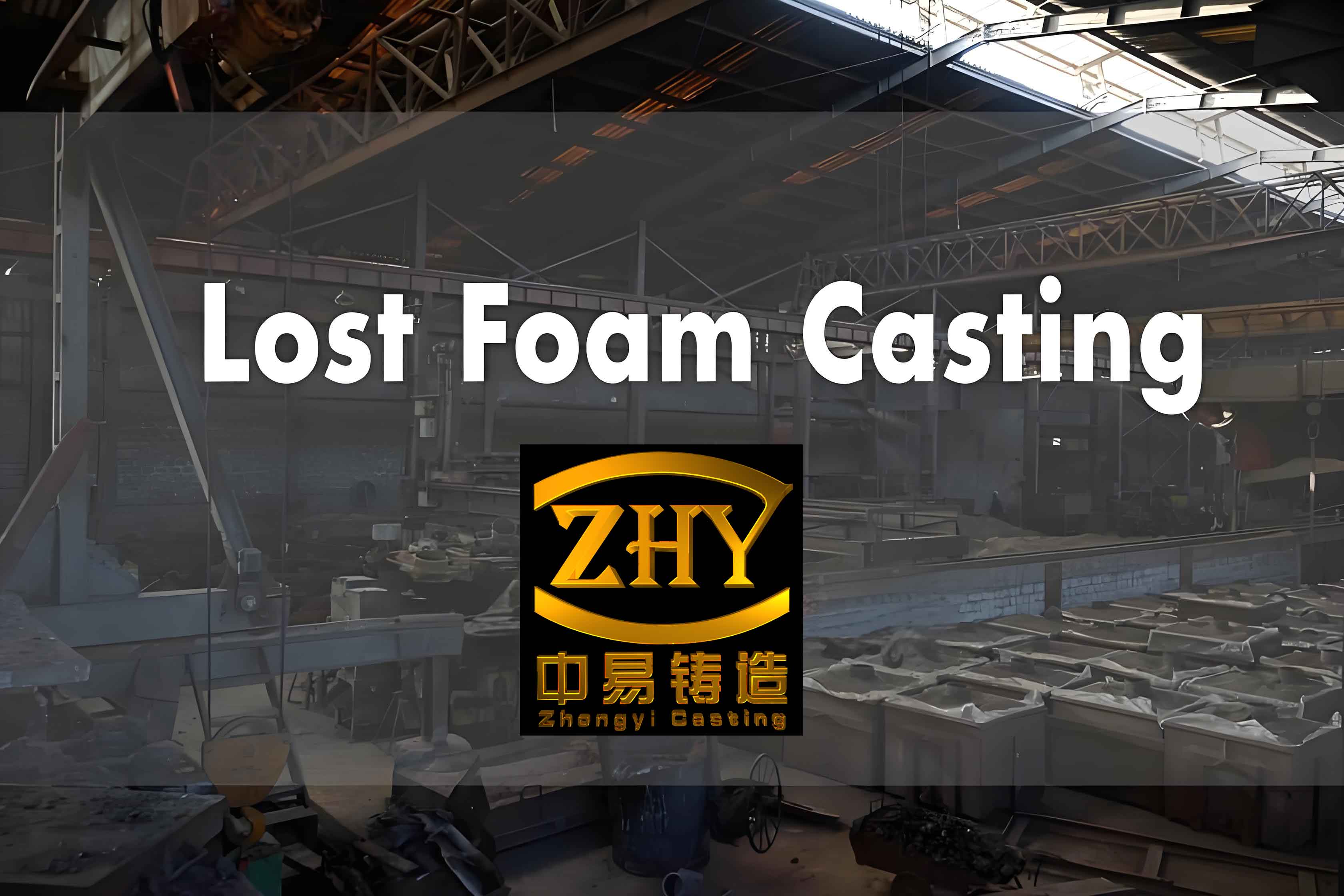
The electric vehicle industry is at the forefront of innovation, driving significant advancements in technology and manufacturing processes. One such manufacturing process that has gained considerable attention is lost foam casting. Lost foam casting offers numerous benefits, including enhanced component quality and cost reduction, making it an ideal choice for the production of electric vehicle components. This article explores the role of lost foam casting in the electric vehicle industry, highlighting its advantages, applications, and the steps involved in the process.
Benefits of Lost Foam Casting in Electric Vehicle Manufacturing
Lost foam casting presents several benefits that make it particularly advantageous for the electric vehicle industry:
- Design Flexibility: Lost foam casting allows for the creation of intricate and complex designs, which is essential for producing advanced electric vehicle components.
- Weight Reduction: The ability to cast thin-walled and lightweight components contributes to the overall reduction of the electric vehicle’s weight, improving efficiency and performance.
- Cost Savings: Lost foam casting reduces the need for extensive machining and assembly, leading to significant cost savings in the production of electric vehicle components.
- High Precision: The process ensures high dimensional accuracy and superior surface finish, which are crucial for the performance and reliability of electric vehicle components.
- Material Efficiency: The precise molding of metal around the foam pattern minimizes material waste, contributing to more sustainable manufacturing practices.
Applications of Lost Foam Casting in Electric Vehicle Industry
Lost foam casting is employed in various applications within the electric vehicle industry due to its versatility and precision. Key applications include:
- Motor Housings: Electric vehicle motors require high-precision housings that can be efficiently produced using lost foam casting.
- Battery Enclosures: The intricate designs of battery enclosures benefit from the design flexibility and precision offered by lost foam casting.
- Inverter and Converter Casings: These components, essential for the functioning of electric vehicles, can be cast with high dimensional accuracy using lost foam casting.
- Suspension Components: Lightweight and durable suspension components can be produced, enhancing the overall performance of electric vehicles.
- Cooling Systems: Complex cooling system parts, necessary for maintaining optimal temperatures in electric vehicles, are ideal candidates for lost foam casting.
Steps Involved in Lost Foam Casting for Electric Vehicle Components
The lost foam casting process involves several detailed steps to ensure the production of high-quality electric vehicle components. The following table outlines the key steps involved in this process:
Step | Description |
---|---|
Pattern Creation | A foam pattern is created, typically using expanded polystyrene (EPS), representing the exact shape of the final electric vehicle component. |
Pattern Assembly | Multiple foam patterns can be assembled into a cluster, known as a tree, to allow for the simultaneous casting of multiple components. |
Coating | The foam pattern is coated with a refractory material to enhance the surface finish and dimensional accuracy of the final product. |
Mold Preparation | The coated pattern is placed in a flask and surrounded by unbonded sand, which provides support and maintains the shape during casting. |
Metal Pouring | Molten metal is poured into the mold, causing the foam pattern to vaporize and the metal to take its place, forming the desired component. |
Cooling and Solidification | The mold is allowed to cool, and the metal solidifies into the shape of the original foam pattern. |
Cleaning and Finishing | The cast metal component is removed from the mold, cleaned, and any necessary finishing processes, such as machining or heat treatment, are performed. |
Comparative Analysis of Casting Methods for Electric Vehicle Components
To better understand the unique advantages of lost foam casting, it is useful to compare it with other common casting methods used in the electric vehicle industry. The table below provides a comparative analysis of lost foam casting, sand casting, and investment casting:
Feature | Lost Foam Casting | Sand Casting | Investment Casting |
---|---|---|---|
Design Complexity | High | Medium | High |
Weight Reduction | Significant | Moderate | Significant |
Surface Finish | Excellent | Fair | Excellent |
Dimensional Accuracy | High | Medium | High |
Material Waste | Low | Medium | Low |
Cost | Moderate | Low | High |
Environmental Impact | Low | Medium | Low |
Challenges and Future Prospects in Electric Vehicle Manufacturing
While lost foam casting offers numerous advantages for the electric vehicle industry, it also presents certain challenges that manufacturers must address:
- Pattern Fragility: Foam patterns can be delicate and require careful handling to avoid damage during the casting process.
- Process Control: Precise control of temperature and mold conditions is crucial for ensuring consistent quality in the final electric vehicle components.
- Initial Setup Cost: The initial costs for pattern creation and coating can be higher compared to some traditional casting methods.
Despite these challenges, the future prospects for lost foam casting in the electric vehicle industry are promising. Advancements in foam materials, coating technologies, and automation are expected to further enhance the efficiency and application scope of this casting method. As the electric vehicle industry continues to grow, the demand for high-quality, cost-effective components will drive further innovation and adoption of lost foam casting.
Conclusion
In conclusion, lost foam casting plays a crucial role in the electric vehicle industry by enhancing component quality and reducing costs. Its ability to produce intricate, lightweight, and high-precision components makes it an ideal choice for electric vehicle manufacturers. As technology continues to evolve, lost foam casting is poised to become an even more integral part of electric vehicle manufacturing, driving innovation and efficiency in the production of essential components. The future of lost foam casting in the electric vehicle industry looks bright, promising continued advancements and improvements in manufacturing processes.