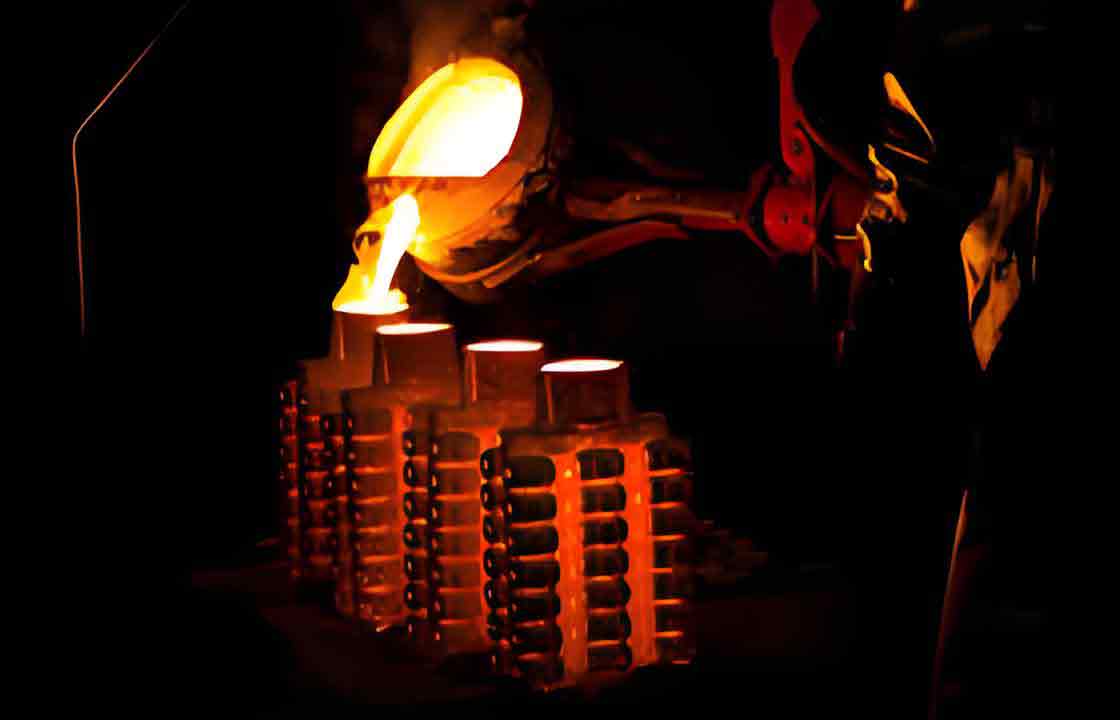
Lost wax casting is highly precise and versatile manufacturing process used to produce complex and intricate metal components. Despite its numerous advantages, lost wax casting can be prone to various casting defects that can compromise the quality and performance of the final products. Identifying and addressing these defects is essential for improving yield rates and reducing costs. This article explores common casting defects in lost wax casting, their causes, and effective strategies for minimizing them.
Introduction to Lost Wax Casting
Lost wax casting involves creating a wax model of the desired part, which is then coated with a ceramic shell. The wax is melted out, leaving a cavity that is filled with molten metal. Once the metal solidifies, the ceramic shell is removed to reveal the metal casting. This process is particularly advantageous for producing components with complex geometries and fine details.
Key Steps in Lost Wax Casting
- Pattern Creation: A wax model of the desired part is created using injection molding or hand carving.
- Assembly: Multiple wax models can be assembled onto a wax tree to create multiple parts in a single batch.
- Shell Building: The wax assembly is repeatedly dipped into a ceramic slurry and coated with fine sand to build a ceramic shell.
- Dewaxing: The ceramic shell is heated to remove the wax, leaving a hollow cavity.
- Metal Pouring: Molten metal is poured into the ceramic mold.
- Shell Removal: Once the metal has solidified, the ceramic shell is broken away to reveal the casting.
- Finishing: The casting is cleaned, and any excess material is removed to achieve the final product.
Common Casting Defects in Lost Wax Casting
Several casting defects can occur during the lost wax casting process. Understanding these defects, their causes, and methods for reducing them is crucial for producing high-quality castings.
1. Surface Roughness
Surface roughness is a common casting defect that affects the surface finish of the casting. It is often caused by poor-quality wax patterns or improper application of the ceramic slurry.
- Causes: Poor-quality wax patterns, improper ceramic slurry application, inadequate drying between coats.
- Reduction Strategies:
- Use high-quality wax and precise pattern-making techniques.
- Ensure uniform application of ceramic slurry.
- Allow adequate drying time between slurry coats.
2. Inclusions
Inclusions are foreign particles embedded in the casting surface, which can weaken the material and affect its appearance.
- Causes: Contaminants in the molten metal, improper handling of ceramic shells, environmental contamination.
- Reduction Strategies:
- Maintain a clean working environment.
- Filter molten metal before pouring.
- Ensure proper handling and storage of ceramic shells.
3. Porosity
Porosity refers to small voids or cavities within the casting, often caused by trapped gases or shrinkage during solidification.
- Causes: Trapped gases, inadequate venting, improper cooling rates, shrinkage.
- Reduction Strategies:
- Control metal pouring temperature and speed.
- Use degassing techniques to remove trapped gases.
- Optimize risers and feeders to manage shrinkage.
- Ensure proper venting of molds.
4. Shell Cracking
Shell cracking occurs when the ceramic shell cracks during the casting process, leading to defects in the casting surface.
- Causes: Improper shell building, thermal stresses during dewaxing or metal pouring.
- Reduction Strategies:
- Apply ceramic slurry uniformly.
- Allow proper drying between coats.
- Control the rate of heating and cooling during dewaxing and metal pouring.
5. Misruns and Cold Shuts
Misruns occur when the molten metal does not completely fill the mold, while cold shuts happen when two streams of metal meet but do not fuse properly.
- Causes: Low pouring temperature, slow pouring speed, inadequate mold preheating.
- Reduction Strategies:
- Maintain proper metal pouring temperature.
- Ensure consistent and adequate pouring speed.
- Preheat molds to appropriate temperatures.
6. Dimensional Variations
Dimensional variations occur when the final casting dimensions deviate from the desired specifications.
- Causes: Wax pattern shrinkage, ceramic shell deformation, improper mold assembly.
- Reduction Strategies:
- Use precise pattern-making techniques to minimize shrinkage.
- Ensure stable and consistent ceramic shell building.
- Verify and adjust mold assembly to maintain dimensional accuracy.
Effective Strategies for Reducing Casting Defects
Reducing casting defects in lost wax casting requires a combination of process optimization, quality control, and advanced techniques. The following strategies can help minimize defects and improve the overall quality of castings.
Process Optimization
- Wax Pattern Quality: Ensure high-quality wax patterns by using precise injection molding techniques and high-quality wax.
- Ceramic Shell Building: Optimize the ceramic shell building process by ensuring uniform slurry application, proper drying, and stable shell structure.
- Metal Pouring Parameters: Control metal pouring temperature, speed, and degassing to prevent defects related to trapped gases and shrinkage.
Quality Control
- Non-Destructive Testing: Implement non-destructive testing methods, such as X-ray and ultrasonic testing, to detect internal defects early.
- Automated Inspection: Use automated inspection systems to identify and address defects during the production process.
- Strict Protocols: Establish and adhere to strict quality control protocols at each stage of the casting process.
Advanced Techniques
- Simulation Software: Use casting simulation software to predict and address potential defects before production.
- Vacuum Casting: Implement vacuum casting techniques to reduce porosity and improve overall casting quality.
- Continuous Improvement: Continuously monitor and improve casting processes based on feedback and defect analysis.
Case Studies: Reducing Casting Defects in Lost Wax Casting
Case Study 1: Aerospace Components
A manufacturer of aerospace components faced issues with porosity and inclusions in their lost wax castings. By implementing vacuum casting techniques and using high-quality ceramic materials, they significantly reduced these defects, resulting in higher quality castings suitable for critical aerospace applications.
Case Study 2: Medical Implants
A producer of medical implants experienced surface roughness and dimensional variations in their castings. By optimizing the wax pattern production process and ensuring precise ceramic shell building, they improved the surface finish and dimensional accuracy, making the castings suitable for medical applications.
Case Study 3: Industrial Tools
An industrial tools manufacturer encountered misruns and shell cracking in their castings. By controlling metal pouring parameters and enhancing the ceramic shell building process, they minimized these defects, leading to more durable and reliable tools.
Conclusion
Reducing casting defects in lost wax casting is essential for producing high-quality components and maintaining cost-effectiveness in manufacturing. By understanding common casting defects, their causes, and effective reduction strategies, manufacturers can optimize their processes and improve the overall quality of their castings. Implementing advanced techniques, quality control measures, and continuous improvement initiatives ensures that lost wax casting remains a reliable and efficient method for producing intricate and high-performance metal components.