The solidification characteristics of heavy section nodular cast iron castings are: short liquid solidification time, long eutectic solidification time, and faster before final solidification. With the increase of the wall thickness of nodular cast iron, the solidification time of eutectic platform increases, and in the later stage of solidification, the solidification time becomes shorter when it is close to the final solidification. The analysis shows that the main way of its decline is the eutectic solidification decline, that is, the cooling rate is slow and the time is long during the eutectic transformation, which leads to the production of abnormal graphite. Therefore, the problems of large diameter and small quantity of graphite balls and fragmented graphite are related to the long solidification time of nodular cast iron. To solve these defects, we should reduce the solidification time of nodular cast iron and improve the anti-aging performance of molten metal.
1. Cold iron application
The solidification time of nodular cast iron in the thick position is relatively long, and the resin sand has a good heat preservation effect, which leads to a further lengthening of the solidification time. Forced cooling measures shall be taken to add cold iron on the upper, lower and side of the thick position, as shown in Figure 1, so as to speed up the cooling of the thick position. Due to the accelerated crystallization rate, the austenitic shell is closed faster, which can prevent the emergence of fragmented graphite. However, for nodular cast iron with large wall thickness, chill can only work in a certain range. When the section is too thick, it still cannot completely eliminate fragmented graphite.
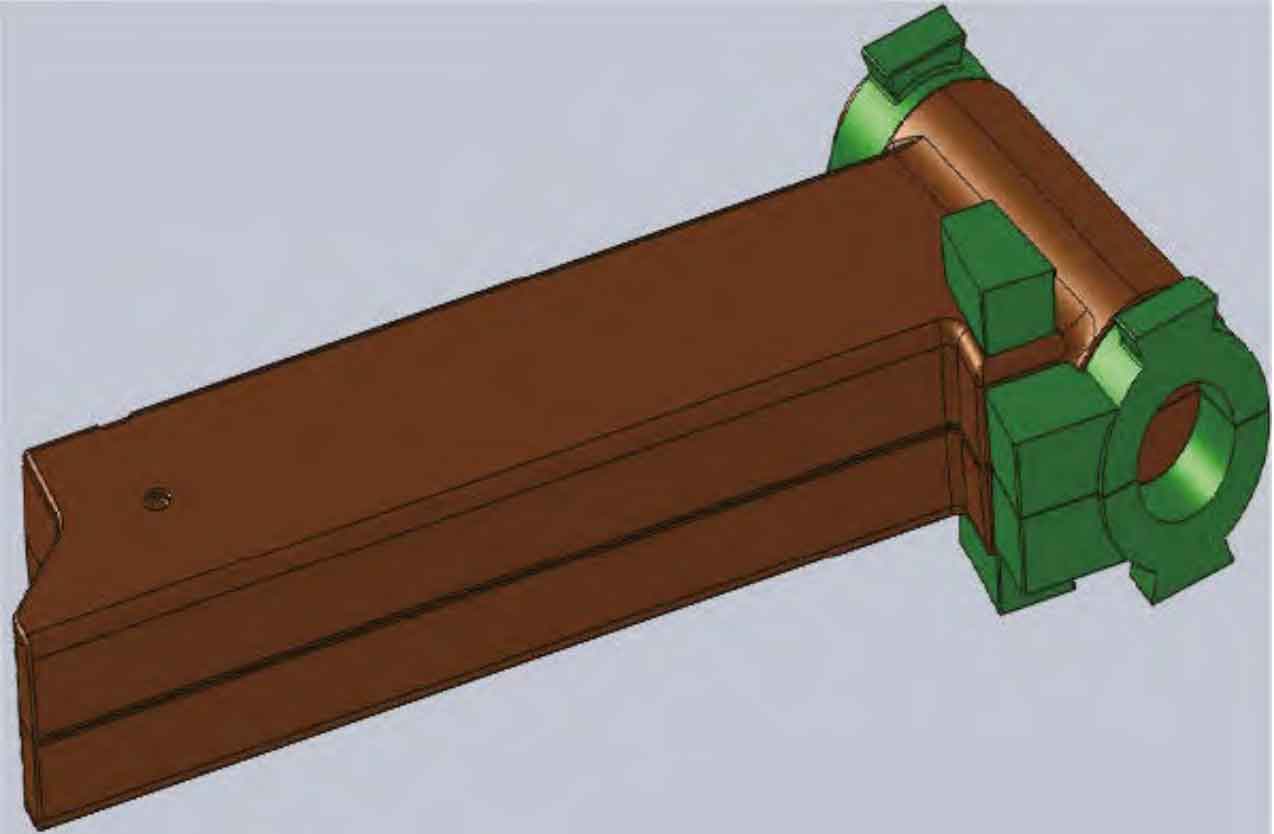
2. Graphite type carburizing agent
The carburizer used in conventional products is petroleum coke. Although it has been calcined at high temperature, its C activity is not enough to meet the requirements of this series of products. Therefore, 0.1%~0.3% graphite type carburizer is added into the furnace before tapping to enhance the graphitization ability of molten iron during treatment, so as to obtain more graphite balls.
3. Low Re nodulizer
Re can remove s and gas, purify molten iron, and give full play to the spheroidization of Mg, playing the role of spheroidization or indirect spheroidization. Re can form high melting point compounds with trace elements, neutralize harmful trace elements, provide a certain heterogeneous core, and increase the number of graphite balls. However, excessive re in heavy section nodular cast iron will lead to the deterioration of graphite morphology and promote the production of fragmented graphite. Re enlarges the eutectic temperature range and prolongs the eutectic solidification time, thereby reducing the number of effective cores for graphite nucleation and increasing the possibility of the existence of fragmented graphite in the residual molten iron. CE and other light RE elements have low melting points and are easy to be segregated between austenite graphite eutectic groups, which stabilizes the narrow channels of eutectic groups, and fragment graphite is easy to be formed in these channels. Therefore, 1.2% – 1.4% pure La low Re spheroidizing agent is selected to improve the graphite morphology of the front axle section and obtain the ideal number of graphite balls.
4. Multiple inoculation
An important reason for the small number of graphite balls and graphite distortion of large section nodular cast iron is the lack of a sufficient number of stable crystalline cores in the long-term solidification process. Some studies have pointed out that when the number of graphite balls of large section nodular cast iron can reach more than 70 / mm2, abnormal graphite will not be formed, that is, with the increase of the number of graphite balls, the graphite morphology can be significantly improved.
Therefore, to solve the problem of less graphite balls and graphite distortion is to precipitate more graphite cores and grow as much as possible at the beginning of solidification and eutectic solidification. Inoculation is an extremely important means. Good inoculation can significantly increase the number of balls and prevent the formation of fragmented graphite, and the later the inoculation time is, the better. In the actual production, the author company adopts three inoculation methods, namely: in bag inoculation + in mold inoculation + flow inoculation, and the amount of inoculant is controlled at 0.6% – 1.0%.
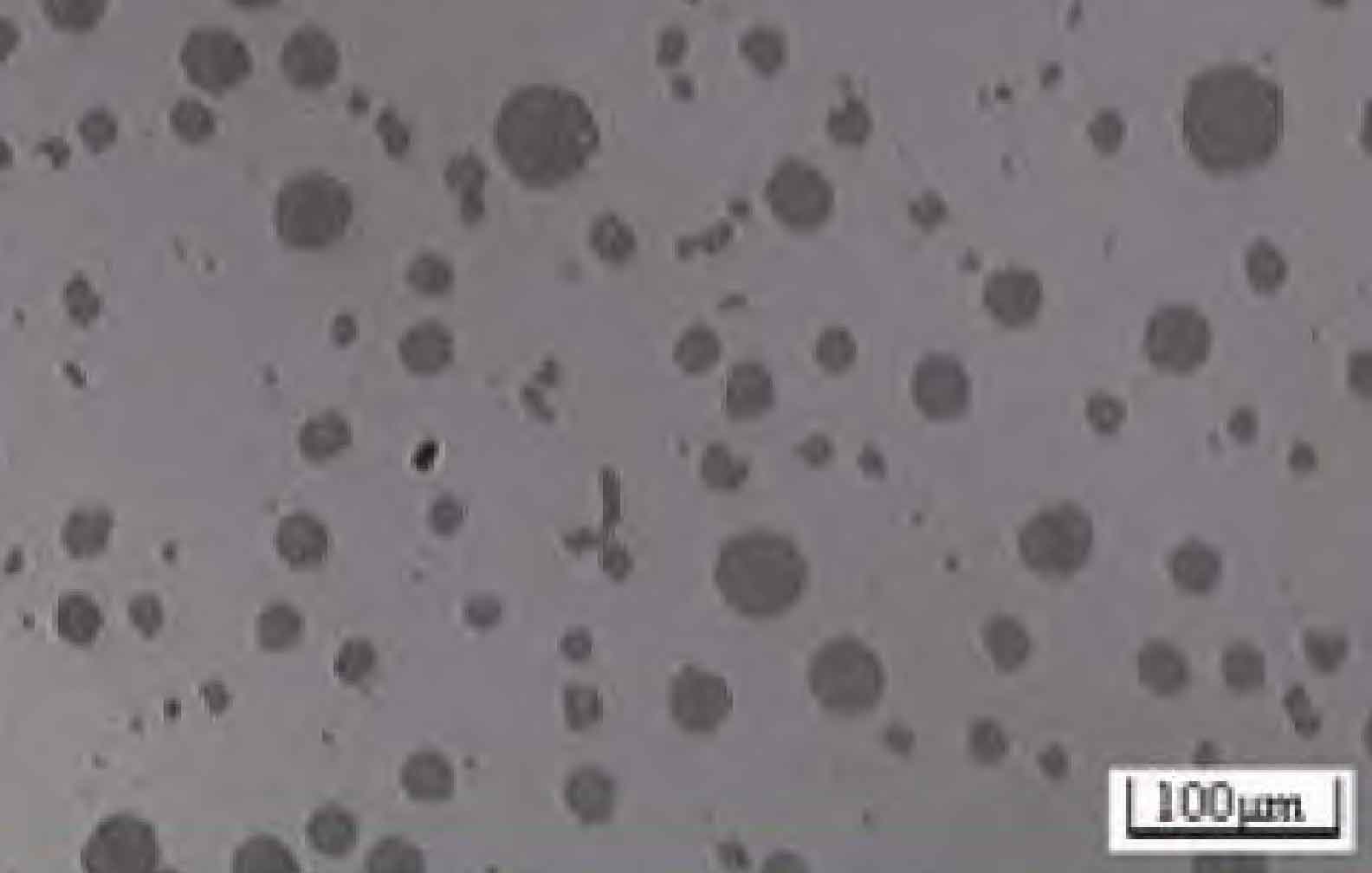
Through the above measures, the graphite balls at the position with large front axle thickness reach 130 /mm2, and the spheroidization rate reaches more than 85%. The metallographic structure is shown in Figure 2. After isothermal quenching, the performance of the sampling position of nodular cast iron reaches 980 MPa, and the elongation is 4.5%.