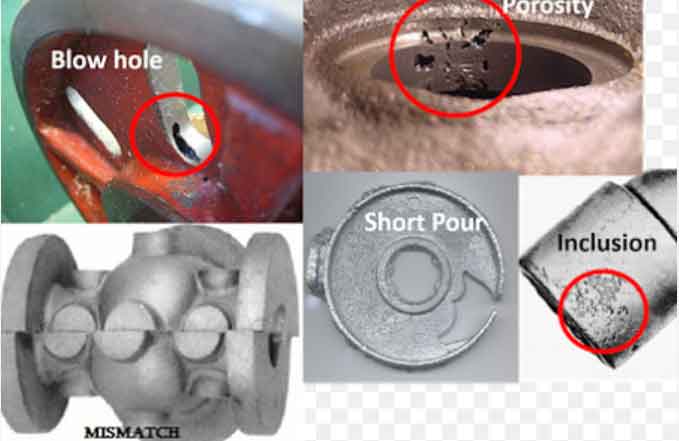
Taking proactive measures for casting defect prevention and control is essential to ensure high-quality castings and minimize the occurrence of defects. By implementing preventive strategies throughout the casting process, manufacturers can improve efficiency, reduce costs, and enhance customer satisfaction. This article highlights key proactive measures that can be employed for effective casting defect prevention and control.
- Robust Design and Engineering:
- Start with a robust design and engineering process that considers casting feasibility, material selection, component geometry, and mold design. Involve experienced design engineers who are knowledgeable about casting processes to optimize the design for manufacturability and minimize the risk of defects.
- Material Quality Control:
- Establish strict material quality control measures, including thorough inspection and testing of incoming raw materials. Ensure that the materials meet the required specifications and have consistent properties to minimize defects caused by material inconsistencies.
- Process Optimization:
- Optimize the casting process parameters to reduce the likelihood of defects. This includes controlling variables such as pouring temperature, cooling rates, solidification time, and mold and core materials. Utilize computer simulations, experimental trials, and historical data analysis to identify optimal process conditions.
- Robust Gating and Riser Systems:
- Design gating and riser systems that promote smooth metal flow, proper filling, and effective feeding during solidification. Optimize the size, shape, and placement of gates and risers to minimize defects such as shrinkage, porosity, and misruns.
- Mold and Core Design:
- Optimize mold and core design to ensure proper venting, minimize turbulence, and promote uniform cooling and solidification. Consider factors such as mold material, surface finish, and core venting to reduce the risk of defects like gas porosity, surface roughness, and dimensional inaccuracies.
- Quality Control at Each Stage:
- Implement comprehensive quality control measures at each stage of the casting process. Conduct visual inspections, dimensional measurements, and non-destructive testing (NDT) to detect and eliminate defects. Regularly monitor process parameters and take corrective actions as necessary.
- Employee Training and Skill Development:
- Provide comprehensive training programs for operators, technicians, and quality control personnel involved in the casting process. Enhance their knowledge and skills in defect recognition, process optimization, and problem-solving techniques. Empower employees to identify and address potential issues proactively.
- Continuous Improvement Culture:
- Foster a culture of continuous improvement by encouraging employees to actively participate in defect prevention initiatives. Establish feedback mechanisms, conduct regular defect analysis, and implement corrective actions based on lessons learned. Encourage cross-functional collaboration and knowledge sharing.
- Supplier Collaboration:
- Collaborate closely with material suppliers, tooling manufacturers, and equipment suppliers to ensure the quality and reliability of the supplied components. Establish clear communication channels, conduct regular audits, and maintain strong relationships to address any potential issues.
- Documentation and Analysis:
- Maintain detailed documentation of the casting process, including process parameters, inspection results, and corrective actions taken. Analyze defect data to identify trends and patterns, and use this information to drive continuous improvement efforts.
Proactive measures for casting defect prevention and control are essential for achieving high-quality castings and optimizing production processes. By focusing on robust design and engineering, material quality control, process optimization, and comprehensive quality control measures, manufacturers can minimize defects and improve overall casting performance. Emphasizing employee training, fostering a culture of continuous improvement, and collaborating with suppliers contribute to ongoing defect prevention and control. With a proactive approach, manufacturers can enhance efficiency, reduce costs, and deliver reliable and high-quality castings to meet customer expectations.