This article focuses on the research of the casting process of pump body based on sand 3D printing technology. It details the design of the pump body structure and the ,the scheme design and simulation analysis, as well as the practical verification process. By using AnyCasting software for numerical simulation analysis of different gating schemes, the side-pouring scheme was determined as the best choice. The application of 3D printing technology in sand mold production significantly shortened the mold-making time, and the combination of numerical simulation and 3D printing technology greatly reduced the development and trial production cycle of new castings, improving production efficiency.
1. Introduction
In recent years, 3D printing technology has been developing rapidly and has been widely applied in various fields. In the field of casting, the combination of 3D printing and traditional casting methods has brought revolutionary changes. This article takes the pump body as the research object to explore the specific application of 3D printing in the sand mold casting process.
2. Pump Body Structure and Design
2.1 Pump Body Structure
The three-dimensional model of the pump body is shown in Figure 1. It belongs to the shell-like castings with an asymmetric structure. The overall dimensions of the pump body are 410 mm × 503 mm × 170.5 mm, and the net weight is 57 kg, which can be classified as a small casting. The material used for the pump body is HT200.
2.2 Determination of
The selection of the 分型面 greatly affects whether the sand mold can be successfully assembled after printing and the quality of the castings after pouring. Therefore, the following aspects need to be considered when choosing the :
- The fewer the sand molds, the lower the error generated during the assembly and pouring process, and the easier it is to assemble the sand molds. Thus, it is necessary to minimize the number of when designing the sand molds.
- Practical pouring experience shows that in cases where the internal or surface of the poured part has a relatively complex structure and a thin wall thickness, these parts should be placed on one of the sand mold blocks as much as possible.
- When 分型 the sand mold, considerations need to be given to later handling and assembly issues. It is necessary to design handling and assembly grasping points on the upper and lower molds of the sand mold, and these points should have sufficient strength.
Unlike the traditional sand mold turning process that requires the use of sand boxes, in sand 3D printing, the 分型面 only needs to give priority to whether the final sand mold can be successfully assembled. Additionally, most castings usually select the 分型面 at the largest cross-sectional area of the casting. Therefore, the 分型面 of this casting is selected at the largest cross-sectional area of the casting, as shown in Figure 2. Through three-dimensional software modeling, this scheme can be successfully assembled.
3. Scheme Design and Simulation Analysis
3.1 Design of Gating System Schemes
Three sets of gating schemes were designed for the pump body’s gating system, including top-pouring, side-pouring, and bottom-pouring, as shown in Figure 3.
3.2 Simulation Analysis of Filling Process
The AnyCasting software was used for the casting simulation analysis of the pump body. During the simulation analysis process, the location and size of the defects generated after the casting was completed could be visually observed. Through numerical simulation, defects could be predicted, the qualification rate of the castings could be improved, and the production cost could be reduced.
The interior of the pump body is an irregular cavity with varying wall thicknesses. Based on the overall dimensions of the castings, it was evenly divided into 1 million regular cube grids, with an average size of each cube grid being 5.6 mm × 5.6 mm × 5.6 mm, as shown in Figure 4. The casting process parameters are presented in Table 1.
3.2.1 Simulation Analysis of Top-Pouring Scheme
The overall solidification sequence of the top-pouring gating system is from top to bottom and from the outside to the inside. Excluding the riser and the gate, the outer wall of the pump body casting is thinner, so it cools first, while the interior of the pump body casting cools last, as shown in Figure 5(a). Through the analysis of the combined defect parameters, it was analyzed that defects might occur on the outer wall of the casting and at the riser, as shown in Figure 5(b). Through the shrinkage porosity analysis of the workpiece using the probability defect parameters, it was found that there were defects in the outer wall and the interior of the casting, as shown in Figure 5(c).
3.2.2 Simulation Analysis of Side-Pouring Scheme
The overall solidification sequence of the side-pouring gating system is also from top to bottom and from the outside to the inside. However, the solidification trend is not uniform. Regardless of the riser and the gate, the outer wall of the pump body casting is thinner, so it cools first, while the interior of the pump body casting cools last, as shown in Figure 6(a). Observing the combined defect prediction diagram in Figure 6(b) and the shrinkage porosity fraction diagram in Figure 6(c), it was found that after solidification, shrinkage porosity defects occurred at the riser. Also, the defects were basically not on the casting itself, so it did not affect the quality of the casting.
[Insert pictures of the side-pouring simulation analysis here]
3.2.3 Simulation Analysis of Bottom-Pouring Scheme
The overall solidification sequence of the bottom-pouring gating system is also from top to bottom and from the outside to the inside, but the place near the gating system cools more slowly, as shown in Figure 7(a). Observing the combined defect prediction diagram in Figure 7(b) and the shrinkage porosity fraction diagram in Figure 7(c), it was found that defects occurred at the place where the riser and the casting were joined near the casting system, and there were shrinkage porosity in the middle hole wall and the plane. When using the bottom-pouring gating system, the bottom runner had poor heat dissipation, and the melt flow rate was slower, resulting in casting defects.
Based on the analysis results of the simulated pouring schemes, it can be concluded that the defects of the side-pouring gating system were concentrated at the riser, while there were almost no defects in the casting itself. Therefore, the side-pouring gating scheme was selected. Nine risers were chosen and placed on the surface of the later workpiece that needed processing, with the same height as the gate plane, which was sufficient for the gas to be smoothly discharged and for smooth feeding.
4. Practical Verification
Due to the complex structure of the castings and the difficulty in molding, the 3D printing method was adopted to print the sand core, as shown in Figure 8. When printing the sand core, the designed size of the sand core cone table could enhance the core’s fixed strength and facilitate placement. The sand mold was divided into 2 pieces. Considering economic benefits, the printed sand mold could optimize the wall thickness of the sand mold under the premise of ensuring strength, reducing the amount of sand used.
The printing of the sand mold was completed in the Longyuan AFS-J1600 forming printer. After testing, the final determined layer thickness of this printing process was 0.4 mm, and the scanning line width was 1.5 mm. After setting the printing parameters, the designed sand mold was output as an STL file and underwent layering processing, and slicing was performed using Magics, with the slice settings as shown in Figure 9. Then, the sliced model output by Magics in the cli format was imported into the AFS-J1600 printer for printing.
After the printing was completed, a vacuum cleaner was used to clean the unbonded and solidified dry sand in the sand mold, supplemented by a dust blower for cleaning. The sand mold after the cleaning work was completed is shown in Figure 10. Before pouring, zircon powder needed to be sprayed on the pouring surface of the sand mold to improve the surface quality of the castings and reduce the gas evolution for obtaining higher-quality castings after pouring. The raw material used for pouring was HT200, the pouring temperature was 1,450 °C, and the pouring time was 18 s.
[Insert a picture of the completed sand mold here]
After the castings cooled, the outer sand mold was knocked off to obtain a casting without obvious defects. The casting after removing the riser and the gating system is shown in Figure 11. After inspection, the quality of the castings was found to be qualified, with no obvious shrinkage porosity on the surface, and the surface quality was good.
5. Conclusion
By using the AnyCasting software to conduct numerical simulation analysis of the side-pouring, top-pouring, and bottom-pouring gating schemes of the pump body, the side-pouring scheme was determined as the best gating scheme, shortening the mold trial period. The adoption of 3D printing technology for making the sand mold could significantly shorten the sand mold production time. The combination of numerical simulation technology and sand 3D printing technology could greatly shorten the development and trial production cycle of new castings, improving production efficiency.
6. 3D Printing in the Field of Casting
6.1 Advantages of 3D Printing in Casting
3D printing technology offers several significant advantages in the casting field. Firstly, it eliminates the need for creating a master mold, reducing production costs. Secondly, it enables the manufacturing of sand molds and cores with arbitrary shapes through 3D printing technology, providing greater design flexibility. Moreover, the sand molds and cores produced have high precision, which leads to improved quality of the final castings. Compared to traditional casting methods, 3D printing technology results in a marked increase in casting quality and production efficiency.
6.2 Application Cases
6.2.1 Case 1: 3D Printing in the Production of High-Performance Pump Shell Castings by Western Heavy Industry
In the precision casting branch factory of Western Heavy Industry Co., Ltd. of Jiugang Group, a 2.5-meter-long, 1.5-meter-wide, and 1-meter-high 3D printer is in operation. After a dozen or so hours, a 3D-printed sand mold of an engine cylinder takes shape. Through processes such as sand blowing, pouring, and cooling, a finished engine cylinder can be released and enter the market.
The 3D casting sand mold printing process features high precision, a short cycle, and high process flexibility. In recent years, Western Heavy Industry has utilized this process to explore the high-end casting market, achieving short-process and batch production of single-piece and small-batch high-end castings. This further releases the technological innovation vitality, enhances product added value, and promotes the advancement of traditional casting to the mid-to-high end.
6.2.2 Case 2: 3D Printing in the Transformation of Kangshuo Electrical Group
Kangshuo Electrical Group started from traditional trade and decided to enter the manufacturing industry to create its own “signature” products. After purchasing 3D printing equipment from abroad, they initially focused on the jewelry industry but faced intense competition. Subsequently, they shifted their attention to the industrial parts casting field.
With the support of a joint innovation project, Kangshuo initiated the sand 3D printing project in 2018 and settled in Gaoping City, Shanxi Province, which has a traditional casting advantage, becoming a chain leader enterprise to facilitate the intelligent transformation and upgrading of local traditional casting enterprises. Their main business involves manufacturing sand molds using 3D printing technology to assist clients in casting key components such as engine cylinder heads, aerospace engine blades, and gearboxes.
[Insert pictures of the sand mold printing process and the products in Kangshuo Electrical Group]
6.2.3 Case 3: 3D Printing in the First 3D Printing Green Intelligent Foundry Factory in Our Province
In the 3D printing intelligent foundry factory of a certain enterprise, the traditional image of the “bulky and rough” casting industry has been broken. By introducing the largest domestic sand 3D printing equipment, the foundry industry has transformed into a “graceful” one.
Engineers need to design the corresponding three-dimensional digital model of the product before the 3D printer forms the sand mold. Compared to the traditional method of handcrafting a wooden mold to form castings, which is time-consuming and has low accuracy, the 3D printer can print out the sand core according to the designed parameters, and then pour molten iron or steel to complete the process, significantly reducing the time and cost.
7. Challenges and Prospects
Although 3D printing technology has brought many benefits to the casting industry, there are still some challenges that need to be addressed. For example, the cost of 3D printing equipment and materials can be relatively high, which may limit its wide application in some enterprises. Additionally, the performance and durability of the castings produced by 3D printing still need further verification and improvement.
However, with the continuous development and innovation of technology, the prospects of 3D printing in the casting field are very promising. In the future, we can expect further improvements in the accuracy and surface quality of 3D-printed castings. Moreover, the combination of 3D printing with other advanced technologies, such as intelligent control and monitoring systems, will likely bring more possibilities and potential to the casting industry.
In conclusion, 3D printing technology has brought revolutionary changes to the traditional casting industry. By optimizing the casting process, improving production efficiency, and enhancing the quality of castings, it provides a new way for the development and innovation of the casting industry. However, in the process of application and promotion, it is necessary to continuously address the existing challenges and explore new development opportunities to achieve more sustainable and high-quality development in the casting field.
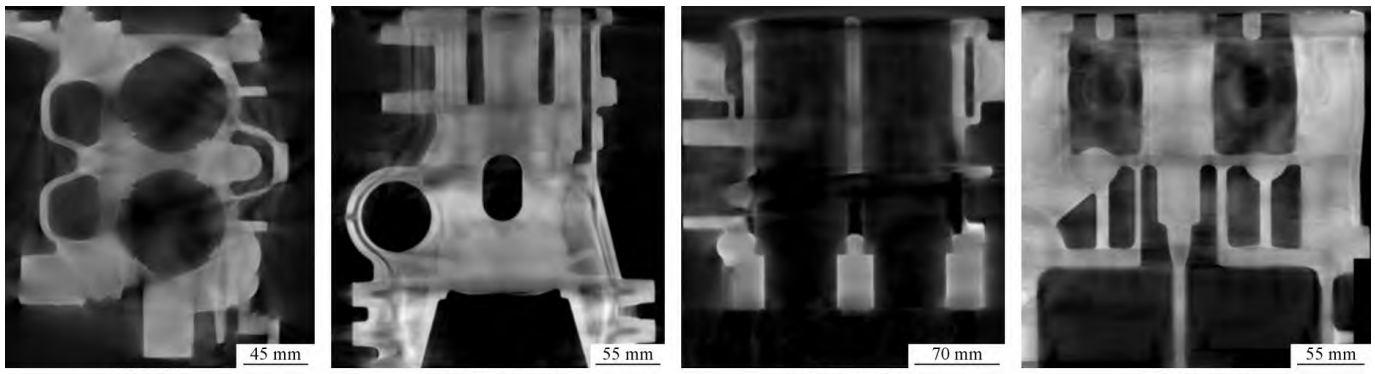