According to the definition of composite squeeze casting, the process flow of the composite squeeze casting forming method is as follows:
(1) The molten metal is transferred to the holding furnace in advance, as shown in figure a);
(2) Upper mold and lower mold are pre assembled, as shown in Figure b);
(3) The molten metal is introduced into the mold filling cavity through a closed pipe, as shown in Figure c);
(4) The metal melt is sent into the mold cavity by the mold filling head to complete the mold filling, as shown in Figure d);
(5) The molten metal is extruded from the upper die downward, and the molten metal solidifies under pressure, as shown in Figure e);
(6) Open the mold and take out the casting, and the mold filling head descends back to the initial position, as shown in Figure f).
In this forming process, pre closing means that the mold forms a closed mold filling space, which is closed relative to the extruded alloy body in the mold cavity, and the gas and a small amount of slag collection and exhaust overflow are throttled and connected to the outside.
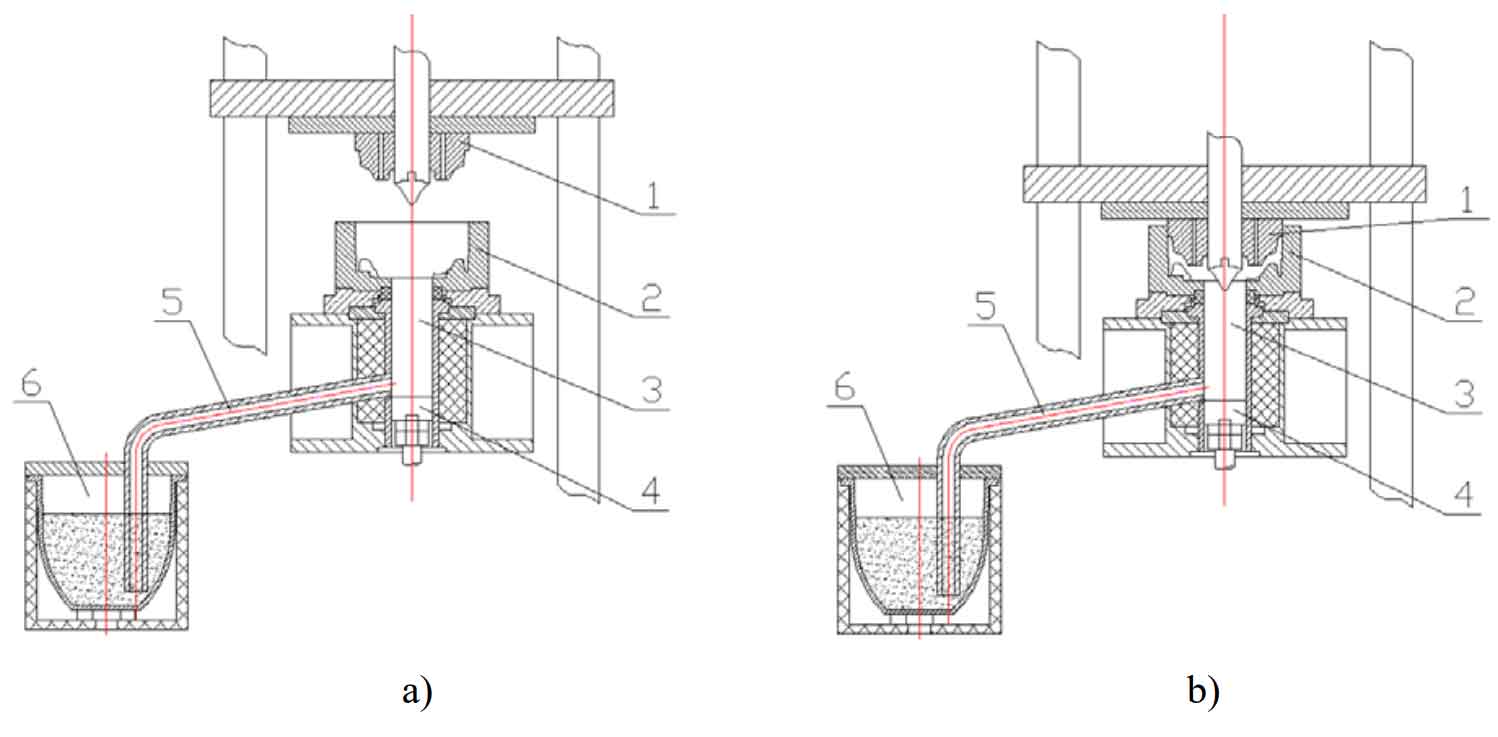
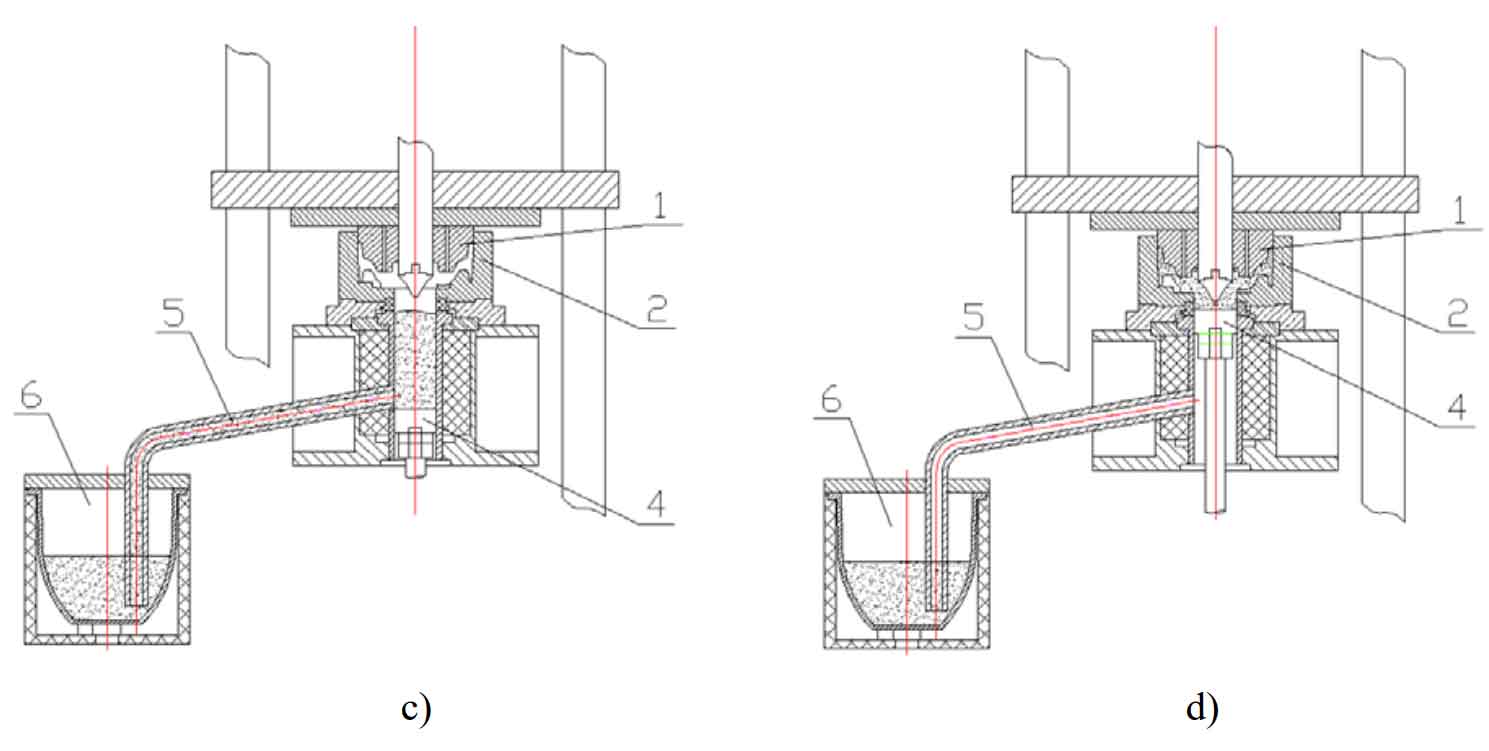
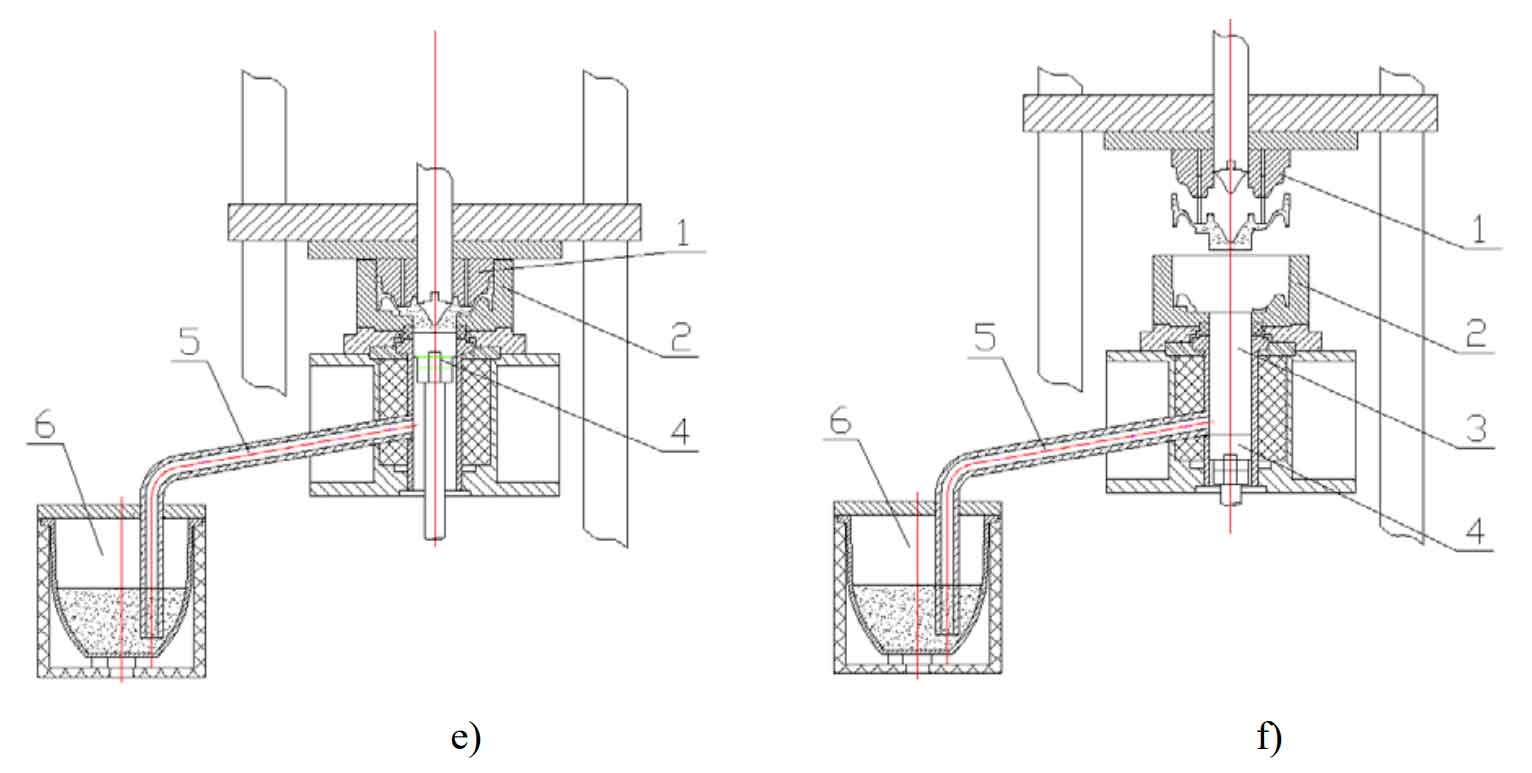
This method uses closed pipes to transport molten metal, which reduces the adverse factors such as oxidation and suction of molten metal. At the same time, the pressure of the die fully acts on the molten metal. It has the advantages of short extrusion force transmission distance, fast pressure building speed, less pressure loss and high utilization efficiency, and is conducive to the squeeze casting of large and complex parts.