1. Selection of runner
The overall structure of the fixed disk investment casting is irregular, with a through hole with a diameter of 15 mm on the side. The average wall thickness of the entire investment casting is 7 mm, and it mainly consists of a base, a curved surface, and holes. In order to make the filling process of investment castings relatively stable and the investment castings can solidify in sequence, it is required that the gating system be well fed to reduce the generation of shrinkage porosity and shrinkage cavities. According to production requirements, use a vertical sprue, a horizontal sprue, and an internal sprue.
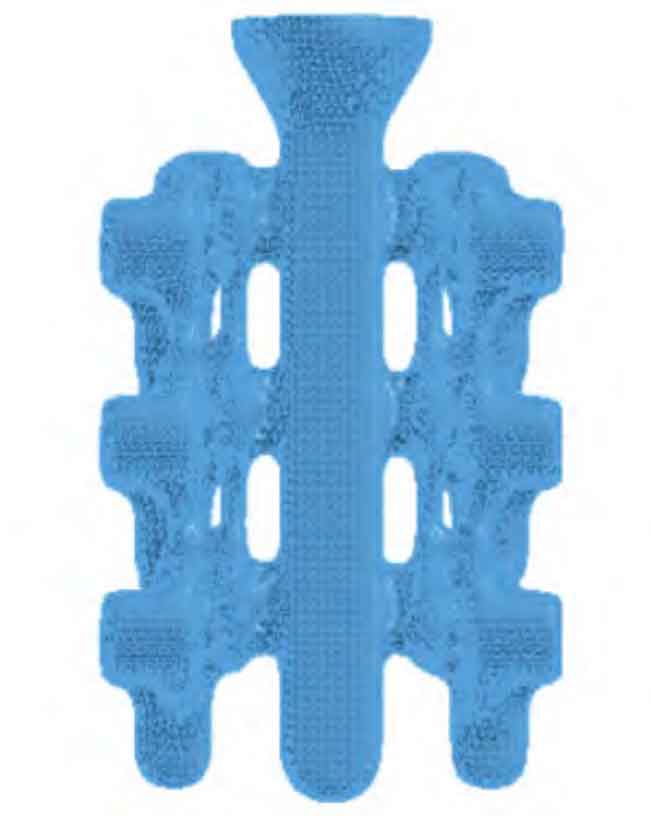
2. Establishment of pouring model
Based on the three-dimensional model of a fixed disk investment casting, a three-dimensional model of its gating system is established, and then the gating system is automatically meshed to obtain a three-dimensional digital model of the gating system of the fixed disk investment casting, as shown in the figure. The grid value is taken as 5mm, the total number of grid cells is 56352, and the total number of nodes is 435310.
3. Simulation related parameter settings
Accurate results can only be obtained by accurately setting simulation parameters in ProCAST software. When simulating investment casting, many simulation parameters are involved, such as heat transfer coefficient, boundary conditions (pouring speed, heat, temperature, etc.), initial conditions (shell, casting, air, etc.), and material parameters. The simulation parameters are set as follows: the ambient temperature during pouring is 800 ℃, and the mold shell temperature does not change, and the mold shell thickness is about 6mm. The material is 42CrMo4 steel, and the corresponding pouring temperature is 1550~1580 ℃, which is 1580 ℃. The gravitational acceleration is set to 9.8m/s2, the heat transfer coefficient is set to 500W/(m ^ 2 · K), and the cold and heat exchange coefficient between investment castings and air is set to 1000W/(m ^ 2 · K).