The production impeller adopts the EPC resin sand composite molding process to obtain the whole sand core, which improves the precision of the casting impeller and reduces the labor intensity of the workers. The key to obtain the high quality sand core is the core box. The original wooden core box can only produce composite core, which can not be used in the new process. Therefore, in order to obtain the whole sand core, it is necessary to design a new core box suitable for the new technology. Considering the characteristics of EPC resin sand composite molding, it is determined that the following principles should be followed in the design of core box through research:
(1) The size of the core made from the core box must be accurate. The shrinkage of glh-5 high chromium alloy is calculated as 2.0%;
(2) The core box shall be easy to handle, assemble and disassemble, and the labor intensity and technical requirements of workers shall be minimized;
(3) the core box assembly process is convenient for positioning of foam foam blades, ensuring accurate positioning of foam and ensuring the accuracy of sand core.
(4) In the process of sand filling, it is required to make the sand filling fully, evenly and without dead angle.
The core box is designed according to the above principles, and the preliminary scheme is shown in the figure:
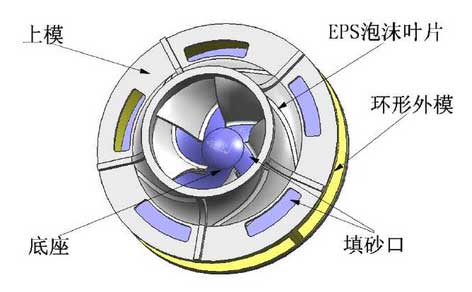
The whole core box is divided into three parts: upper mold, annular outer mold and base, which are made of cast aluminum. The three parts are connected by bolts and positioned by pins. In order to locate five blades of foam, five deep 20mm positioning grooves were designed on the base, and five positioning holes were designed in the upper mold to ensure the accurate positioning of the foam blades. The positioning design is shown in the diagram. When molding, the annular outer mold and the base are fixed first, then five foam blades are inserted into the positioning groove of the base in turn, and finally the upper mould is closed, and the foam blade is inserted into the positioning slot of the upper cover. When filling sand, it can be filled through the sand filling port reserved on the upper mold. The diameter of the larger sand filling port in the middle is φ 590mm, which can ensure the sand filling in the center area surrounded by the blades. In addition, five fan-shaped sand filling openings are distributed near the edge of the upper cover, which can ensure that the sand filling in the outside area of the five blades is sufficient.
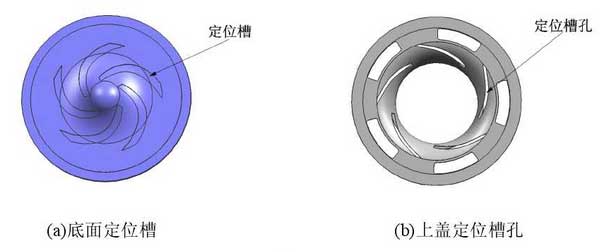
The design structure is simple, and assembly and disassembly are relatively easy, which ensures that the sand filling is full and uniform, and the foam positioning is more accurate. However, there are still some problems in the actual production: in the upper mold installation process, five foam blades are required to be inserted into the positioning slot at the same time to complete the installation, and there is pin location between the upper die and the outer ring mold, so there is a serious over location in the installation process of the upper die, which brings difficulty to the assembly of the core box. In addition, at the end of core making, since the shape of the sand core is tapered as shown in figure (a), it is impossible to take out the sand core from the upper mold side, so it is necessary to take out the sand core from the base side, which brings troubles to the core taking.
According to the above problems, the original scheme is improved. As shown in the figure, the upper cover is divided into five parts, each part corresponding to a foam blade. In addition, the auxiliary support is added to assist the installation and positioning, and the sand filling is removed after the installation. Installation of each part requires only one foam and side pin to reduce installation difficulty. In order to solve the problem of difficult coring in the initial process, the annular outer die is divided into two parts so that when coring, the annular die can be opened and taken out.
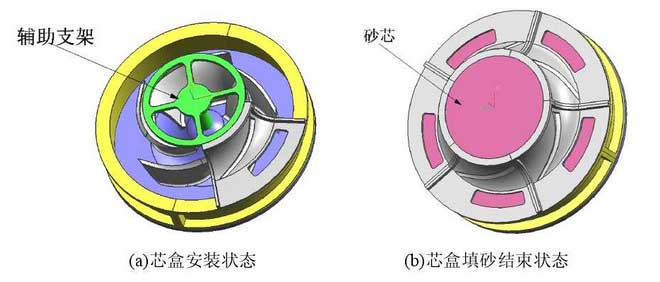
The improved core box solves the problems of the initial design, such as the difficulty of the upper mold installation and the difficulty of the core taking. After the use, it is proved that the design effect is achieved and the qualified whole sand core is successfully produced.