The difficulty of making the foam model is that the size of the cast steel joints is large, the width is basically 5-6 meters and the spatial structure is complex. At present, there is no such large-scale foam processing equipment in the manufacturers, so the model making is basically done by means of artificial bonding. The basic process is: first, the preformed polystyrene wool is made into the required cylinder or square, and then each cylinder or cuboid is bonded according to the spatial shape of the model.
In order to ensure the consistency of the foam model and the three-dimensional model space size. The 3D model needs to be split. As shown in the figure:
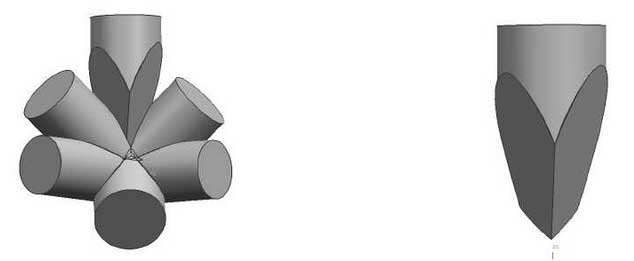
Taking the back peak node as an example, six poles are separated from the three-dimensional model. Each pole is split by a plane bounded by an intersection line. The information of the intersection line between the section plane and the cylinder surface of each pole is recorded respectively. Generally, the coordinates of one highest point and two lowest points are measured by three-dimensional software (UG).
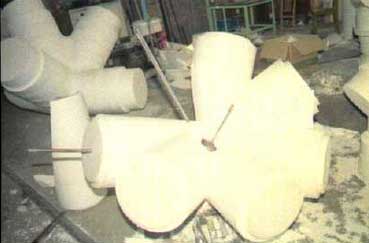
In the actual production process, workers can identify the required cross sections by the coordinates of the three points, and use the resistance wire to cut the round bar foam blank. After the six rods are cut, they are successively bonded. This ensures that the accuracy of the node space is made, and the labor intensity of the workers is reduced.