Quality control in casting product manufacturing is crucial for ensuring the integrity, reliability, and performance of the final products. Implementing best practices and adhering to industry standards can significantly improve the quality and consistency of casting products. Here’s an overview of key best practices and standards in this field:
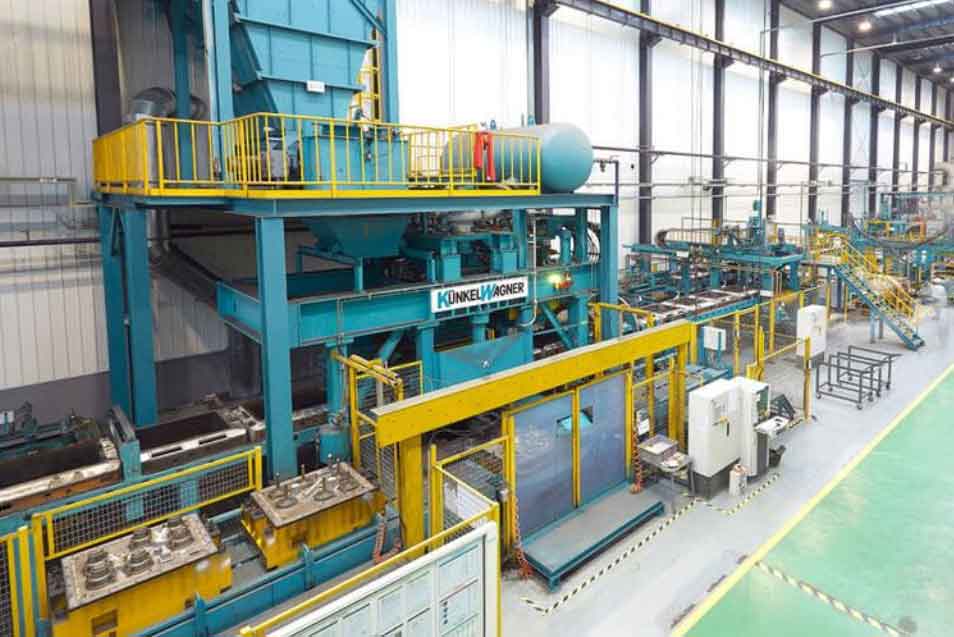
Best Practices in Quality Control for Casting
- Design Review and Simulation:
- Conduct thorough design reviews to ensure the mold design is optimized for quality.
- Use simulation software to predict potential issues such as cold shuts, misruns, and hot tears.
- Material Quality Assurance:
- Implement stringent controls on material sourcing to ensure purity and appropriateness for the application.
- Regularly test material properties like tensile strength, elongation, and hardness.
- Process Control:
- Standardize casting processes, including melting, mold making, pouring, and cooling, to reduce variability.
- Utilize process control software to monitor parameters like temperature and pouring rate in real time.
- Inspection and Testing:
- Apply non-destructive testing methods such as X-ray, ultrasound, and magnetic particle inspection to detect internal and surface defects.
- Conduct destructive testing on sample parts to assess performance under stress conditions.
- Employee Training:
- Provide ongoing training for operators on the latest casting techniques and quality standards.
- Foster a culture of quality and continuous improvement among staff.
- Preventive Maintenance:
- Regularly maintain and inspect equipment to prevent breakdowns that could compromise quality.
- Calibrate instruments and machinery to ensure accurate measurements and operations.
Standards in Casting Product Manufacturing
- ASTM Standards:
- ASTM A802 for visual inspection criteria.
- ASTM E446, E186, and E280 for radiographic examination standards.
- ISO Standards:
- ISO 9001 for quality management systems which ensures consistency in product quality.
- ISO 4990 for steel castings – general technical delivery conditions.
- Other International Standards:
- EN 1371 for foundry machinery – liquid penetrant inspection.
- SAE AMS 2175 for classifying discontinuities in metal castings from non-destructive examinations.
Adhering to these practices and standards not only helps in minimizing defects and failures in casting products but also enhances customer satisfaction and maintains competitive advantage in the market. Implementing a rigorous quality control program is essential for manufacturers looking to uphold high standards in casting production.