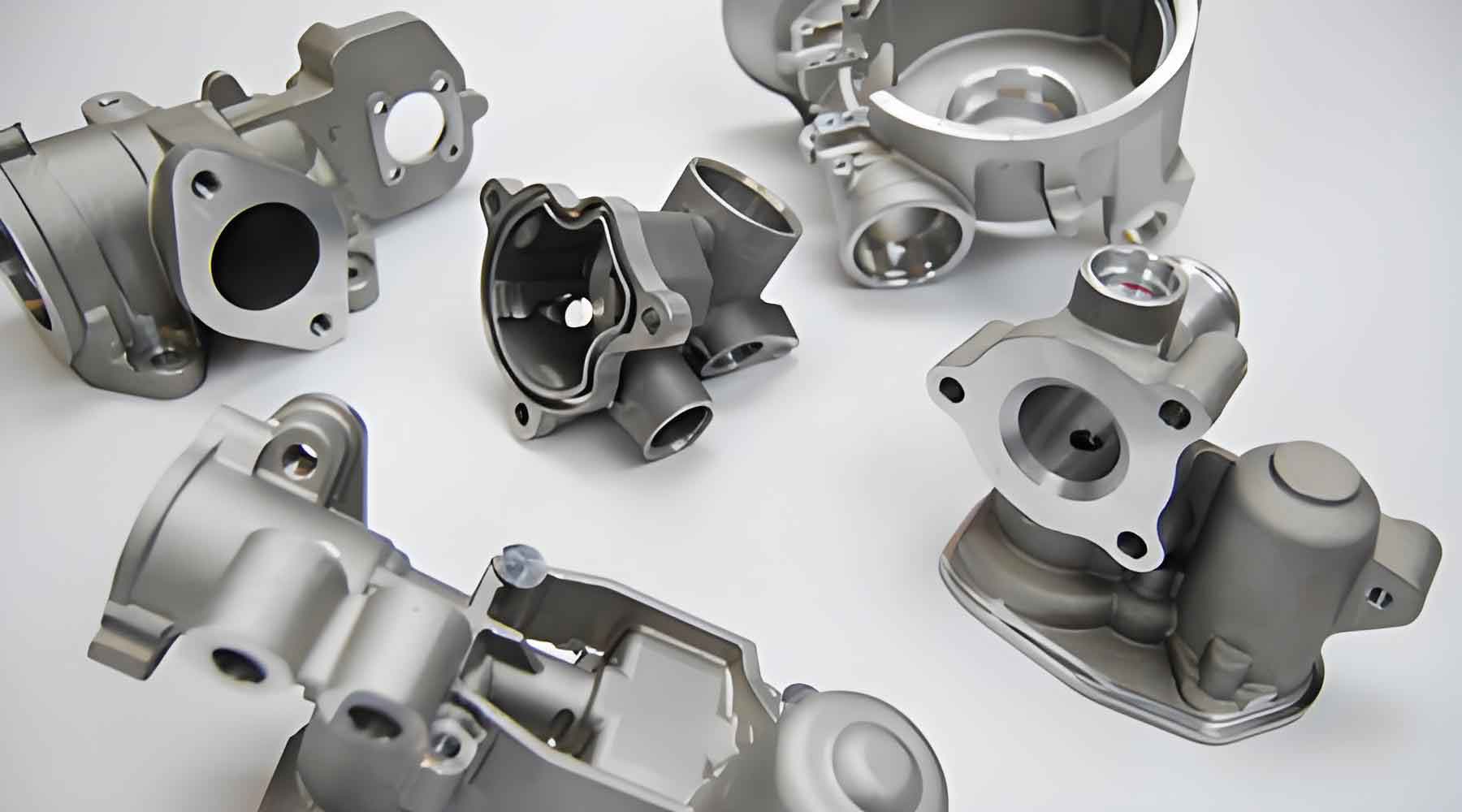
Precision casting is critical manufacturing process used to create high-precision, complex metal components. Ensuring the quality of these castings is paramount, particularly in industries such as aerospace, automotive, and medical devices, where component reliability and performance are crucial. This article delves into the various quality control and inspection methods employed in precision casting, highlighting their importance, techniques, and benefits.
Introduction to Precision Casting
Precision casting involves creating a wax model, which is then coated with a ceramic shell to form a mold. Once the wax is melted away, molten metal is poured into the mold to produce a highly accurate and detailed metal part. This process is renowned for its ability to produce components with intricate geometries, tight tolerances, and excellent surface finishes.
Importance of Quality Control in Precision Casting
Quality control in precision casting is essential for several reasons:
- Ensuring Dimensional Accuracy: Components must meet stringent dimensional specifications to function correctly in their applications.
- Detecting Defects: Early identification of defects helps reduce waste and improve overall production efficiency.
- Meeting Industry Standards: Compliance with industry standards and customer requirements is crucial for market acceptance.
- Enhancing Performance and Reliability: High-quality castings ensure better performance and reliability of the final products.
Key Quality Control and Inspection Methods
- Dimensional Inspection
- Non-Destructive Testing (NDT)
- Visual Inspection
- Material Analysis
- Process Monitoring and Control
Dimensional Inspection
Dimensional inspection verifies that the cast components meet the specified dimensions and tolerances. Techniques include:
- Coordinate Measuring Machines (CMM): Provide precise measurements of casting dimensions.
- Laser Scanning: Captures detailed surface geometry and compares it to the original CAD model.
Technique | Accuracy | Applications |
---|---|---|
Coordinate Measuring Machine (CMM) | Very High | Complex geometries, tight tolerances |
Laser Scanning | High | Surface profiling, dimensional verification |
Non-Destructive Testing (NDT)
NDT methods detect internal and surface defects without damaging the castings. Common NDT methods include:
- X-Ray Radiography: Reveals internal defects such as porosity, inclusions, and cracks.
- Ultrasonic Testing: Detects internal flaws and measures material thickness.
- Dye Penetrant Testing: Identifies surface cracks and defects.
NDT Method | Defect Detection | Applications |
---|---|---|
X-Ray Radiography | Internal | Complex internal structures |
Ultrasonic Testing | Internal | Thickness measurement, flaw detection |
Dye Penetrant Testing | Surface | Surface cracks, defects |
Visual Inspection
Visual inspection is a straightforward technique used to identify surface defects and irregularities. It includes:
- Manual Inspection: Conducted by skilled inspectors using visual aids and magnification.
- Automated Inspection Systems: Employ cameras and machine learning algorithms to detect defects.
Method | Accuracy | Applications |
---|---|---|
Manual Inspection | Moderate | General surface defects, irregularities |
Automated Inspection | High | Consistent defect detection, high-volume production |
Material Analysis
Material analysis ensures that the chemical composition and mechanical properties of the castings meet specifications. Techniques include:
- Spectroscopy: Determines the elemental composition of the metal.
- Hardness Testing: Measures the hardness of the casting to ensure it meets required standards.
- Tensile Testing: Evaluates the tensile strength and ductility of the material.
Technique | Information Provided | Applications |
---|---|---|
Spectroscopy | Elemental composition | Alloy verification, quality control |
Hardness Testing | Hardness values | Material property verification |
Tensile Testing | Tensile strength, ductility | Mechanical performance evaluation |
Process Monitoring and Control
Real-time monitoring and control of the casting process are vital for maintaining consistent quality. This includes:
- Temperature Monitoring: Ensures the molten metal is poured at the correct temperature.
- Flow Control: Regulates the flow of metal to prevent turbulence and incomplete filling.
- Environmental Control: Monitors humidity and temperature to ensure optimal conditions for foam pattern and coating.
Parameter | Monitoring Method | Impact on Quality |
---|---|---|
Temperature | Thermocouples, infrared sensors | Metal fluidity, foam evaporation |
Flow Control | Automated systems | Defect reduction, mold filling |
Environmental Control | Humidity and temperature sensors | Pattern stability, coating performance |
Benefits of Effective Quality Control
Implementing effective quality control techniques in precision casting offers several benefits:
- Reduced Defects: Identifying and addressing defects early in the process reduces scrap rates and rework.
- Enhanced Product Quality: Ensures castings meet or exceed customer specifications and performance requirements.
- Increased Efficiency: Streamlined processes and reduced waste lead to higher production efficiency and cost savings.
- Improved Customer Satisfaction: Delivering high-quality products enhances customer trust and loyalty.
Case Studies
Case Study 1: Aerospace Turbine Blades
An aerospace manufacturer implemented comprehensive quality control techniques, including CMM for dimensional inspection and X-ray radiography for internal defect detection. The results were a significant reduction in defects and improved overall quality.
Metric | Before QC Implementation | After QC Implementation |
---|---|---|
Defect Rate | 8% | 3% |
Dimensional Tolerance | ±0.5 mm | ±0.3 mm |
Production Efficiency | 85% | 92% |
Case Study 2: Medical Implants
A manufacturer of medical implants used automated inspection systems and advanced material analysis to enhance quality control. This approach led to a reduction in defects and increased reliability of the cast components.
Metric | Before QC Implementation | After QC Implementation |
---|---|---|
Defect Rate | 6% | 2% |
Dimensional Tolerance | ±0.4 mm | ±0.2 mm |
Production Efficiency | 80% | 88% |
Future Directions in Quality Control
The future of quality control in precision casting includes several promising advancements:
- Integration of AI and Machine Learning
- Predictive Analytics: Using AI to predict and prevent defects based on historical data.
- Automated Decision-Making: Implementing machine learning algorithms to optimize process parameters in real-time.
- Advanced NDT Technologies
- 3D X-Ray Imaging: Providing detailed internal views of castings for better defect detection.
- Laser Ultrasonics: Offering high-resolution measurements of internal defects and material properties.
- Enhanced Process Monitoring
- Internet of Things (IoT) Devices: Using IoT sensors to continuously monitor and control process parameters.
- Real-Time Data Analytics: Leveraging big data analytics to improve process efficiency and quality control.
Conclusion
Quality control and inspection methods are critical to the success of precision casting processes. By employing a range of techniques such as dimensional inspection, non-destructive testing, visual inspection, material analysis, and process monitoring, manufacturers can ensure that their cast components meet the highest standards of quality and performance. As technology continues to evolve, the integration of AI, advanced NDT technologies, and IoT devices will further enhance the capabilities of quality control in precision casting, leading to even greater improvements in efficiency, reliability, and customer satisfaction.