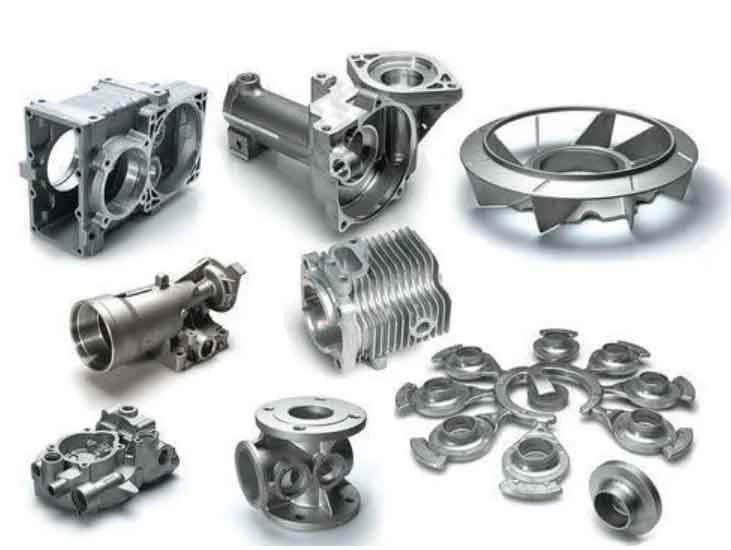
Grey Cast Iron: Properties, Production, and Applications
Grey cast iron, often referred to as gray iron, is a widely used engineering material known for its excellent casting properties, low cost, and good machinability. It is one of the oldest and most popular types of cast iron, primarily composed of carbon, silicon, and iron, with small amounts of other elements. In this guide, we will explore the properties, production methods, and applications of grey cast iron.
Properties of Grey Cast Iron:
- Graphite Structure: Grey cast iron gets its name from the graphite flakes that form within its microstructure. These flakes provide unique properties like good vibration dampening, self-lubrication, and low wear rate.
- Brittleness: While grey cast iron offers excellent castability, it is relatively brittle compared to other cast irons. This limits its use in applications requiring high tensile strength and impact resistance.
- Machinability: Grey cast iron is known for its excellent machinability due to the graphite flakes, which create small chips and reduce tool wear during machining processes.
- Thermal Conductivity: The graphite structure enhances grey cast iron’s thermal conductivity, making it suitable for applications involving heat transfer.
- Corrosion Resistance: Grey cast iron can be susceptible to certain forms of corrosion, but its resistance can be improved through surface treatments and alloy additions.
- Density: Grey cast iron has a relatively high density, making it suitable for applications requiring weight and inertia.
Production of Grey Cast Iron:
Grey cast iron is produced through a casting process called sand casting, which is one of the most common methods used for iron casting. The steps involved in grey cast iron production are as follows:
- Pattern Creation: A pattern, typically made of wood or metal, is created based on the desired shape of the final casting.
- Mold Preparation: The pattern is used to create a mold cavity in a mixture of sand and a bonding agent (usually clay or resin). The mold consists of two halves, the cope and the drag, which are placed together to form the complete mold cavity.
- Pouring: Molten iron, along with alloying elements if required, is poured into the mold cavity. The molten metal flows through the mold and fills the space occupied by the pattern.
- Solidification: The molten metal cools and solidifies inside the mold, taking the shape of the pattern.
- Cooling and Shakeout: After solidification, the casting is allowed to cool before the mold is removed, and the cast part is separated from the mold (shakeout).
- Finishing: The casting may undergo various finishing operations, such as cutting off the gates and risers, cleaning, and machining to achieve the desired final shape and surface finish.
Applications of Grey Cast Iron:
Grey cast iron finds numerous applications across various industries, including:
- Automotive Industry: Engine blocks, cylinder heads, brake components, and other automotive parts.
- Construction: Manhole covers, pipes, fittings, and construction equipment parts.
- Machine Tool Industry: Bed plates, machine bases, and components for machine tools.
- Pumps and Valves: Pump housings, valve bodies, and impellers.
- Railway Industry: Railway brake shoes, brake discs, and other components.
- Agricultural Machinery: Components for tractors and agricultural equipment.
- Cookware: Some traditional cookware items are made of grey cast iron due to their excellent heat retention properties.
Grey cast iron’s versatility, cost-effectiveness, and ease of casting make it a popular choice for a wide range of applications. However, its brittleness limits its use in load-bearing and high-stress applications, where other types of cast iron or materials may be more suitable.