Precision in motion is a hallmark of resin sand casting, and this casting method excels at enhancing metal fabrication in various ways. From producing intricate designs to achieving dimensional accuracy, resin sand casting plays a crucial role in the metal fabrication process. Let’s explore how it enhances metal fabrication:
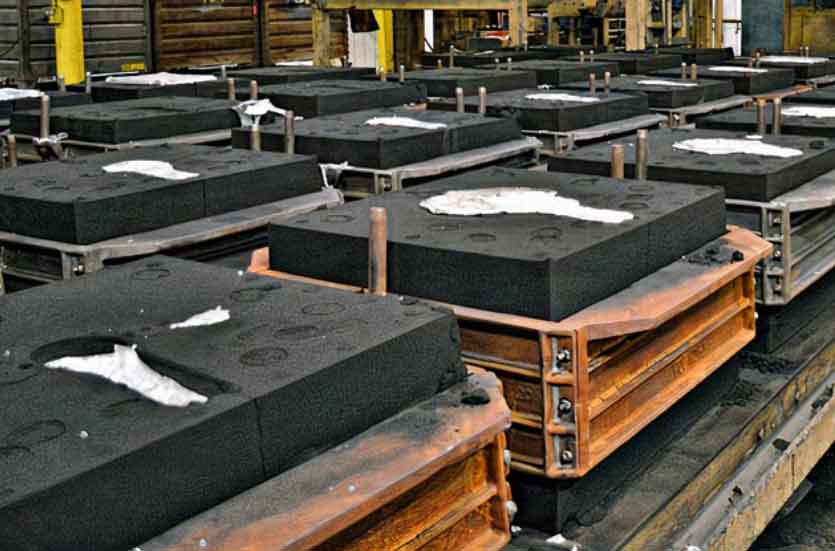
1. Intricate Designs and Complex Geometries:
Resin sand casting enables the fabrication of metal components with intricate designs and complex geometries that may be challenging or impossible to achieve through other casting methods. The versatility of resin sand casting allows for the creation of parts with intricate internal features, undercuts, and fine details.
2. High Dimensional Accuracy:
Resin sand casting’s precise molding techniques, along with the use of resin-coated sand, contribute to high dimensional accuracy in the final metal components. This level of precision is essential in metal fabrication, particularly when components need to fit together seamlessly or when tight tolerances are required.
3. Smooth Surface Finish:
The use of resin-coated sand in the casting process results in a smoother mold surface, leading to better surface finishes on the final metal components. This reduced surface roughness can minimize the need for extensive post-processing and finishing operations, saving time and cost.
4. Tooling Flexibility:
Resin sand casting offers greater tooling flexibility compared to other casting methods that require more complex and costly molds. This flexibility allows for rapid prototyping and the efficient production of small to medium batch sizes, which is especially advantageous for product development and low-volume production runs.
5. Weight Reduction and Material Optimization:
The ability to create complex geometries with thin sections and hollow structures allows for weight reduction in metal components. By optimizing designs and using less material, resin sand casting contributes to resource efficiency and material cost savings.
6. Diverse Material Compatibility:
Resin sand casting is compatible with a wide range of metals and alloys, offering flexibility in material selection to suit specific applications. Different metals can be used to achieve desired properties such as strength, corrosion resistance, or thermal conductivity.
7. Integration with Additive Manufacturing:
Resin sand casting can be integrated with additive manufacturing, such as 3D printing, to further enhance metal fabrication. 3D-printed patterns and cores can be used in the casting process, enabling the fabrication of even more complex and unique components.
8. Reduced Defects and Scrap:
Resin sand casting’s controlled mold filling and solidification processes help reduce defects in metal components, leading to higher yields and less material scrap. This efficiency in production contributes to cost-effectiveness in metal fabrication.
9. Time and Cost Savings:
With shorter setup times and efficient production cycles, resin sand casting can lead to time and cost savings in metal fabrication. The ability to produce complex parts in a single casting also eliminates the need for multiple joining processes, further streamlining fabrication.
Resin sand casting’s precision and adaptability make it a valuable tool in metal fabrication. Its ability to create intricate designs, achieve high dimensional accuracy, and optimize material usage contributes to the advancement of various industries, including automotive, aerospace, machinery, and more.