricate details. While resin sand casting is typically associated with larger, less precise parts, advancements in the process and the use of modern techniques have made it possible to achieve precision in the casting of smaller and more intricate components.
To achieve precision in resin sand casting, the following factors are crucial:
- Pattern and Mold Preparation: The initial step involves creating an accurate and detailed pattern or mold. This can be done using 3D printing technology, which allows for the production of intricate patterns with high precision. The pattern must be designed to account for the contraction of the metal during solidification to ensure the final component meets the desired dimensions.
- Molding Materials: The selection of molding materials is critical for precision casting. High-quality resin-bonded sand with fine grain size is preferred to achieve better surface finish and dimensional accuracy. The sand should have excellent flowability and compaction properties to accurately replicate the pattern details.
- Molding Process Control: The molding process requires careful control to ensure precision. The sand mixture should be properly compacted around the pattern to achieve a uniform density and minimize defects like porosity. Vibratory compaction or other techniques can be employed to ensure the sand is evenly distributed and tightly packed.
- Pouring Technique: The pouring of molten metal into the mold is another critical step for precision. It is important to control the pouring speed, temperature, and gating system design to ensure proper filling of the mold without causing turbulence or defects. The use of computer-controlled pouring systems can enhance accuracy and repeatability.
- Solidification and Cooling: The cooling process after pouring is crucial for achieving precise dimensions and minimizing internal stresses. Proper cooling rates and the use of controlled cooling techniques, such as the use of cooling media or controlled atmosphere, can help control the solidification process and reduce the risk of warping or distortion.
- Post-Casting Finishing: After the casting has cooled and solidified, post-casting finishing processes can further enhance precision. These may include trimming, grinding, machining, or surface treatments to achieve the desired dimensional accuracy and surface quality.
- Quality Control and Inspection: Rigorous quality control measures should be implemented throughout the casting process. Non-destructive testing methods, such as X-ray or ultrasonic inspection, can be employed to detect any internal defects that may affect precision. Dimensional inspections using coordinate measuring machines (CMMs) or other precision measurement tools are also essential to verify the accuracy of the final component.
By incorporating these practices, resin sand casting can achieve precise and complex metal components. While it may not offer the same level of precision as some other manufacturing methods like CNC machining or investment casting, resin sand casting provides a cost-effective solution for producing intricate parts with moderate precision requirements. It offers the advantages of design flexibility, material versatility, and cost-effectiveness, making it a viable option for a range of applications in various industries.