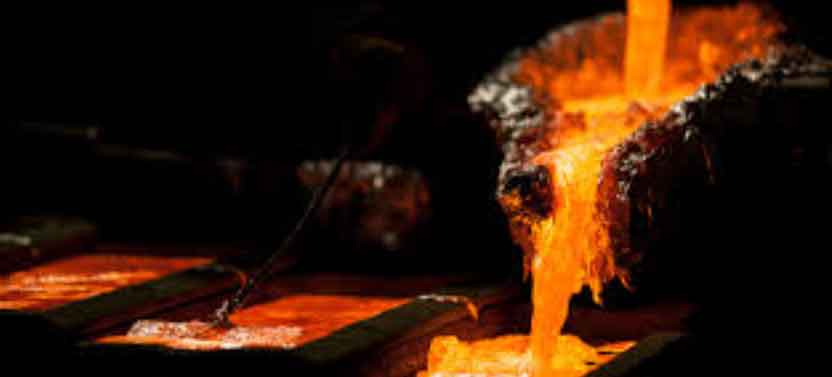
Quality control is a critical aspect of the casting process in China to ensure the production of reliable and high-quality cast components. Effective quality control measures help casting foundries meet international standards and satisfy the requirements of their global customers. Here are some key aspects of quality control in China casting foundries:
1. Process Control and Standardization:
Casting foundries in China implement stringent process control measures to ensure consistency in casting production. Standardizing the casting process helps reduce variations and ensures that each cast component meets the specified requirements.
2. Material Inspection:
Foundries conduct thorough material inspections to verify the quality and suitability of the raw materials used in casting. Material testing ensures that the castings have the desired mechanical properties and can withstand the intended applications.
3. Dimensional Accuracy and Tolerances:
Precision in dimensions and tolerances is crucial for cast components. Quality control teams use advanced measurement tools and techniques to check the dimensional accuracy of castings and ensure they meet the required specifications.
4. Non-Destructive Testing (NDT):
NDT techniques such as ultrasonic testing, radiographic testing, and dye penetrant inspection are employed to detect internal and surface defects in castings without damaging the components.
5. Visual Inspection:
Foundries conduct visual inspections to identify surface defects, surface finish, and overall appearance of cast components. Visual inspection ensures that the castings are free from defects that could affect their functionality or appearance.
6. Mechanical Testing:
Mechanical testing, including tensile strength testing, hardness testing, and impact testing, is carried out to verify the mechanical properties and performance of the castings.
7. In-Process Inspection:
Quality control personnel conduct in-process inspections at various stages of the casting process to identify and rectify any potential issues before they affect the final product.
8. Final Inspection and Sampling:
Before shipping, each batch of cast components undergoes final inspection. This inspection may involve random sampling to verify the quality and consistency of the entire batch.
9. Documentation and Traceability:
Quality control processes in Chinese casting foundries are well-documented to ensure traceability of materials, processes, and inspection results. Proper documentation helps in identifying any issues that may arise during the production process.
10. Certification and Compliance:
Casting foundries in China may obtain certifications such as ISO 9001, ISO 14001, or other industry-specific certifications to demonstrate their commitment to quality management and environmental standards.
11. Customer Feedback and Continuous Improvement:
Chinese casting foundries actively seek feedback from their customers and use this information to improve their processes and product quality continually.
12. Training and Skilled Workforce:
Foundries invest in the training of their workforce to ensure that employees possess the necessary skills and knowledge to execute quality control procedures effectively.
By prioritizing quality control, Chinese casting foundries can produce reliable and high-quality cast components that meet the expectations of global customers. Through continuous improvement and adherence to international standards, these foundries contribute to the success of their clients in various industries worldwide.