1. Introduction
In the field of casting, the production of high-quality castings is crucial for various industries. The box bed casting is an important component, especially in the manufacturing of large machine tools. However, during the production process, numerous challenges and quality issues often arise. This article focuses on a specific box bed casting produced by a company and details the process of identifying and resolving the problems to achieve an improved casting process.
1.1 Background of the Box Bed Casting
The box bed casting serves as a vital part of large machine tools. It not only bears the load of other components but also forms the core skeleton of the machine tool. Its quality directly impacts the precision, performance, and service life of the machine tool. For example, in a machining center, an accurate and durable box bed casting is essential for maintaining the stability and accuracy of the cutting operations.
1.2 Importance of Process Improvement
The initial production of the box bed casting faced several quality problems, such as slag inclusion, choking bubbles, and poor core brace fusion on the upper box surface. These issues led to a high defective rate, which not only increased production costs but also affected product delivery and customer satisfaction. Therefore, process improvement was necessary to enhance the quality of the castings and ensure the smooth operation of the production line.
2. Structure and Quality Requirements of the Box Bed Casting
2.1 Casting Structure
The box bed casting has a specific structure as shown in Figure 1. It has a material of HT300 and a weight of 2989 kg. The contour dimensions are 3100 mm × 1265 mm × 785 mm. The main wall thickness is 15 mm, with a maximum wall thickness of 90 mm and a minimum wall thickness of 15 mm.
2.2 Quality Requirements
- The processing surface should be free from defects such as sand inclusion, pores, slag inclusion, and cold shuts.
- The oil cavity area should have no defects.
- The hardness of the guide rail must be greater than 183 HBN, and there should be no issues such as loose structure and unqualified hardness.
- The other appearance surfaces should not have obvious defects like sand holes, sand sticking, and bulges that affect the appearance quality.
3. Original Process and Casting Quality Problems
3.1 Original Process
- Melting Parameters
- The raw material proportions are as follows:
| Raw Material Type | Pig Iron | Machine Iron | Scrap Steel | Carburizer | Ferrosilicon | Ferromanganese |
| — | — | — | — | — | — | — |
| Proportion | 5% | 35% | 60% | 2.0% | 0.7% | 0.4% | - The original iron water composition requirements are as follows:
| Chemical Composition | C | Si | Mn | P | S | Ti | Pb |
| — | — | — | — | — | — | — | — |
| Proportion | 3.12±0.03 | 1.40±0.03 | 0.65±0.03 | ≤0.04 | 0.08 – 0.12 | ≤0.030 | ≤0.0015 | - The iron water melting temperature is not higher than 1380 °C, the superheat temperature is 1490 – 1510 °C, and the pouring temperature is controlled between 1370 – 1390 °C. A 0.5% SiFe (particle size 3 – 10 mm) is used for inoculation treatment in a two-stage inoculation tank, and 0.1% SiFe (particle size 3 – 10 mm) is added in the ladle for floating silicon inoculation to control the Si content of the casting between 1.7% – 1.8% and the C content between 3.05% – 3.15%.
- The raw material proportions are as follows:
- Pouring System
- An open, bottom-return type pouring system is adopted. The inner runner is introduced from the bottom surface. The pouring system ratio is: Σ直:Σ横:Σ内 = 1:1.56:1.53. The straight runner is ø90 mm, the cross runner is (105 mm + 84 mm) × 105mm, and the inner runner is ø35 mm × 4/ø50 mm × 3 (ø35 cross-sectional area 3848 , ø50 cross-sectional area 5890 ). The process uses 8 S100 mm and 2 S80 mm spherical risers and no cold iron is placed.
3.2 Casting Quality Problems
- Hardness Issue
- Out of 13 castings produced, 4 had a hardness of 164 – 176 HBN, which was lower than the customer’s requirement. The metallographic examination revealed that the pearlite content was only 80% – 90%. The hardness of other qualified products was concentrated between 180 – 185 HBN, indicating a certain risk.
- Slag Inclusion on the Upper Box Surface
- The upper box surface had a significant amount of slag inclusion. Almost every casting required welding repair, increasing the difficulty of subsequent cleaning and the cost of rework.
- Choking and Defects during Pouring
- During the pouring process, choking was severe. 7 castings were scrapped due to choking, resulting in a scrap rate of 53.8%. The choked castings showed defects such as poor core brace fusion, and the PT test was unqualified after welding repair.
3.3 Reasons for Quality Problems
- Material and Pouring System Related to Hardness Issue
- Due to the large wall thickness deviation of the casting material HT300 and the slow pouring speed and relatively low pouring temperature in an open pouring system, defects such as cold shuts, loose structure, and unqualified hardness occurred. The insufficient pearlite content was likely due to the insufficient content of chemical elements promoting pearlite formation, and the high CE value also promoted the formation of ferrite.
- Reasons for Slag Inclusion on the Upper Box Surface
- The upper box surface was mostly flat, with a small core-setting gap. The control of the sand core coating layer was poor, resulting in sand rubbing during the core-setting process. Moreover, there were few overflow risers on the upper box surface, leading to slag inclusion after pouring. Additionally, due to the special structure of the casting, the weight reduction holes and wire-passing holes on the upper box surface were concentrated at one end, and there were almost no weight reduction holes on one side of the fuel tank. In actual production, many core braces were used, and sand rubbing occurred during core-setting. The uncleaned scattered sand led to slag inclusion in the casting.
- Causes of Choking and Core Brace Fusion Problems
- The choking problem was more likely to occur at the 10# and 11# core positions. The lower side of the 10# and 11# cores had core heads for fixation, while the upper side was completely supported by core braces with a large contact area and could not be effectively fixed. Under the impact of the molten iron, these two sand cores were prone to shaking, resulting in choking. The poor fusion of core braces after using ordinary core braces was due to the inability to effectively guarantee the pouring temperature during pouring, resulting in the defect of poor core brace fusion.
4. Process Improvement Measures
4.1 Melting Process Improvement
- The proportion of scrap steel was appropriately increased during iron water melting to improve the hardness of the casting.
- To ensure the pearlite content, the control median of Mn was increased from 0.65% to 0.95%, the control median of C was decreased from 3.12% to 3.07%, and the control median of Si was decreased from 1.75% to 1.71%.
- The pouring temperature was adjusted to 1380 – 1400 °C, while other melting parameters remained unchanged.
4.2 Casting Process Improvement
- 3D Printing Standard Core Method
- Due to the special structure of the casting, the original 3D process had problems with ineffective fixation of some sand cores during core-setting. To solve this, the product was directly modified to be produced using the 3D printing standard core method. The sand cores were produced in a “standard core” manner. For example, the core head parts of the 8# and 11# sand cores that were difficult to fix were designed as embedded screw methods. Before core-setting, the 6# core was connected and fixed to the 10# sand core through a screw. Two ø20 mm and 650 mm long poles were pre-embedded on the 7# sand core, and the 11# core was fixed through the screw of the 7# sand core. This reduced the use of core braces.
- Adjustment of Core Gaps and Increase of Overflow Risers
- The gaps between the remaining sand cores were adjusted from 1 mm to 1.5 mm. The number of overflow risers on the upper box surface was increased from 10 to 16, with an increased gas outlet area of 5850 .
5. Improvement Results
- After implementing the improved process, 40 products were continuously produced. The pearlite content in the casting matrix structure was ≥95%, the tensile strength was 315 – 335 MPa, and the solid hardness reached 183 – 192 HBN, meeting the customer’s quality requirements for materials.
- The pouring process was stable, and no choking phenomenon occurred at a pouring temperature of 1380 – 1400 °C. The casting did not have defects such as slag inclusion, sand inclusion, and poor core brace fusion. The defective rate was controlled below 1.5%.
6. Conclusion
The production of box bed castings has its own unique characteristics. Through continuous exploration and improvement, a set of production processes for thin-walled box castings in the fuel tank area has been developed and applied in production practice. The key points include not using core braces in the fuel tank area, placing the entire casting in the upper box, placing a filter net under the cross runner, strictly controlling the contents of Mn, C, and Si to ensure the pearlite content, and ensuring a pouring temperature above 1380 °C and waiting for 72 hours before lifting and unpacking the casting. This process improvement has effectively solved the quality problems of the box bed casting, improved the product quality and production efficiency, and reduced the production cost and defective rate, providing a valuable reference for the production of similar castings in the future.
In the following sections, we will further discuss the details of each aspect of the process improvement and its impact on the casting quality.
6.1 Impact of Melting Process Improvement on Casting Quality
The adjustment of the raw material proportions and the control of chemical compositions in the melting process have a significant impact on the casting quality. By increasing the proportion of scrap steel, the hardness of the casting can be improved. The adjustment of the control values of Mn, C, and Si ensures the proper formation of the microstructure of the casting. The increase in Mn content promotes the formation of pearlite, while the appropriate reduction of C and Si contents helps to control the microstructure and hardness of the casting. The adjustment of the pouring temperature also plays a crucial role. A higher pouring temperature within a reasonable range can ensure the fluidity of the molten iron, reducing the occurrence of defects such as cold shuts and improving the filling ability of the mold cavity.
6.2 Significance of Casting Process Improvement
The adoption of the 3D printing standard core method has revolutionized the casting process. It not only solves the problem of ineffective fixation of sand cores but also reduces the use of core braces, thereby reducing the potential for defects such as core brace fusion problems. The adjustment of the core gaps and the increase of overflow risers on the upper box surface also contribute to improving the quality of the casting. The appropriate core gaps ensure the smooth flow of gases during the casting process, reducing the occurrence of defects such as pores and slag inclusion. The increase in overflow risers provides a better exhaust path for the gases generated during the pouring process, further improving the quality of the casting.
6.3 Comparison of Original and Improved Processes
Aspect | Original Process | Improved Process |
---|---|---|
Melting Parameters | Pig Iron: 5%, Machine Iron: 35%, Scrap Steel: 60%, Carburizer: 2.0%, Ferrosilicon: 0.7%, Ferromanganese: 0.4%; Iron water melting temperature ≤ 1380 °C, superheat temperature 1490 – 1510 °C, pouring temperature 1370 – 390 °C; Si content 1.7% – 1.8%, C content 3.05% – 3.15% | Pig Iron: 5%, Machine Iron: 35%, Scrap Steel: increased, Carburizer: 2.0%, Ferrosilicon: 0.7%, Ferromanganese: increased; Iron water melting temperature ≤ 1380 °C, superheat temperature 1490 – 1510 °C, pouring temperature 1380 – 1400 °C; Si content 1.71% – 1.8%, C content 3.07% – 3.15% |
Pouring System | Open, bottom-return type; Σ直:Σ横:Σ内 = 1:1.56:1.53; Straight runner ø90 mm, cross runner (105 mm + 84 mm) × 105mm, inner runner ø35 mm × 4/ø50 mm × 3; 8 S100 mm and 2 S80 mm spherical risers, no cold iron | 3D printing standard core method; Gaps between cores adjusted; 16 overflow risers on upper box surface; Different core fixation methods for some cores |
Casting Quality | Hardness issue (some products below requirement), slag inclusion on upper box surface, choking and core brace fusion problems, high defective rate | Pearlite content ≥95%, tensile strength 315 – 335 MPa, solid hardness 183 – 192 HBN, stable pouring process, low defective rate |
This comparison clearly shows the superiority of the improved process over the original one. The improved process effectively addresses the quality problems faced in the original process and significantly improves the quality of the casting.
6.4 Future Prospects for Box Bed Casting Production
The success of this process improvement provides a good example for the future production of box bed castings. In the future, with the continuous development of technology, more advanced casting methods and materials may be applied. For example, the development of new alloy materials may further improve the performance of the box bed casting. The application of more advanced numerical simulation techniques can help to optimize the casting process in advance, reducing the trial and error process. Additionally, the integration of intelligent manufacturing technologies can improve the production efficiency and quality control of the casting process. However, it is also necessary to continuously monitor and evaluate the production process to ensure that the quality of the castings remains stable and meets the requirements of different applications.
In conclusion, the process improvement of the box bed casting is an important step in the development of the casting industry. It not only solves the immediate quality problems but also provides a direction for future development. Through continuous innovation and improvement, the production of box bed castings can achieve higher quality and efficiency, meeting the needs of the modern manufacturing industry.
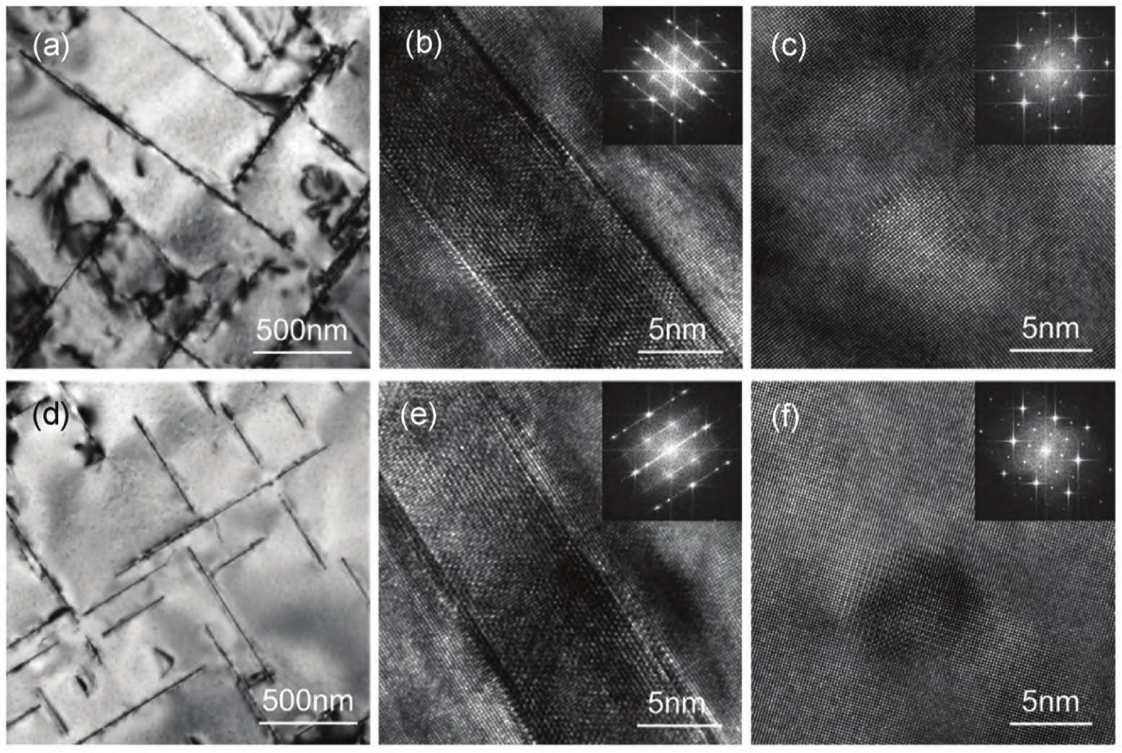