According to the types of base plate defects, corresponding measures are taken in the aspects of gating system, riser, composition control of molten iron, pouring temperature and chilling of plate castings, including increasing riser, changing single side pouring to double side pouring, increasing carbon equivalent, reducing pouring temperature, heel punching point, changing the placement mode of graphite block, etc. By taking the above measures, the internal shrinkage defects of base plate castings can be reduced and eliminated. The improved casting process is shown in Figure 1, and the specific process measures are as follows:
1. Increase carbon equivalent of large ductile iron parts with equal thickness of base plate
The carbon equivalent of molten iron in backing plate casting is increased from eutectic component 4.30% to hypereutectic component 4.55%, and the shrinkage tendency of molten iron is reduced. The molten iron near the eutectic composition has a narrow crystallization temperature range and belongs to layer by layer solidification mode, which is easy to produce concentrated shrinkage. Generally, the defects can be transferred to the riser by designing the riser; Secondly, with low melting point, it is easy to melt. At the same temperature, it has high superheat and good fluidity; In addition, the Fe3C phase is reduced and its fragmentation effect on the collective is reduced.
2. Adjust and control the pouring temperature of molten iron
Under the current process state, the discharge temperature of castings such as backing plate is reduced from 1470 ~ 1480 ℃ to 1450 ~ 1460 ℃, and the gland amount of nodular pig iron is increased from 2.0% to 2.0 ~ 2.5%. The pouring temperature is controlled between 1320 ~ 1340 ℃ by controlling the discharge temperature and spheroidizing agent capping process, which not only meets the pouring temperature requirements of plate castings, but also reduces the shrinkage tendency caused by high pouring temperature.
3. Improvement of gating system
Change the original unilateral pouring into bilateral pouring. Bilateral pouring can reduce the flow resistance of molten iron, shorten the time of molten iron filling the mold cavity, facilitate the filling of large plate castings, and improve the effect of punching point feeding of plate castings.
4. Improve pouring process
The punching point process of the backing plate is improved and changed from the original ladle punching point to another hot metal punching point. Due to the high temperature of the other hot metal, the hot metal remains in a high temperature state for a long time, which prolongs the punching point time. The flushing time is extended from 20 minutes to 30 ~ 40 minutes. Using the feeding principle of riser, the solidification time of riser should be greater than or equal to the solidification time of plate casting (fed part); There shall be enough liquid metal in the riser to supplement the liquid shrinkage and solidification shrinkage of plate castings; During the solidification of plate castings, there should be a smooth feeding channel between the riser and the Fed part. For large plate castings, such as the backing plate of the press, the riser also plays the role of slag removal to realize the sequential solidification of plate castings. Therefore, filling points on the basis of the original riser is more powerful for feeding large plate castings, so as to reduce the tendency of shrinkage cavity of plate castings.
5. Effect verification
After the process improvement, the trial pouring was carried out for several types of press backing plates. In the production of recent year, the qualified rate of finished products of backing plates has been greatly improved, and the scrap rate is zero. It can be seen that after the process improvement, the quality effect on large plate castings is very obvious. At the same time, it is also proved that reasonable composition design, gating system and gating process have a very important impact on the yield of plate castings. Fig. 2 is the drilling drawing of the base plate after the process improvement, and Fig. 3 is the physical drawing of the base plate after the process improvement.
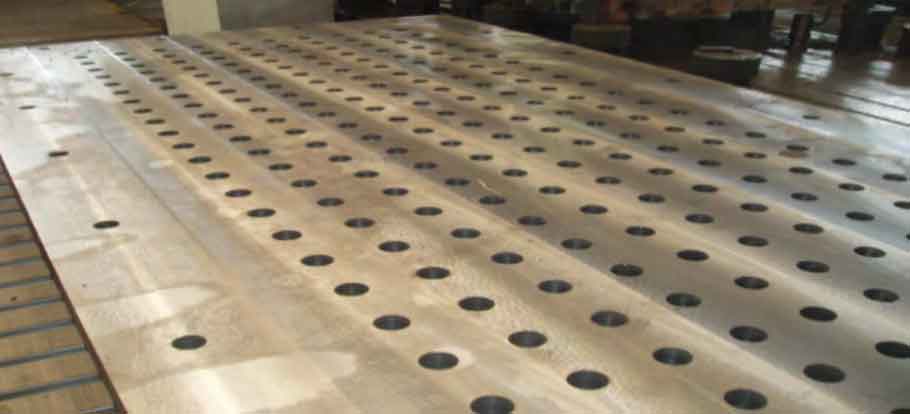
In the casting production of large-scale plate castings, high-quality and dense plate castings can be obtained by adopting reasonable casting process, increasing the carbon equivalent of molten iron, improving the gating system, controlling the pouring temperature of molten iron, reasonably setting feeding risers, effectively feeding the parts prone to defects, improving and controlling the solidification conditions of molten iron, The qualified rate of plate castings is improved, the materials are saved and the production cost is reduced.