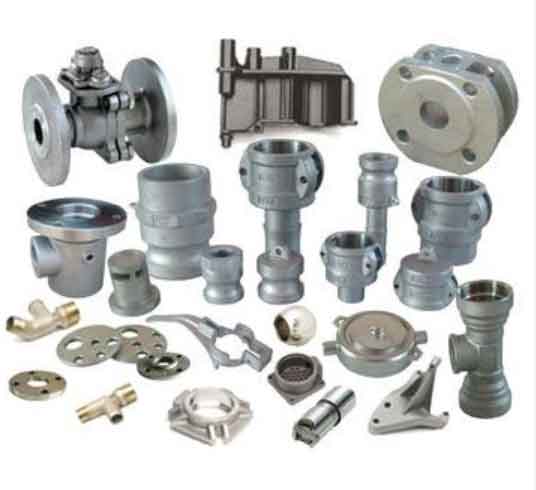
Quality control in sand casting is crucial to ensure the consistency and precision of cast parts. By implementing effective quality control measures, manufacturers can identify and rectify any issues during the casting process, resulting in high-quality and reliable components. Here are some key aspects of quality control in sand casting:
- Process control: Establish and document standardized procedures for each stage of the casting process, including pattern making, mold preparation, metal pouring, and cooling. Monitor and control process variables such as sand properties, sand mixture composition, moisture content, mold density, and metal pouring temperature.
- Inspection and testing: Perform regular inspections and testing throughout the casting process to detect any defects or deviations. This can include visual inspections, dimensional measurements, non-destructive testing (such as X-ray or ultrasonic testing), and mechanical testing (such as tensile testing or hardness testing) of test samples.
- Quality assurance documentation: Maintain comprehensive documentation of quality control procedures, inspection records, and test results. This documentation helps ensure traceability and facilitates the identification and resolution of any quality issues that may arise.
- Mold and pattern maintenance: Regularly inspect and maintain molds and patterns to ensure their dimensional accuracy and surface finish. Proper maintenance helps prevent defects caused by worn-out or damaged molds and patterns.
- Metal quality control: Control the quality of the molten metal used in the casting process by monitoring its chemical composition, cleanliness, and temperature. Conduct periodic metal analysis and metal treatment (such as degassing or alloying) to maintain the desired metal properties.
- Defect analysis and corrective actions: Establish a systematic approach to identify, analyze, and address casting defects. Implement root cause analysis techniques to identify the underlying causes of defects and develop corrective and preventive actions to eliminate or minimize the occurrence of such defects in the future.
- Training and skill development: Provide adequate training and skill development programs for the workforce involved in sand casting. Ensure that operators and inspectors are knowledgeable about quality control procedures, casting standards, and defect identification techniques.
- Continuous improvement: Foster a culture of continuous improvement by regularly reviewing quality control processes, analyzing performance metrics, and implementing corrective actions. Seek feedback from customers and incorporate their input to enhance the quality of cast parts.
- Supplier evaluation and qualification: Evaluate and qualify suppliers of sand, additives, and other materials used in the casting process. Ensure that suppliers meet quality standards and consistently deliver materials that meet the required specifications.
- Statistical process control (SPC): Implement SPC techniques to monitor and control critical process parameters. Use statistical tools to analyze process data, identify trends, and take proactive measures to maintain process stability and improve overall quality.
By implementing these quality control measures, manufacturers can ensure the consistency, precision, and reliability of sand castings. This, in turn, leads to improved customer satisfaction, reduced scrap rates, and increased operational efficiency.