
Figure 1 shows the relationship between the tensile strength, Brinell hardness and w (TI) content of the test sample, in which the hardness and tensile strength are the average values of the test sample. It can be seen that when the amount of W (TI) of gray cast iron brake disc is 0.01% – 0.12%, the Brinell hardness and tensile strength of brake disc first decrease and then increase with the increase of W (TI). At the same time, it also shows that there is an inflection point between 0.01% and 0.12% for the influence of Ti on the mechanical properties of gray cast iron brake discs, and the specific situation needs further and more detailed experimental research.
Programme | C | Si | Mn | P | S | Cr | Cu | Sn | Ti |
A | 3,31 | 1.95 | 0.80 | 0.03 | 0.08 | 0.25 | 0.29 | 0.05 | 0.01 |
B | 3.30 | 1.98 | 0.79 | 0.03 | 0.08 | 0.25 | 0.29 | 0.05 | 0.03 |
C | 3.32 | 1.99 | 0.76 | 0.03 | 0.07 | 0.26 | 0.28 | 0.05 | 0.12 |
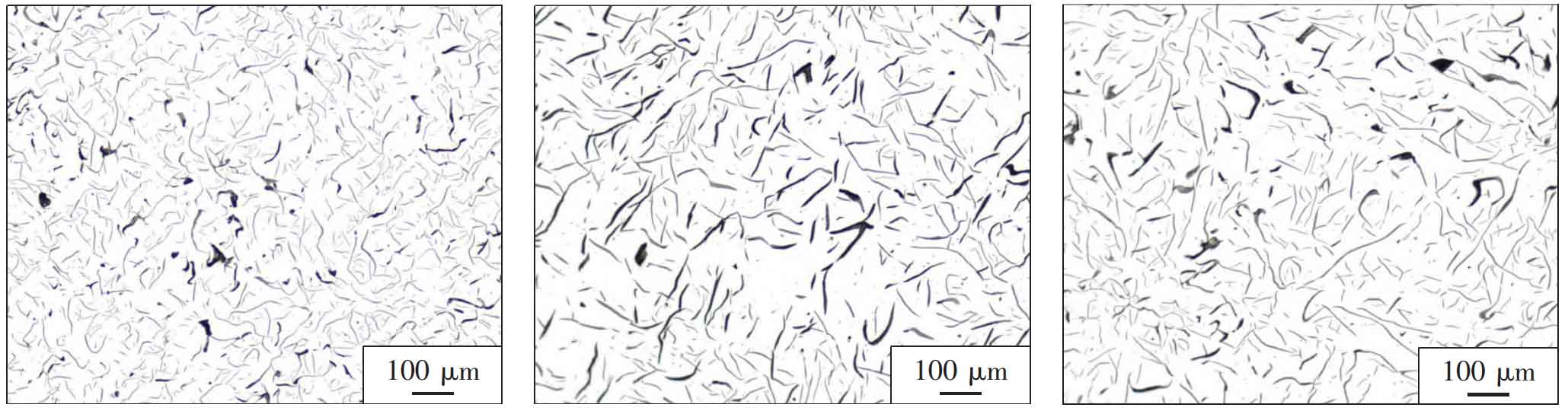
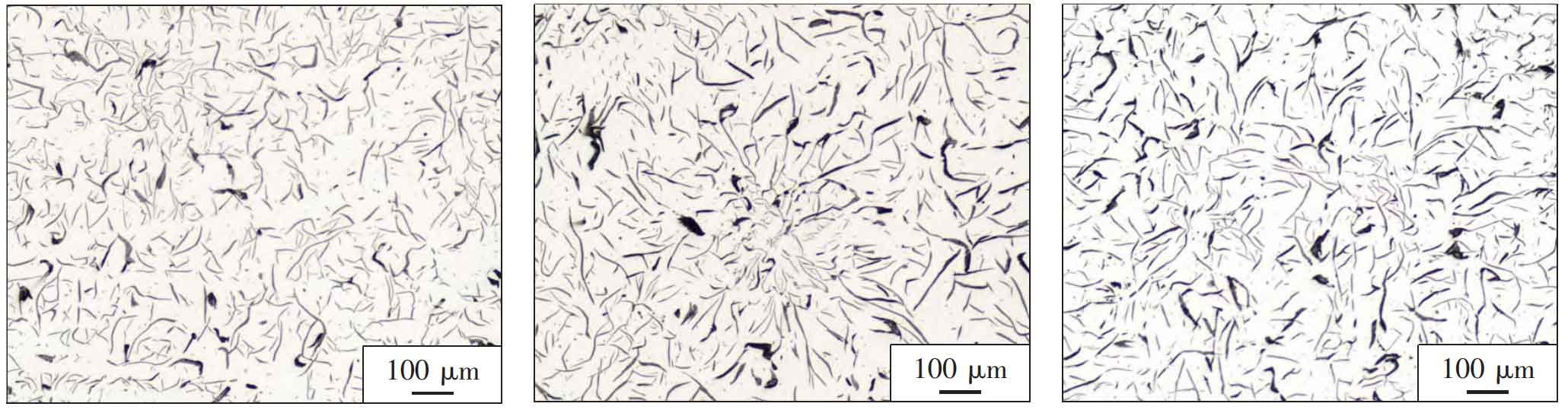
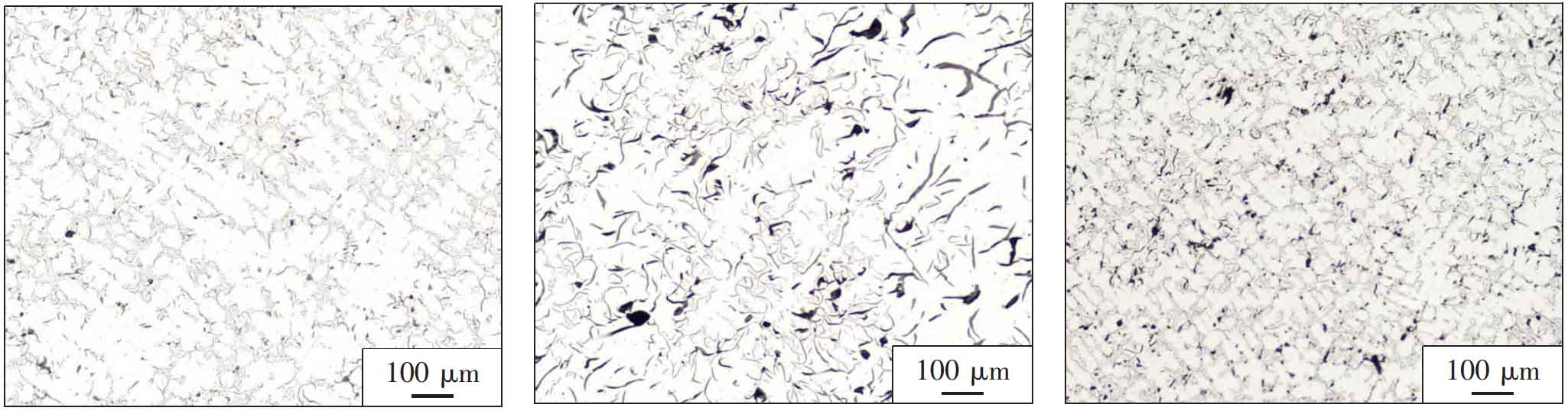
Comparing the graphite morphology of samples with different w (TI), it is found that Ti also has a significant effect on the graphite morphology of gray cast iron brake discs. Figure 2 compares the graphite morphology of three samples with different w (TI) in polished state. Compared with the sample with 0.01% w (TI), the graphite of 0.03% sample is longer, which indicates that Ti element shows the characteristic of promoting graphitization. Compared with the samples with w (TI) content of 0.01% and 0.03%, the graphite of the samples with w (TI) content of 0.12% is relatively fine, and typical D-type graphite appears, indicating that Ti element shows the characteristics of refining A-type graphite at this time.
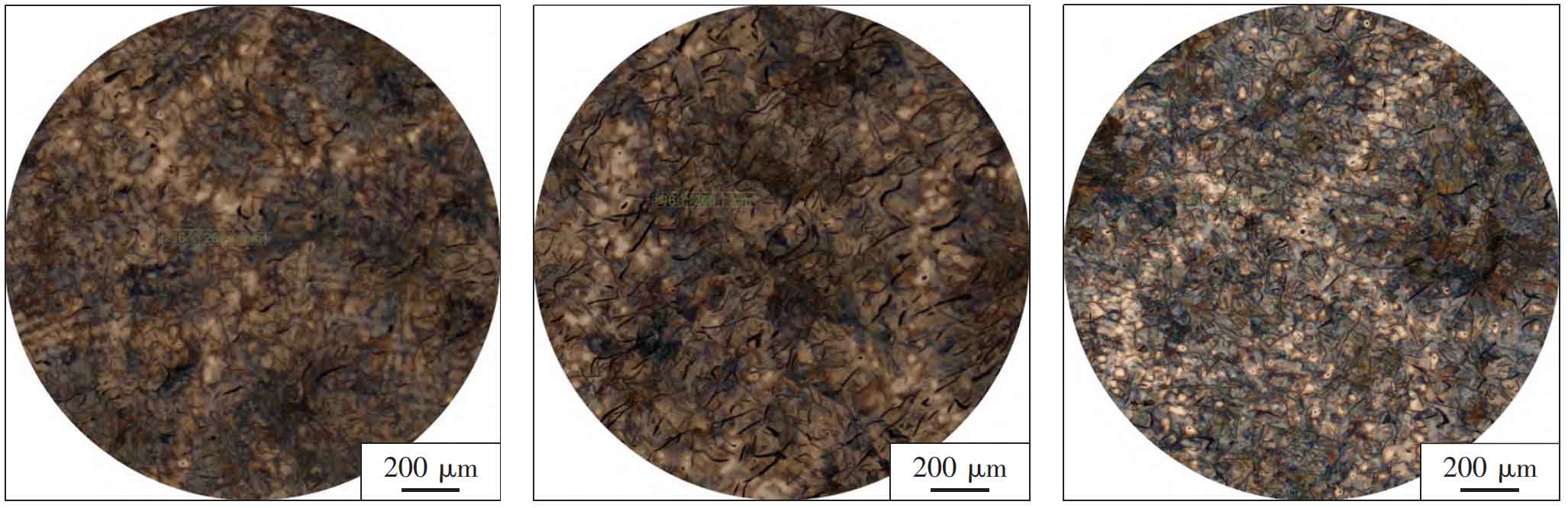
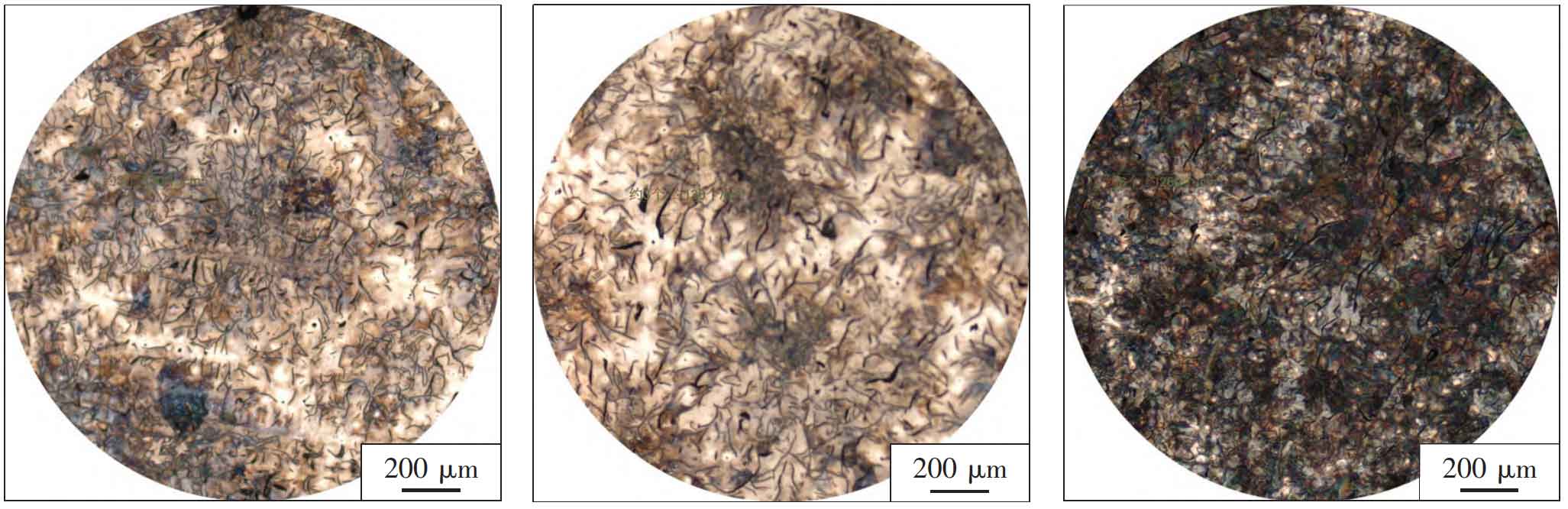
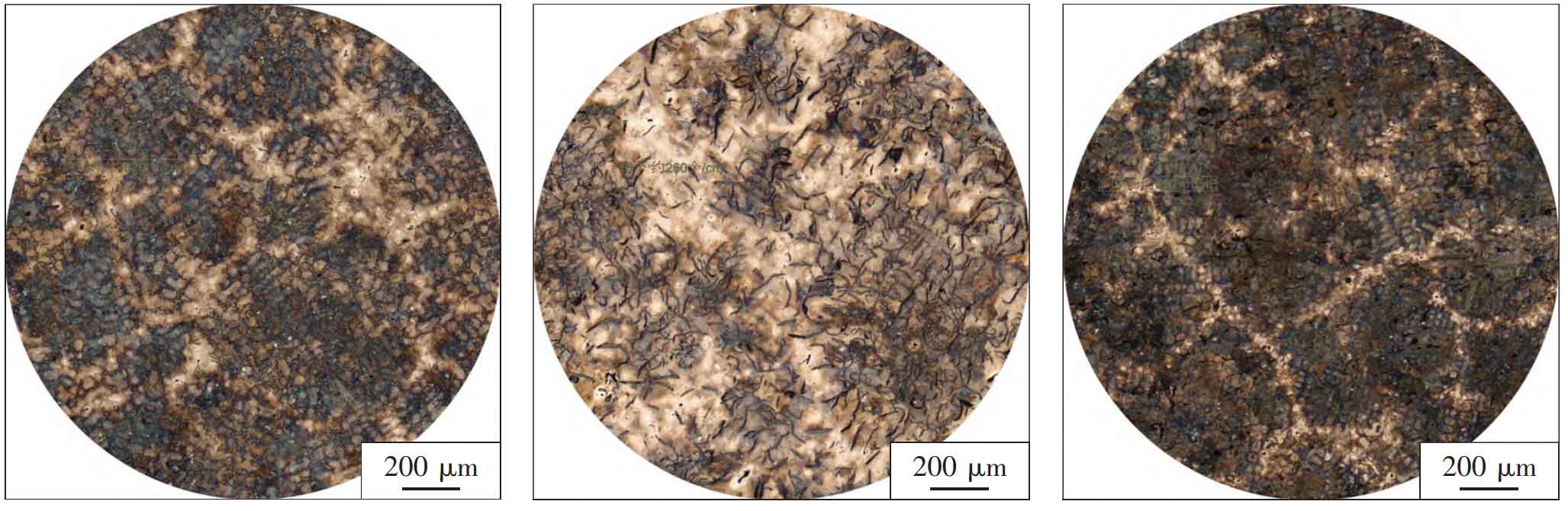
By comparing the number of eutectic clusters of samples with different w (TI) content, it is found that Ti also has a significant effect on the eutectic clusters of gray cast iron brake discs. Figure 3 shows the number of eutectic clusters at different positions of samples with different w (TI), and table 2 shows the number of eutectic clusters of samples with different w (TI). It can be seen that when the amount of W (TI) is within 0.01% – 0.12%, with the increase of the amount of W (TI), first increase the size of eutectic clusters and reduce the number of eutectic clusters, and then reduce the size of eutectic clusters and increase the number of eutectic clusters.
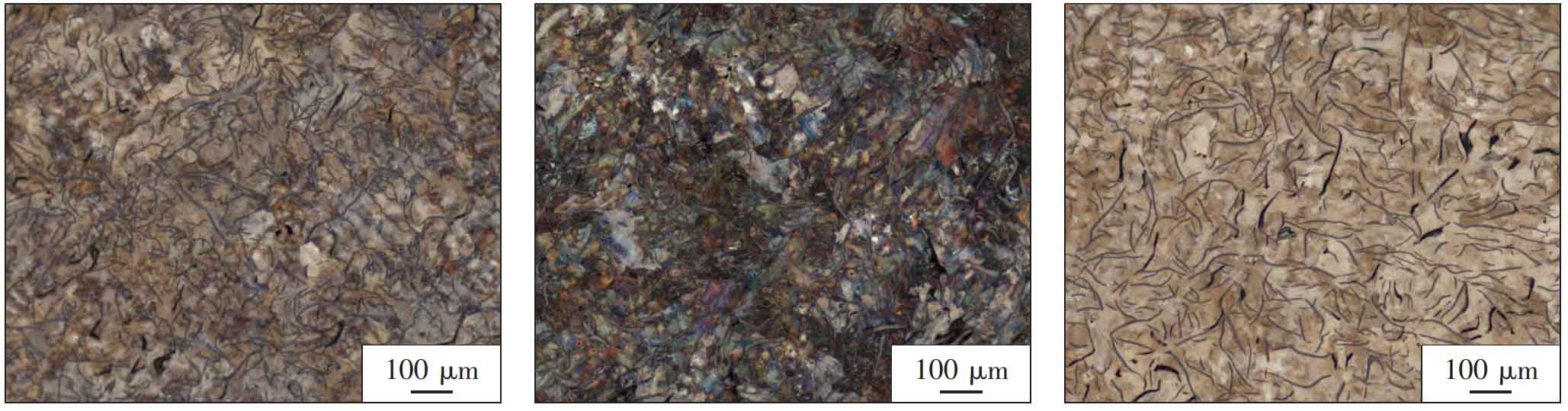
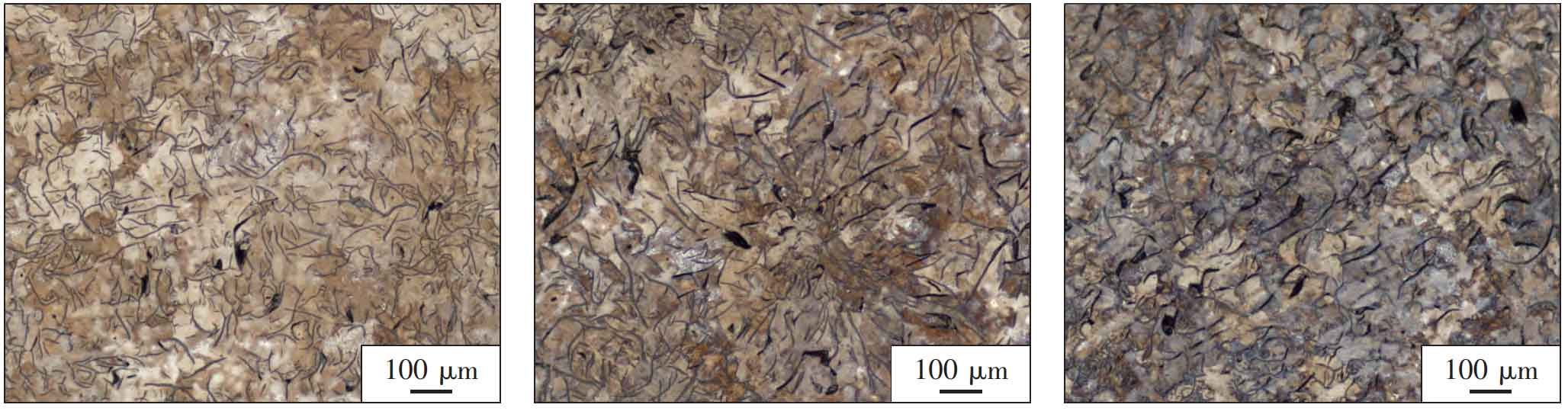
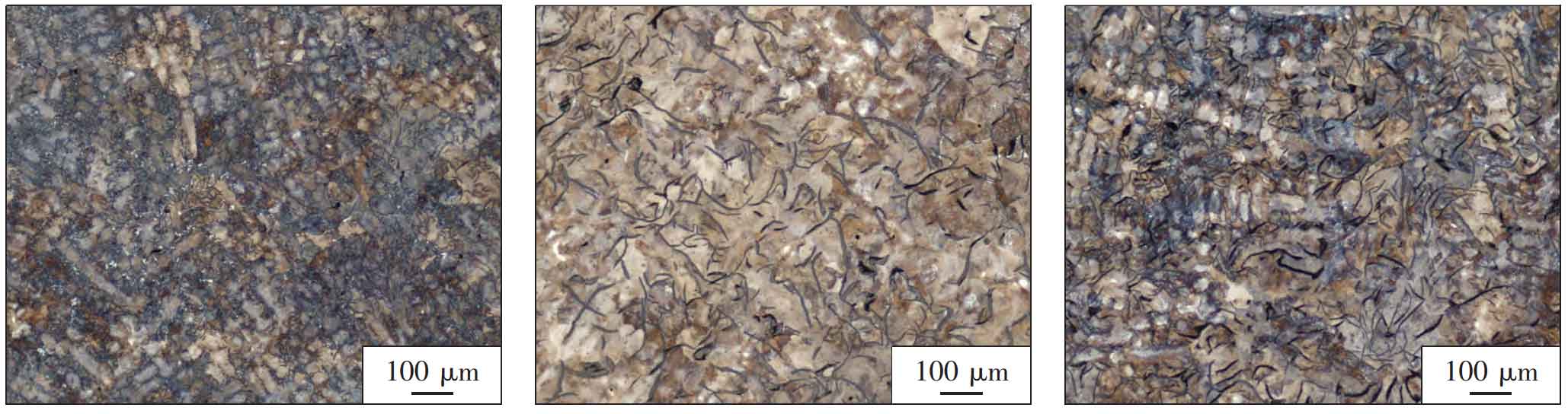
Comparing the matrix structure of samples with different w (TI) content, it is found that when the w (TI) content is high, the matrix structure will also change. Figure 4 shows the matrix structure at different positions of samples with different w (TI) content, and table 3 shows the test results of matrix structure. It can be seen that when the amount of W (TI) reaches 0.12%, more ferrite appears in the matrix under the same conditions.
location | w(Ti)0.01% | w(Ti)0.03% | w(Ti)0.12% |
① | 260 | 130 | 520 |
② | 260 | 130 | 260 |
③ | 260 | 260 | 390 |
Comparing the internal casting defects of samples with different w (TI) amount, X-ray flaw detection was used to detect. No shrinkage casting defects were found in the samples with 0.01% w (TI) amount, 1% shrinkage casting defects were found in the samples with 0.03% w (TI) amount, 100% shrinkage casting defects were found in the samples with 0.12% w (TI) amount, and a few hole casting defects were also found in the finishing turning process (as shown in Figure 5), Under the scanning electron microscope, dendrites can be observed inside the hole casting defects, which can be determined as shrinkage casting defects (as shown in Figure 6).
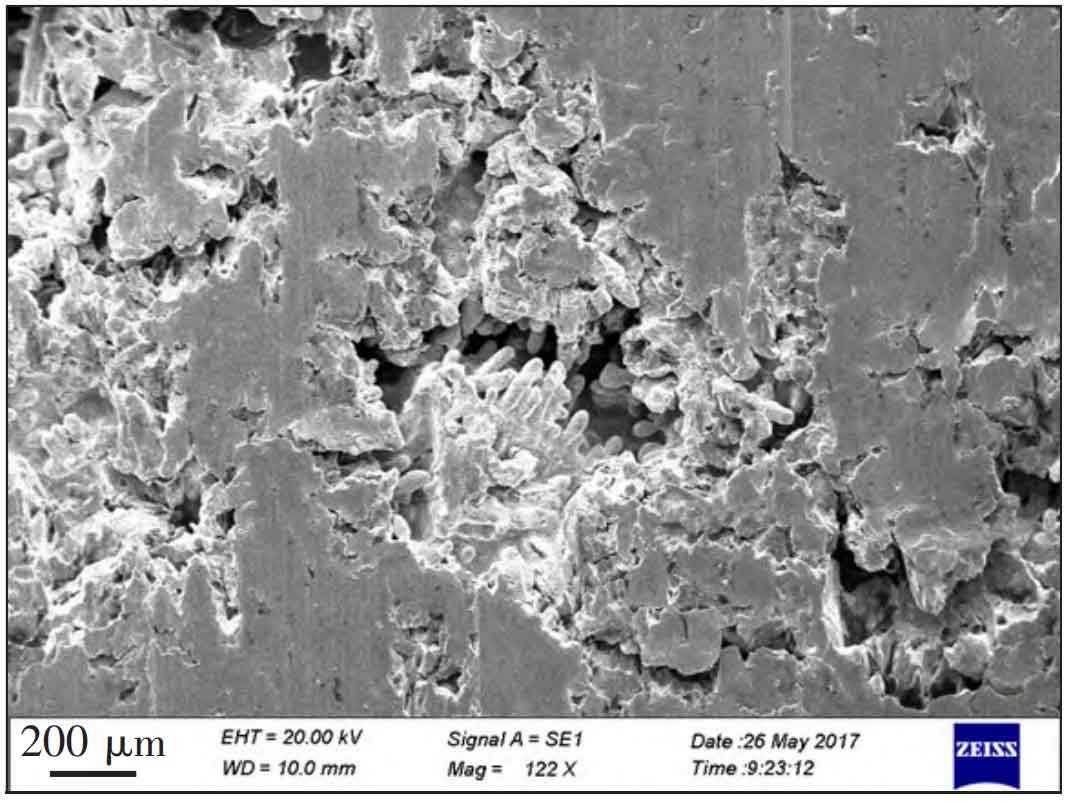
In addition, the machining process was also observed. It was found that the samples with 0.01% and 0.03% w (TI) did not find obvious waste knives and difficult turning during the turning process, but the samples with 0.12% w (TI) could obviously hear the abnormal sound of the lathe during the turning process. The performance is particularly obvious in the grinding process. With the same grinding equipment and the same grinding process, no abnormal grinding pattern is found when the w (TI) amount is 0.01% and 0.03%, but when the sample with w (TI) amount is 0.12%, the grinding machine sound is abnormal, and the phenomenon of grinding immobility occurs, that is, the turning knife pattern can still be seen after grinding (as shown in Figure 7). According to the information, the reason why turning / grinding is difficult is that Ti and N or C form hard compounds.
location | w(Ti)0.01% | w(Ti)0.03% | w(Ti)0.12% |
① | >99%P | >99%P | 95%P+5%F |
② | >99%P | >99%P | 95%P+5%F |
③ | >99%P | >99%P | 95%P+5%F |