The metallurgical industry relies heavily on various types of cast irons due to their versatile properties and cost-effective production methods. Among these, ductile cast iron stands out for its superior mechanical properties compared to traditional cast irons. This article presents a comparative analysis of ductile cast iron and traditional cast irons, focusing on their microstructure, mechanical properties, applications, and advantages in the metallurgical industry.
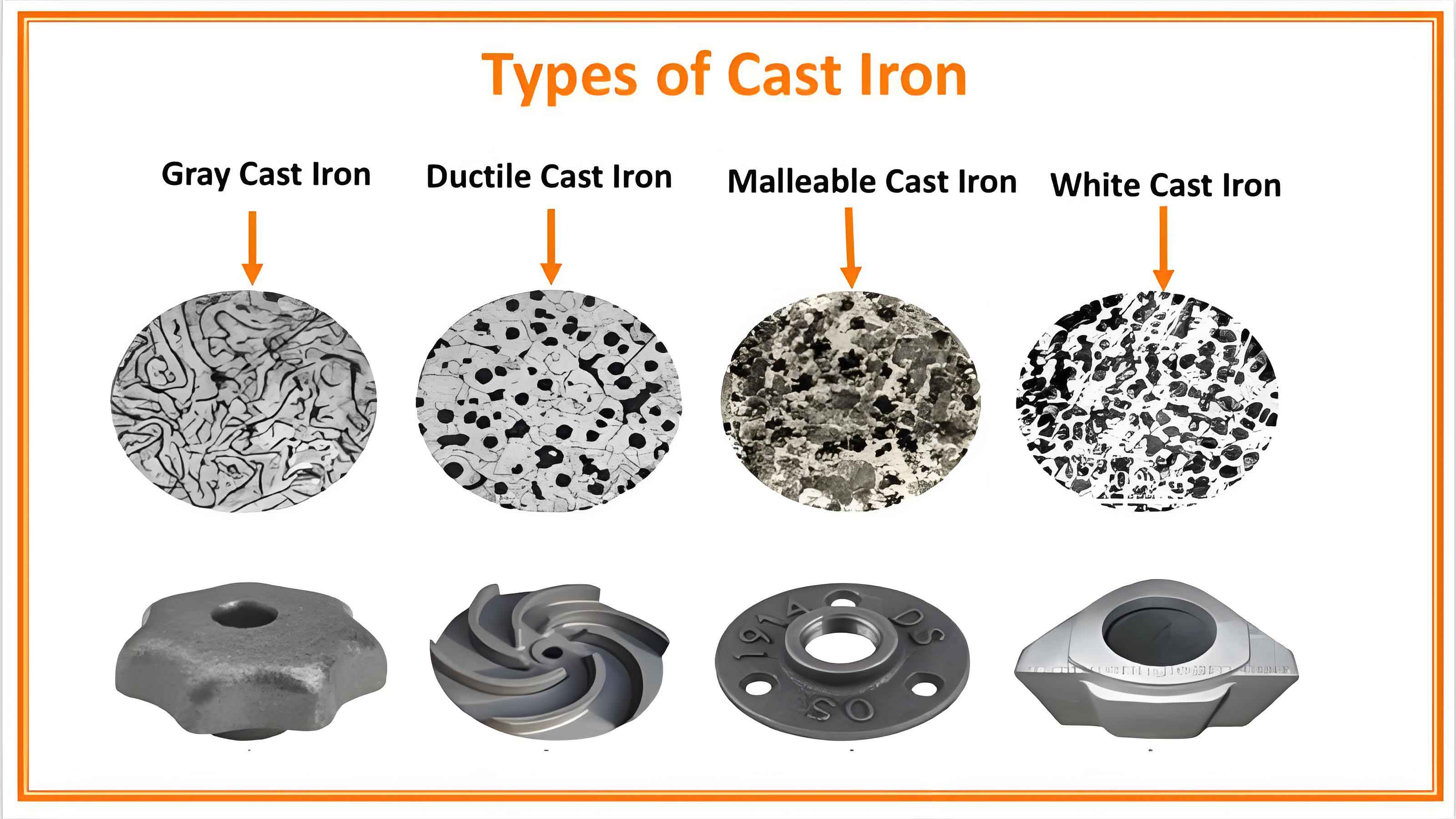
Introduction
Cast irons are a group of iron-carbon alloys with carbon content greater than 2%. Traditional cast irons, such as gray cast iron and white cast iron, have been used for centuries due to their excellent castability and machinability. Ductile cast iron, also known as nodular cast iron or spheroidal graphite iron, emerged in the mid-20th century, offering enhanced mechanical properties. This article explores the differences between ductile cast iron and traditional cast irons, highlighting their respective roles in the metallurgical industry.
Microstructure
The microstructure of cast irons significantly influences their mechanical properties. Traditional cast irons and ductile cast iron differ primarily in the morphology of their graphite content.
Gray Cast Iron
Gray cast iron contains graphite in the form of flakes, which are randomly oriented in the matrix. These flakes create stress concentration points, leading to reduced tensile strength and ductility.
White Cast Iron
White cast iron lacks graphite; instead, carbon is present as iron carbide (cementite). This results in a hard and brittle structure, making it suitable for wear-resistant applications but challenging to machine.
Ductile Cast Iron
Ductile cast iron contains graphite in the form of nodules or spheroids. This nodular graphite morphology minimizes stress concentration points, enhancing tensile strength, ductility, and impact resistance.
Table 1: Microstructural Characteristics of Cast Irons
Type of Cast Iron | Graphite Morphology | Matrix Structure |
---|---|---|
Gray Cast Iron | Flake Graphite | Ferrite and/or Pearlite |
White Cast Iron | None (Iron Carbide) | Hard and Brittle (Cementite) |
Ductile Cast Iron | Nodular Graphite | Ferrite, Pearlite, or Bainite |
Mechanical Properties
The mechanical properties of cast irons are crucial for their performance in various applications. Ductile cast iron generally outperforms traditional cast irons in terms of strength and ductility.
Table 2: Mechanical Properties of Cast Irons
Property | Gray Cast Iron | White Cast Iron | Ductile Cast Iron |
---|---|---|---|
Tensile Strength (MPa) | 200 – 400 | 240 – 400 | 400 – 700 |
Yield Strength (MPa) | 100 – 250 | 200 – 300 | 250 – 500 |
Elongation (%) | 0.5 – 2.0 | <0.5 | 5 – 25 |
Hardness (HB) | 180 – 260 | 400 – 600 | 140 – 300 |
Impact Toughness (J) | 5 – 10 | 2 – 5 | 12 – 20 |
Applications
The distinct properties of each type of cast iron determine their suitability for various applications in the metallurgical industry.
Gray Cast Iron
Gray cast iron is widely used for its excellent castability and machinability. Common applications include engine blocks, cylinder heads, machine tool bases, and pipes.
White Cast Iron
White cast iron’s hardness and wear resistance make it ideal for applications such as grinding balls, mill liners, and wear-resistant surfaces.
Ductile Cast Iron
Ductile cast iron’s superior mechanical properties make it suitable for a broad range of applications, including automotive components (e.g., crankshafts, gears), heavy machinery parts, pressure pipes, and structural components in buildings and bridges.
Table 3: Common Applications of Cast Irons
Type of Cast Iron | Common Applications |
---|---|
Gray Cast Iron | Engine blocks, machine tool bases, pipes |
White Cast Iron | Grinding balls, mill liners, wear-resistant surfaces |
Ductile Cast Iron | Crankshafts, gears, pressure pipes, structural components |
Advantages in the Metallurgical Industry
Gray Cast Iron
- Cost-Effective: Lower production costs due to simpler casting processes.
- Excellent Castability: Easy to cast into complex shapes.
- Good Machinability: Easily machined due to the presence of graphite flakes.
White Cast Iron
- High Hardness: Excellent wear resistance for abrasive environments.
- High Strength: Suitable for high-stress applications.
Ductile Cast Iron
- Superior Mechanical Properties: High tensile strength, ductility, and toughness.
- Versatility: Suitable for a wide range of demanding applications.
- Fatigue Resistance: Better performance under cyclic loading conditions.
Comparative Analysis
The comparative analysis highlights the strengths and limitations of each type of cast iron, guiding material selection for specific applications in the metallurgical industry.
Table 4: Comparative Analysis of Cast Irons
Aspect | Gray Cast Iron | White Cast Iron | Ductile Cast Iron |
---|---|---|---|
Castability | Excellent | Moderate | Good |
Machinability | Excellent | Poor | Good |
Wear Resistance | Moderate | Excellent | Good |
Strength and Ductility | Low to Moderate | High strength, low ductility | High |
Toughness | Low | Low | High |
Cost | Low | Moderate | Moderate to High |
Conclusion
The metallurgical industry benefits from the unique properties of various cast irons. Gray cast iron remains a staple for applications requiring good castability and machinability at a low cost. White cast iron excels in wear-resistant applications due to its hardness, despite its brittleness. Ductile cast iron stands out for its superior mechanical properties, making it the material of choice for demanding applications that require high strength, toughness, and ductility.
Understanding the differences between ductile cast iron and traditional cast irons allows engineers and metallurgists to make informed decisions when selecting materials for specific applications, ensuring optimal performance and longevity of the components.