Due to the temperature gradient generated in the process of laser melting of gray cast iron and the transformation of surface microstructure after melting of gray cast iron, there is a large residual tensile stress in the melting layer of gray cast iron. Once the value of the tensile stress exceeds the yield strength of the material, it will lead to cracks in the melting layer of gray cast iron. Figure 1 (a) shows the residual stress value of the surface of gray cast iron melting layer measured by X-ray stress tester along the laser scanning direction. The analysis shows that the residual stress on the surface of gray cast iron melting layer is mainly tensile stress. When the scanning speed is 4 mm / s and the laser power is 1000 W, the average residual tensile stress on the sample surface after gray cast iron melting is 190 MPa, the laser power is 1500 W and the average residual tensile stress is 250 MPa. When the laser power is 2000 W, the average residual tensile stress reaches the highest 275 MPa. With the increase of laser power, the residual tensile stress increases significantly. Fig. 1 (b) shows the change of residual compressive stress on the surface of gray cast iron melting layer under different laser impact energy. After laser impact, the residual tensile stress on the surface of gray cast iron melting layer is completely transformed into residual compressive stress. When the laser impact energy is 3 J, the residual compressive stress induced by gray cast iron melting surface is small, and the maximum residual compressive stress reaches – 100 MPa in the center of the molten pool, When the laser shock energy increases to 5 J and 7 J, the maximum residual compressive stress on the surface increases to – 250 MPa and – 300 MPa respectively. This shows that the residual compressive stress increases significantly with the increase of laser shock energy. Under the laser impact with the overlap ratio of light spot of 50%, the value of residual compressive stress in the middle of gray cast iron melting layer fluctuates less, and the distribution of residual compressive stress is more uniform.
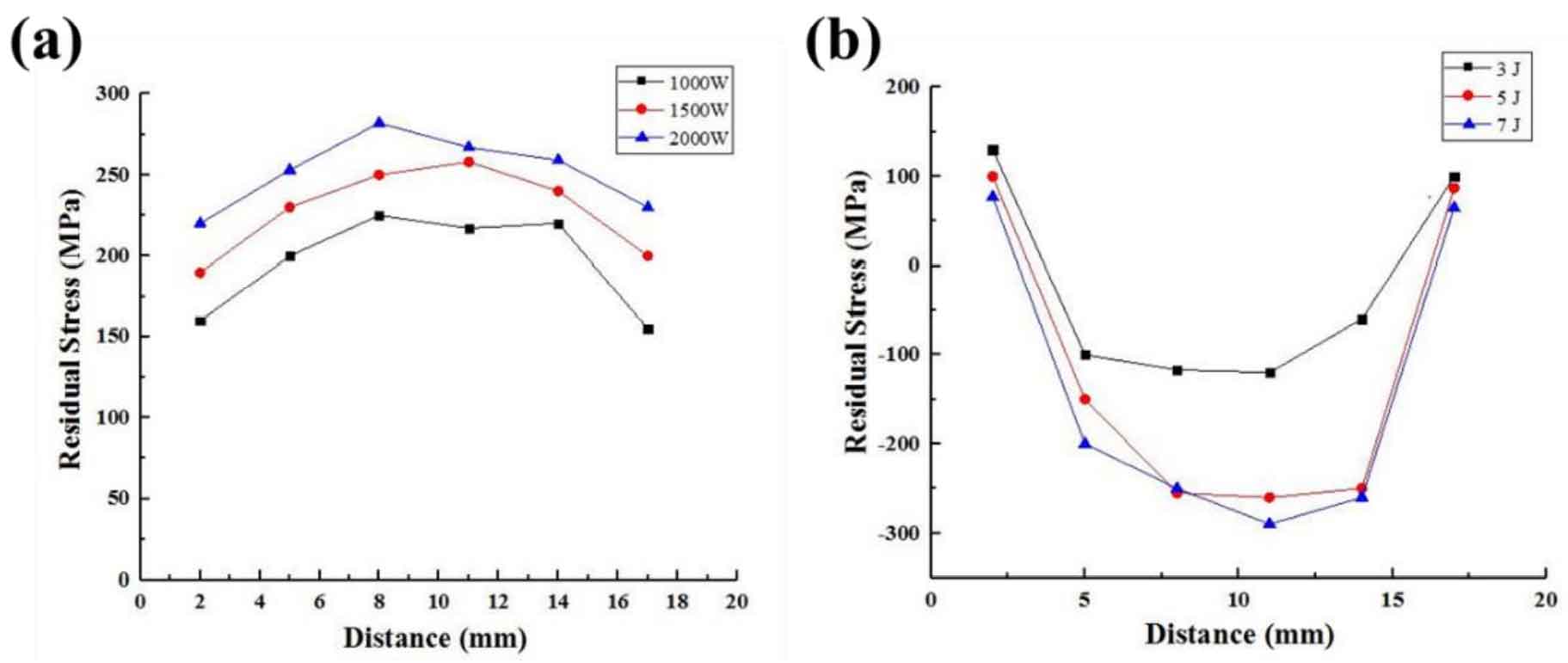
(b) Residual compressive stress on the remelted surface after LSP
Figure 2 shows the comparison of crack propagation depth of gray cast iron melting layer before and after laser impact. It can be seen from the cross section of the gray cast iron laser melting sample that the crack originates on the surface of the gray cast iron melting layer. Because the carbide toughness on the surface of the gray cast iron melting layer is very poor, the crack will expand into the melting layer along the hard and brittle columnar cementite and cause damage to the melting layer. After laser shock, the size of the crack in the fusion layer of gray cast iron is reduced by half, and the depth of crack propagation into the fusion layer is also significantly reduced. The analysis shows that the residual compressive stress induced by laser shock improves the tensile stress in the fusion layer of gray cast iron and can hinder the crack propagation. After laser shock, the grain of the fusion layer is refined and the grain boundary is increased, It leads to the increase of the yield strength of the melting layer of gray cast iron and inhibits the crack initiation.