The shell of the motor has complex appearance, including outlet box, fork hole, pitch converter mounting screw hole, rotor mounting base, and an internal circulating water chamber. In order to obtain an inner cavity by casting, a sand core (hereinafter referred to as water jacket core) with the same shape as the water cavity is required. The sand core does not react with the molten iron, and the water cavity shape can be obtained by collapsing the molten iron after cooling. The original three-dimensional water jacket smart model can be easily obtained by using the synchronous modeling of UG and Boolean operation function,
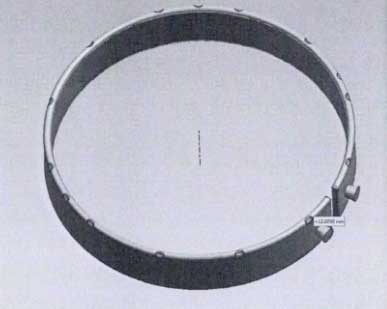
The wall thickness of the water jacket core is only 12mm without shrinkage and coating layer. The wall thickness will be thinner after putting various process parameters, and the whole sand core is not connected. There are only two supports, i.e. inlet and outlet, on the periphery. It is difficult to carry the self hardening resin sand completely after the production of the sand core, and the closed inner cavity can not clean the casting after Shao casting, There are two problems caused by residual sand in the water chamber:
(1) The residual sand is carried to the water by cooling water flow, and the damaged water is accumulated.
(2) The residual sand affects the cooling effect and overload the motor at high temperature.
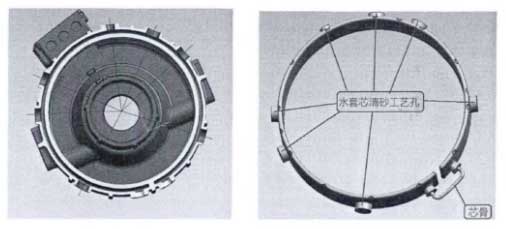
Therefore, it is necessary to solve the molding process of the water jacket core. Considering that the product needs an inner cavity of 12mm, with a distance of 90mm, it is difficult to carry the core by itself depending on the strength of self hardening sand, and the casting also needs to be cleaned after casting. Therefore, it can be considered to add some process holes around the product, and then use the frozen bowl plug after the product is processed, which is a more commonly used process in the transmission industry. The process hole can be used to clean the sand in the inner cavity from the hole easily after the casting is cooled. At the same time, because the water jacket core is disconnected at the inlet and outlet holes, the overall strength is very low. In order to increase the strength, it can be considered to arrange the core bone at the water hole to increase the overall strength. After confirming that the installation position will not interfere, 6 process holes with diameter of 38 and 1 process hole with diameter of 21 are added around the product, and a core bone with diameter of 10 is added at the inlet and outlet holes.
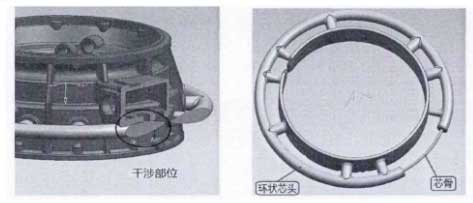
Although the problem of sand cleaning in the inner cavity of the motor shell has been solved, and the core bone has also been added to the disconnected part of the sand core, because the sand core is too thin, it can only be arranged in the water inlet and outlet holes. If the water jacket core is regarded as an approximate revolving body, the core bone can only resist the radial force to a certain extent, but cannot prevent the axial force from pulling the sand core. Therefore, to better protect the water The position of core and core bone need to be changed. In order to strengthen the strength of the water jacket core without replacing the molding sand, it is necessary to solve the problem that there is a gap in the annular sand. A complete ring can greatly improve the overall strength of the sand core, so it is not necessary to crack in the process of handling. Therefore, it can be considered to add a complete annular core head, annular core head and inner core at the outer side of the water jacket core in combination with the sand cleaning hole added above In this way, the inner core is connected with the annular core head by 9 supporting columns, and the situation that the gap of the inner core causes the sand core to be sheared and cracked is also improved under the effect of the supporting column. Because the annular core head and the inner core form the water jacket core together, the core needs to be made together. In order to save sand and reduce the weight of sand, the diameter of the annular core head should be the same as the diameter of the process hole. However, because the motor housing has an outlet box, the shape of the 038 part of the ring core is interfered with the outlet box. In order to avoid the outlet box, the diameter of a nearby core can be reduced. However, because of the need to avoid the enough location of the outlet box, W will form foam and sand core. The diameter of a section of sand core near the outlet box can only be about 10, and the size of the sand core will become the whole. At the weakest part of the annular core head, the sand core is easy to crack when it is transported. However, the size of the reinforcement with a diameter of 10 can meet the requirements of the whole water jacket core for rigidity and tensile strength. Therefore, the problem of yielding can be solved by arranging a section of core bone near the occurrence box.