Chapter 1: The Basic Characteristics of Ductile Iron Castings
Ductile iron castings, also known as nodular iron or spheroidal graphite iron (SGI), are a type of cast iron that exhibits enhanced mechanical properties and improved ductility compared to traditional gray iron. Ductile iron is wcastings idely used in various industries due to its combination of strength, toughness, and cost-effectiveness. Here are the basic characteristics of ductile iron castings:
1. Alloy Composition:
- Ductile iron castings is primarily composed of iron (Fe) along with varying amounts of carbon (C), silicon (Si), manganese (Mn), sulfur (S), and phosphorus (P).
- The addition of small amounts of magnesium (Mg) or cerium (Ce) in the alloy promotes the formation of graphite nodules, which give ductile iron castings its distinctive microstructure.
2. Microstructure:
- The microstructure of ductile iron castings consists of graphite nodules embedded within a matrix of ferrite and pearlite phases.
- The graphite nodules provide a more continuous and interconnected structure compared to the flake graphite in gray iron.
- The nodular graphite morphology imparts ductility to the material, allowing it to deform and absorb energy before failure.
3. Mechanical Properties:
- Ductile iron castings exhibits a combination of high strength, good ductility, and excellent impact resistance.
- Its mechanical properties are influenced by factors such as the nodularity of graphite, matrix structure, and heat treatment.
- Ductile iron castings has higher tensile strength, yield strength, and elongation compared to gray iron.
4. Performance and Applications:
- The improved mechanical properties of ductile iron castings make it suitable for applications requiring high load-bearing capacity, shock absorption, and wear resistance.
- Ductile iron castings are commonly used in automotive components, machinery parts, gears, pipes, valves, and other industrial components.
- The ductility of the material allows for intricate shapes and complex designs, making it versatile for various engineering applications.
5. Heat Treatment:
- Heat treatment processes such as annealing, normalizing, and quenching can be applied to ductile iron castings to further refine its microstructure and enhance mechanical properties.
- Heat treatment can improve strength, hardness, and wear resistance, depending on the specific application requirements.
6. Corrosion Resistance:
- Ductile iron castings has good corrosion resistance, particularly in environments where the presence of water or moisture is common.
- Protective coatings, such as epoxy or zinc coatings, can be applied to enhance its corrosion resistance further.
7. Machinability:
- Ductile iron castings is generally considered to have good machinability due to its softer matrix compared to other cast irons.
Ductile iron castings are favored in applications where a balance between strength, toughness, and cost-effectiveness is required. Its unique microstructure and mechanical properties contribute to its widespread use in a variety of industries, including automotive, machinery, construction, and infrastructure.
Chapter 2: The Advantages and Disadvantages of Ductile Iron Castings
Ductile iron castings offer several advantages and disadvantages that make them suitable for various applications. Here’s an overview of the pros and cons of using ductile iron castings:
Advantages of Ductile Iron Castings:
- High Strength and Durability: Ductile iron castings have higher tensile strength and yield strength compared to other cast iron types, making them suitable for applications requiring structural integrity and load-bearing capacity.
- Excellent Ductility: Ductile iron castings is more ductile and less brittle than other cast iron types, allowing for greater deformation before failure and enhancing resistance to sudden impacts or shock loads.
- Good Impact Resistance: The presence of graphite nodules in ductile iron castings contributes to excellent impact resistance, making it suitable for components subjected to dynamic loads and vibration.
- Versatility in Design: Ductile iron castings flexibility allows for intricate and complex shapes to be cast, providing design freedom and the ability to create parts with complex geometries.
- Machinability: Ductile iron castings can be easily machined, offering good surface finish and dimensional accuracy after machining operations.
- Cost-Effective: Ductile iron castings is often more cost-effective than steel and can be a suitable substitute for steel components, providing a balance between performance and cost.
- Excellent Heat Treatment Response: Ductile iron castings can be heat-treated to achieve desired mechanical properties, allowing for tailoring the material to specific application requirements.
Disadvantages of Ductile Iron Castings:
- Brittleness at Low Temperatures: Ductile iron castings can exhibit brittle behavior at low temperatures, affecting its impact resistance in cold environments.
- Less Wear Resistance: While ductile iron castings has good wear resistance, it may not be as wear-resistant as some other materials, especially under abrasive conditions.
- Lower Machinability than Gray Iron: Ductile iron castings can be more challenging to machine than gray iron due to its higher strength, requiring specialized tools and techniques.
- Limited Corrosion Resistance: Ductile iron castings is susceptible to corrosion, particularly in aggressive environments, and may require additional coatings or protective measures to enhance its corrosion resistance.
- Casting Complexity: While ductile iron castings can be cast into intricate shapes, the casting process may be more complex and require careful consideration of gating and risering systems.
- Lower Thermal Conductivity: Ductile iron castings has lower thermal conductivity compared to other metals like aluminum, which can affect its performance in applications involving heat transfer.
- Environmental Impact: Like other metal production processes, the manufacturing of ductile iron castings can have environmental implications, particularly in terms of energy consumption and emissions.
It’s important to note that the advantages and disadvantages of ductile iron castings can vary depending on the specific application, design considerations, and material selection factors. Proper engineering and material selection are essential to ensure that ductile iron castings meet the requirements of the intended use.
Chapter 3: The Alloy Composition of Ductile Iron Castings
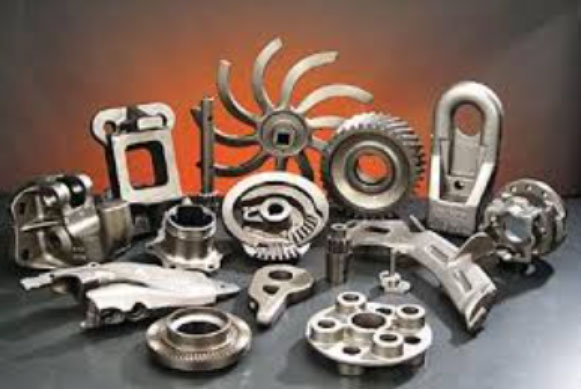
The alloy composition of ductile iron castings plays a crucial role in determining their mechanical properties, microstructure, and overall performance. Here are the main alloying elements found in ductile iron castings and their impact on the properties of the castings:
1. Carbon (C):
- Carbon is a key element in ductile iron castings, contributing to its strength and hardness.
- An appropriate carbon content is essential to achieve the desired matrix structure (ferrite and pearlite) and mechanical properties.
- Too high a carbon content can lead to excessive hardness and brittleness, while too low a content may result in insufficient strength.
2. Silicon (Si):
- Silicon is a strong graphitizing element that promotes the formation of graphite nodules in ductile iron castings.
- Silicon also enhances fluidity during casting and improves resistance to thermal and mechanical stresses.
- Proper silicon content helps achieve a well-distributed and spherical graphite structure, which enhances ductility.
3. Manganese (Mn):
- Manganese contributes to the strength and hardenability of ductile iron castings.
- It helps control the formation of pearlite, and higher manganese levels can improve the tensile strength and wear resistance of the castings.
4. Nickel (Ni) and Copper (Cu):
- These elements are often added in small amounts to improve specific properties.
- Nickel enhances toughness and impact resistance, especially at lower temperatures.
- Copper can improve corrosion resistance and thermal conductivity.
5. Traces of Other Elements:
- Traces of elements such as chromium (Cr), molybdenum (Mo), and vanadium (V) may be added for specific applications to enhance properties such as wear resistance, heat resistance, and corrosion resistance.
Impact on Properties:
- Proper alloying elements and their concentrations contribute to the formation of nodular graphite, which imparts ductility to the iron.
- The matrix structure of ferrite and pearlite provides a good balance between strength and toughness.
- Alloying elements influence mechanical properties such as tensile strength, yield strength, elongation, and impact resistance.
- The alloy composition affects heat treatment response, allowing for adjustments in hardness and microstructure.
- Corrosion resistance, wear resistance, and other specialized properties can be tailored through alloying.
It’s important to note that the specific composition of ductile iron castings may vary based on the intended application and casting requirements. Balancing these alloying elements and their concentrations is crucial to achieving the desired combination of mechanical properties and overall performance in ductile iron castings.
Chapter 4: The Microstructure of Ductile Iron Castings
The microstructure of ductile iron castings consists of two primary components: the structure of spherical graphite nodules and the matrix phase. The interaction between these components significantly influences the mechanical properties and overall performance of ductile iron castings.
1. Structure of Spherical Graphite Nodules:
- Ductile iron castings is characterized by the presence of graphite nodules, which are spherical in shape due to the addition of nodulizing agents during the casting process.
- The graphite nodules are embedded within the matrix phase and act as stress concentrators during deformation, enhancing the ductility and toughness of the material.
- The presence of spherical graphite nodules improves the ability of the material to absorb energy before fracture, making ductile iron castings less brittle compared to gray iron.
2. Matrix Phase:
- The matrix phase in ductile iron castings consists of a combination of ferrite and pearlite.
- Ferrite is a relatively soft phase that contributes to ductility and impact resistance.
- Pearlite is a harder phase formed by the eutectoid reaction of carbon and iron, contributing to strength and wear resistance.
- The proportion of ferrite and pearlite in the matrix influences the mechanical properties, with higher pearlite content providing increased hardness and strength.
Influence of Different Microstructural Types on Performance:
- Different microstructural types within ductile iron castings, characterized by the relative amounts of ferrite and pearlite, impact various properties:
- Predominantly Ferritic Microstructure: Offers excellent machinability, good ductility, and impact resistance, making it suitable for applications requiring vibration damping and shock absorption.
- Predominantly Pearlitic Microstructure: Provides higher strength, hardness, and wear resistance, suitable for applications where mechanical properties and abrasion resistance are critical.
- Mixed Microstructure: Combines the advantages of both ferritic and pearlitic microstructures, providing a balanced combination of strength, ductility, and wear resistance.
Performance Enhancement and Tailoring:
- The microstructure of ductile iron castings can be tailored through alloying and heat treatment processes to achieve desired mechanical properties.
- Alloying elements and heat treatment influence the distribution of ferrite and pearlite, allowing optimization of strength, hardness, and other properties.
In summary, the microstructure of ductile iron castings, characterized by the presence of spherical graphite nodules and the matrix phase, plays a vital role in determining the material’s mechanical properties, such as strength, ductility, hardness, impact resistance, and wear resistance. Different microstructural types can be chosen or engineered to suit specific application requirements, making ductile iron castings a versatile material for various industries.
Chapter 5: The Mechanical Properties of Ductile Iron Castings

Ductile iron castings exhibit a range of mechanical properties that make them suitable for a wide variety of applications. The mechanical properties of ductile iron castings are influenced by factors such as the alloy composition, microstructure, and heat treatment. Here are some key mechanical properties of ductile iron castings:
1. Hardness:
- Ductile iron castings typically has a hardness range of 170 to 260 HB (Brinell hardness), depending on the microstructure and heat treatment.
- Alloying elements and heat treatment can be adjusted to achieve specific hardness levels suitable for different applications.
2. Strength:
- Ductile iron castings has good tensile and yield strength compared to other cast iron types.
- Depending on the microstructure and alloying elements, ductile iron castings can have tensile strengths ranging from 400 to 1000 MPa.
3. Ductility:
- Ductile iron castings is named for its improved ductility compared to gray iron.
- The presence of spherical graphite nodules and a ferrite-pearlite matrix contributes to ductility, allowing for plastic deformation without catastrophic failure.
- Ductile iron castings typically has elongation values ranging from 10% to 30%, indicating its ability to withstand deformation before breaking.
4. Impact Toughness:
- The presence of graphite nodules helps absorb impact energy, improving the impact toughness of ductile iron castings.
- Ductile iron castings can exhibit Charpy impact values ranging from 20 J/cm² to 40 J/cm² or more, depending on microstructure and conditions.
5. Fatigue Resistance:
- Ductile iron castings exhibits good fatigue resistance, making it suitable for applications subjected to cyclic loading.
- The fatigue properties of ductile iron castings can be enhanced through heat treatment and alloying adjustments.
6. Wear Resistance:
- Ductile iron’s wear resistance depends on the microstructure, with pearlitic structures offering higher wear resistance than ferritic structures.
- Alloying elements like chromium, molybdenum, and nickel can be added to enhance wear resistance.
7. Creep Resistance:
- Ductile iron castings has good creep resistance at elevated temperatures, making it suitable for applications involving constant or cyclic loads at high temperatures.
It’s important to note that the mechanical properties of ductile iron castings can be tailored through alloying, heat treatment, and other processing techniques. This allows for the optimization of specific properties to meet the requirements of different industries and applications, ranging from automotive components to machinery parts and beyond.
Chapter 6: Corrosion Resistance of Ductile Iron Castings and Their Application in Corrosive Environments
Ductile iron castings can exhibit varying degrees of corrosion resistance depending on factors such as alloy composition, microstructure, and environmental conditions. While ductile iron castings is generally less corrosion-resistant than materials like stainless steel or certain non-ferrous alloys, it can still be suitable for many corrosive environments with proper design and protective measures.
Corrosion Mechanisms in Ductile Iron castings: Ductile iron castings is susceptible to several corrosion mechanisms, including:
- Uniform Corrosion: This is a general corrosion process that affects the entire surface of the material and can occur in various environments.
- Pitting Corrosion: Localized corrosion that forms pits or cavities on the surface of the material, which can lead to localized weakening.
- Microbiologically Influenced Corrosion (MIC): Corrosion caused or accelerated by the activity of microorganisms, such as bacteria or fungi, often seen in water or sewage systems.
- Crevice Corrosion: Occurs in confined spaces or crevices where oxygen availability is limited, leading to accelerated corrosion in these areas.
Application of Ductile Iron Castings in Corrosive Environments: Ductile iron castings are commonly used in various industries and applications where they may be exposed to corrosive environments. Some examples include:
- Water and Wastewater Systems: Ductile iron castings is often used in water distribution pipes, sewage systems, and wastewater treatment facilities. Proper coatings and linings can enhance corrosion resistance.
- Marine and Offshore Structures: Ductile iron castings components are used in marine environments, such as shipbuilding and offshore platforms. Proper corrosion-resistant coatings are essential in these applications.
- Chemical Processing: Ductile iron castings may be used in chemical processing equipment, where compatibility with specific chemicals and protective coatings is crucial.
- Agricultural Equipment: Ductile iron castings is used in agricultural machinery and equipment that can be exposed to corrosive substances in fertilizers and soil.
- Mining Industry: Components in the mining sector, such as pumps and valves, can be exposed to abrasive and corrosive materials.
Measures to Improve Corrosion Resistance:
- Coatings and Linings: Applying appropriate coatings, such as epoxy, polyurethane, or fusion-bonded epoxy coatings, can enhance corrosion resistance in ductile iron castings.
- Cathodic Protection: Using sacrificial anodes or impressed current systems can provide cathodic protection to prevent or slow down the corrosion process.
- Material Selection: Utilizing ductile iron castings alloys with higher corrosion resistance, such as those containing alloying elements like chromium, molybdenum, and nickel, can improve performance.
- Proper Design: Design features that prevent water accumulation, eliminate crevices, and facilitate drainage can reduce the risk of corrosion.
- Regular Maintenance: Regular inspection, cleaning, and maintenance can help identify and address corrosion-related issues in a timely manner.
It’s important to consider the specific corrosive environment, exposure conditions, and industry standards when selecting and using ductile iron castings in corrosive applications. Consulting with materials and corrosion experts can help ensure the appropriate measures are taken to minimize corrosion and extend the service life of ductile iron castings components.
Chapter 7: The Wear Resistance of Ductile Iron Castings and Their Application in Wear Environments
Ductile iron castings can exhibit good wear resistance, making them suitable for applications where components are subjected to abrasive or erosive wear. The wear resistance of ductile iron castings is influenced by factors such as alloy composition, microstructure, and the presence of graphite nodules. While ductile iron castings may not have the same wear resistance as specialized wear-resistant alloys, it can still perform well in many wear environments when properly selected and treated.
Application of Ductile Iron Castings in Wear Environments: Ductile iron castings are used in a variety of industries and applications where wear resistance is important. Some examples include:
- Automotive Industry: Ductile iron castings is commonly used for the production of crankshafts, camshafts, gears, and other components that may experience sliding or rolling wear.
- Mining and Construction: Ductile iron castings is used in mining equipment components like crusher parts, grinding media, and earthmoving machinery components subjected to abrasive wear.
- Agricultural Machinery: Components such as tillage tools, plow shares, and wear plates may utilize ductile iron castings for improved wear resistance.
- Hydraulic Systems: Ductile iron castings can be found in hydraulic components like pump casings, valve bodies, and cylinders that may experience wear due to fluid flow.
- Pipelines and Pipe Fittings: Ductile iron pipes and fittings used in abrasive environments can benefit from the material’s wear resistance.
Enhancing Wear Resistance of Ductile Iron Castings:
- Alloy Composition: Alloying elements like chromium, molybdenum, and nickel can be added to ductile iron castings to improve wear resistance. These elements can form hard carbides or provide solid solution strengthening.
- Heat Treatment: Proper heat treatment processes, such as quenching and tempering, can improve the hardness and wear resistance of ductile iron castings.
- Surface Treatments: Applying surface treatments like hardfacing, nitriding, or carburizing can further enhance the wear resistance of ductile iron castings components.
- Graphite Nodularity: A high degree of graphite nodularity in the microstructure can contribute to better wear resistance by reducing stress concentrations and improving material toughness.
- Lubrication and Maintenance: Proper lubrication and maintenance practices can minimize friction and wear in ductile iron castings components.
- Material Selection: Selecting the appropriate ductile iron castings grade for the specific wear environment is crucial. Some grades are designed for enhanced wear resistance.
Considerations for Wear Applications:
While ductile iron castings can offer good wear resistance, it’s important to consider the specific wear mechanisms and conditions in the intended application. Factors such as sliding or impact wear, abrasive particle size and hardness, operating temperature, and load should be taken into account when selecting ductile iron castings for wear environments.
Collaboration with materials and engineering experts can help ensure that ductile iron castings are properly designed, treated, and maintained to deliver satisfactory wear performance in the desired application.
Chapter 8: Heat Treatment Methods for Ductile Iron Castings
Heat treatment plays a crucial role in enhancing the mechanical properties and microstructure of ductile iron castings. The specific heat treatment method applied depends on the desired properties and performance requirements of the castings. Here are some common heat treatment methods used for ductile iron castings:
- Annealing:
- Process: The casting is heated to a temperature below the eutectoid temperature (between 850°C and 950°C) and held for a specific time before slowly cooling in the furnace.
- Purpose: Annealing reduces internal stresses, refines the microstructure, and improves machinability and dimensional stability.
- Normalizing:
- Process: The casting is heated above the eutectoid temperature to transform the matrix into austenite and then air-cooled or cooled in still air.
- Purpose: Normalizing improves mechanical properties, particularly strength and hardness, by refining the microstructure and eliminating coarse graphite structures.
- Quenching and Tempering:
- Process: The casting is heated above the eutectoid temperature, quenched rapidly to form martensite, and then tempered by reheating to a lower temperature.
- Purpose: Quenching and tempering improve hardness, strength, and toughness by forming a controlled amount of martensite and tempering it to the desired properties.
- Stress Relief Annealing:
- Process: The casting is heated to a temperature below the eutectoid temperature and held to relieve residual stresses, followed by slow cooling.
- Purpose: Stress relief annealing reduces internal stresses introduced during casting, welding, or machining processes.
- Sub-Critical Annealing:
- Process: The casting is heated below the eutectoid temperature and held to refine the matrix and reduce graphite size.
- Purpose: Sub-critical annealing enhances ductility and machinability while maintaining a pearlitic microstructure.
- Induction Hardening:
- Process: Localized heating of specific areas, followed by rapid quenching, produces a hardened layer.
- Purpose: Induction hardening is used to improve wear resistance and surface hardness in selected regions of the casting.
- Surface Hardening Techniques (Carburizing, Nitriding, Flame Hardening, etc.):
- Process: The surface of the casting is modified to create a hardened layer using chemical or thermal methods.
- Purpose: Surface hardening improves wear resistance and surface properties without significantly altering the bulk properties.
It’s important to note that the heat treatment process and parameters should be carefully controlled to achieve the desired microstructure and properties while avoiding potential issues like distortion, cracking, or excessive hardness. The specific heat treatment method chosen will depend on factors such as the ductile iron castings grade, casting geometry, intended application, and performance requirements. Collaboration with materials and heat treatment experts is essential to ensure the successful heat treatment of ductile iron castings.
Chapter 9: The Casting Technology of Ductile Iron Castings
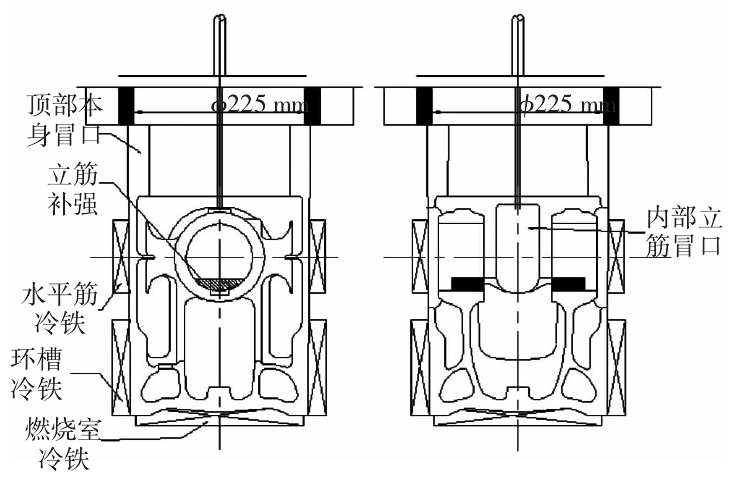
Ductile iron castings are commonly produced using various casting processes, including sand casting and investment casting. Each process has its own advantages and considerations when it comes to producing high-quality ductile iron castings.
1. Model Preparation:
- Model preparation involves creating a pattern or model of the desired ductile iron casting. The pattern can be made from wood, plastic, or other materials. It is a replica of the final casting and is used to create the mold.
2. Sand Casting:
- Sand casting is a widely used process for producing ductile iron castings. It involves the following steps:
- Mold Making: A mold is created by compacting sand around the pattern. The pattern is removed, leaving a cavity in the sand mold.
- Mold Assembly: The mold is typically made in two halves, which are assembled to create the complete mold cavity.
- Melting and Pouring: Molten ductile iron castings is prepared in a furnace and poured into the mold cavity.
- Solidification: The molten iron cools and solidifies within the mold, taking the shape of the desired casting.
- Cooling and Shakeout: After solidification, the mold is cooled, and the casting is removed by breaking the mold.
3. Investment Casting:
- Investment casting, also known as lost-wax casting, is another method used for ductile iron castings. The process involves the following steps:
- Model Creation: A pattern of the casting is made using wax, plastic, or other materials.
- Mold Building: The pattern is coated with ceramic shell material to create a mold.
- Wax Removal: The mold is heated to melt and remove the wax pattern, leaving behind a cavity.
- Pouring: Molten ductile iron castings is poured into the mold.
- Solidification and Cooling: The iron solidifies and cools within the mold.
- Shell Removal: After solidification, the ceramic shell is broken away to reveal the cast part.
Impact on Casting Quality:
- Both sand casting and investment casting can produce high-quality ductile iron castings, but the choice of process depends on factors such as complexity, size, quantity, and required surface finish.
- Proper mold design and gating system are essential to ensure even filling and minimize defects like porosity and shrinkage.
- Molten metal quality, pouring temperature, and pouring technique impact casting integrity and properties.
- Cooling rates during solidification influence the microstructure and mechanical properties of the casting.
- Post-casting processes, such as heat treatment and machining, may be necessary to achieve desired properties and dimensions.
The selection of the casting process depends on the specific requirements of the ductile iron casting, including its size, complexity, accuracy, surface finish, and production volume. Both sand casting and investment casting can provide excellent results when properly executed, and they are used in various industries where ductile iron’s mechanical properties are beneficial. It’s essential to work with experienced casting professionals to ensure the best possible outcome in terms of quality and performance.
Chapter 10: The Widespread Application of Ductile Iron Castings
Ductile iron castings have a wide range of applications across various industries due to their desirable combination of mechanical properties, including high strength, good ductility, and excellent wear resistance. Some of the common applications of ductile iron castings include:
1. Automotive Industry:
- Engine components: Ductile iron castings is used in the manufacturing of engine blocks, cylinder heads, crankshafts, and other parts due to its strength, durability, and resistance to thermal cycling.
- Suspension components: Ductile iron castings is used for various suspension parts, including control arms, knuckles, and steering components.
- Brake components: Ductile iron castings is employed for brake calipers, brackets, and other components due to its wear resistance and thermal conductivity.
2. Engineering Machinery:
- Construction equipment: Ductile iron castings are used in the construction of heavy machinery like excavators, bulldozers, loaders, and road rollers.
- Agricultural machinery: Tractors, plows, and other agricultural equipment often use ductile iron castings for their durability and wear resistance.
3. Pipeline Systems:
- Water and sewage systems: Ductile iron pipes and fittings are commonly used for water distribution, wastewater treatment, and sewage systems due to their corrosion resistance and high tensile strength.
- Gas distribution: Ductile iron castings is used for gas distribution pipelines due to its resistance to external loads and ability to handle high-pressure applications.
4. Pump and Valve Components:
- Pump housings: Ductile iron castings is used to manufacture pump housings for various industries, including water treatment, oil and gas, and chemical processing.
- Valve bodies: Valves in industrial applications use ductile iron castings for its strength and corrosion resistance.
5. Railway Industry:
- Railroad components: Ductile iron castings are used in the manufacturing of railway components such as railcar wheels, brake shoes, and couplings.
6. Construction and Infrastructure:
- Manhole covers and drainage grates: Ductile iron’s high strength-to-weight ratio makes it suitable for heavy-duty applications in urban infrastructure.
7. Energy Sector:
- Wind turbine components: Ductile iron castings are used in wind turbine hubs and other components due to their strength and fatigue resistance.
8. Mining and Material Handling:
- Mining equipment: Ductile iron castings are used in various mining machinery and equipment for their durability and wear resistance.
9. Marine and Naval Applications:
- Marine engine components: Ductile iron castings is used in marine engine parts, propellers, and other components exposed to harsh marine environments.
Ductile iron’s versatility, along with its ability to be easily machined and welded, makes it a popular choice for a wide range of applications in industries where high strength, toughness, and wear resistance are essential. It’s important to note that the specific properties and grades of ductile iron castings can be tailored to suit the requirements of each application.
Chapter 11: Quality Control Methods for Ductile Iron Castings
Quality control is crucial in ensuring the reliability and performance of ductile iron castings. Various methods are employed to ensure the quality of ductile iron castings throughout the manufacturing process. Some common quality control methods include:
1. Metallographic Analysis:
Metallographic analysis involves examining the microstructure of the ductile iron casting under a microscope. This analysis helps identify the distribution of graphite nodules, the matrix structure, and any potential defects or anomalies that may affect the mechanical properties of the casting.
2. Dimensional Measurement:
Dimensional measurement is performed using precision measuring instruments and techniques to verify that the casting’s dimensions conform to the required specifications. This includes measurements of length, width, height, diameters, and other critical dimensions.
3. Non-Destructive Testing (NDT):
NDT methods are employed to detect surface and subsurface defects without causing damage to the casting. Some common NDT techniques for ductile iron castings include:
- Visual inspection: Direct visual examination to identify surface defects.
- Magnetic Particle Testing (MT): Detects surface and near-surface defects using magnetic fields and magnetic particles.
- Ultrasonic Testing (UT): Uses ultrasonic waves to detect internal defects and measure wall thickness.
- Radiographic Testing (RT): Utilizes X-rays or gamma rays to detect internal defects such as porosity and inclusions.
- Dye Penetrant Testing (PT): Identifies surface defects by applying a dye that penetrates into surface cracks and defects.
4. Mechanical Testing:
Mechanical testing involves assessing the mechanical properties of the ductile iron casting, such as tensile strength, yield strength, elongation, hardness, and impact resistance. These tests ensure that the casting meets the specified mechanical requirements.
5. Chemical Composition Analysis:
Chemical composition analysis is performed to verify that the alloy composition of the ductile iron casting adheres to the required specifications. This analysis is essential to ensure that the material properties meet the desired standards.
6. Pressure Testing:
Pressure testing is conducted to check the casting’s integrity and leak resistance. Castings designed for pressure-containing applications, such as pipes and fittings, undergo hydrostatic or pneumatic pressure tests to ensure they can withstand the specified pressures without failure.
7. Surface Finish Inspection:
Surface finish inspection assesses the quality and smoothness of the casting’s surface. It ensures that the casting meets the required surface roughness and finish specifications.
8. Ultrasonic Thickness Measurement:
This method measures the thickness of the casting’s walls using ultrasonic waves. It helps verify uniform wall thickness and detect thinning areas that could compromise the casting’s integrity.
9. Hardness Testing:
Hardness testing measures the hardness of the casting’s material using methods like Brinell, Rockwell, or Vickers testing. This helps assess the material’s strength and resistance to wear.
Effective quality control ensures that ductile iron castings meet industry standards, regulatory requirements, and customer specifications. By employing a combination of these methods, manufacturers can identify and address defects, anomalies, and deviations from the desired quality, thereby producing reliable and high-quality ductile iron castings.
Chapter 12: Environmental Considerations During the Process of Ductile Iron Castings
Environmental considerations are becoming increasingly important in the casting process of ductile iron castings to promote sustainability and reduce the overall environmental impact. Several practices and strategies can be employed to minimize waste, conserve resources, and promote green manufacturing:
1. Material Recycling:
Implement recycling programs for scrap metal and other materials generated during the casting process. Recycle leftover sprues, gates, and defective castings to reduce waste and conserve raw materials. Recycling can also help reduce energy consumption and greenhouse gas emissions associated with the production of new materials.
2. Energy Efficiency:
Optimize energy usage by adopting energy-efficient technologies and practices. This includes using energy-efficient furnaces, optimizing melting processes, and using advanced insulation materials to minimize heat loss during heating and cooling cycles.
3. Emissions Reduction:
Install air pollution control systems, such as baghouses or scrubbers, to capture and control harmful emissions generated during the melting and casting process. Proper emission control helps reduce the release of pollutants into the atmosphere.
4. Water Conservation:
Implement water-saving measures to reduce water consumption during the casting process. This includes using closed-loop water systems, optimizing cooling processes, and minimizing water usage for cleaning and quenching.
5. Green Sand Reclamation:
Utilize green sand reclamation systems to recycle and regenerate used sand for molding purposes. This reduces the need for new sand and minimizes waste generation. Reclaimed sand can be mixed with new sand to maintain the required properties for molding.
6. Lean Manufacturing:
Implement lean manufacturing principles to optimize processes and eliminate waste. Reduce excess material handling, streamline workflows, and minimize non-value-added activities to enhance overall efficiency and resource utilization.
7. Waste Management:
Develop a comprehensive waste management plan to segregate, recycle, and dispose of waste materials responsibly. Proper waste management prevents pollution and reduces the environmental footprint of the casting process.
8. Lifecycle Assessment:
Conduct a life cycle assessment (LCA) to evaluate the environmental impact of ductile iron casting processes from raw material extraction to end-of-life. Identify areas for improvement and implement measures to reduce environmental impacts at every stage of the product lifecycle.
9. Green Certification and Standards:
Adopt environmentally friendly certifications and standards, such as ISO 14001 for environmental management systems, to ensure that the casting process adheres to sustainable practices.
10. Employee Awareness and Training:
Educate employees about the importance of environmental considerations and provide training on sustainable practices. Encourage a culture of environmental responsibility within the workforce.
By integrating these environmental considerations into the casting process of ductile iron castings, manufacturers can contribute to a more sustainable and environmentally friendly production process, reduce waste generation, and minimize the ecological footprint of their operations.
Chapter 13: Innovative Trends in the Field of Ductile Iron Castings
In the field of ductile iron castings, several innovative trends are shaping the way these castings are produced, improving their quality, efficiency, and sustainability. Some of these trends include:
1. Digital Manufacturing and Industry 4.0:
The adoption of digital manufacturing technologies, such as advanced simulation and modeling software, digital twin technology, and real-time monitoring systems, is transforming the ductile iron casting process. Industry 4.0 principles are being applied to optimize production processes, improve quality control, enhance predictive maintenance, and enable data-driven decision-making.
2. Additive Manufacturing (3D Printing):
Additive manufacturing techniques are being explored for producing complex and intricate ductile iron components. While traditional casting methods remain dominant, 3D printing offers opportunities for rapid prototyping, customized designs, and the production of small batches with reduced lead times.
3. Advanced Materials and Alloys:
Research into new materials and alloy compositions is ongoing to enhance the mechanical properties and performance of ductile iron castings. The development of high-strength and lightweight materials can lead to improved efficiency and durability in applications that require these properties.
4. Sustainable Practices:
Sustainability is a growing concern in the manufacturing industry, and the field of ductile iron castings is no exception. Manufacturers are focusing on reducing energy consumption, minimizing waste, and implementing eco-friendly practices to reduce the environmental impact of the casting process.
5. Automation and Robotics:
Automation and robotics are being integrated into various stages of the ductile iron casting process, including mold preparation, pouring, and finishing. This not only improves consistency and precision but also enhances worker safety and frees up human resources for more complex tasks.
6. Advanced Simulation and Modeling:
Simulation software is increasingly being used to predict and optimize the behavior of molten metal during casting, solidification, and cooling processes. This helps in minimizing defects, optimizing gating systems, and improving casting quality.
7. Surface Treatment and Coatings:
Innovative surface treatment techniques and coatings are being developed to enhance the wear resistance, corrosion resistance, and overall performance of ductile iron castings in different environments.
8. Green Sand Reclamation and Recycling:
Green sand reclamation and recycling systems are gaining importance in the industry as a means to reduce waste, conserve resources, and maintain consistent sand quality for molding.
9. Improved Quality Control Methods:
Advancements in non-destructive testing (NDT) techniques, such as digital radiography, ultrasonic testing, and laser scanning, are being used to ensure the quality and integrity of ductile iron castings.
10. Hybrid Casting Methods:
Hybrid approaches that combine different casting methods, such as ductile iron casting with other processes like investment casting or additive manufacturing, are being explored to leverage the strengths of each technique for specific applications.
These trends are collectively driving innovation in the field of ductile iron castings, making the process more efficient, sustainable, and capable of producing high-quality components that meet the demands of various industries.