Lost Foam Casting is a versatile and cost-effective method widely used to produce intricate and precise metal components. However, achieving the desired surface finish and mechanical properties often requires additional post-processing and surface finishing techniques. This article delves into various surface finishing and post-processing techniques employed in lost foam casting, highlighting their significance and methodologies.
Introduction to Lost Foam Casting
Lost Foam Casting involves creating a foam pattern of the desired component, coating it with a refractory material, and embedding it in unbonded sand. When molten metal is poured into the mold, the foam pattern vaporizes, leaving behind a metal casting that replicates the foam pattern. Despite its precision, the process often requires further refinement to meet stringent surface finish and mechanical property requirements.
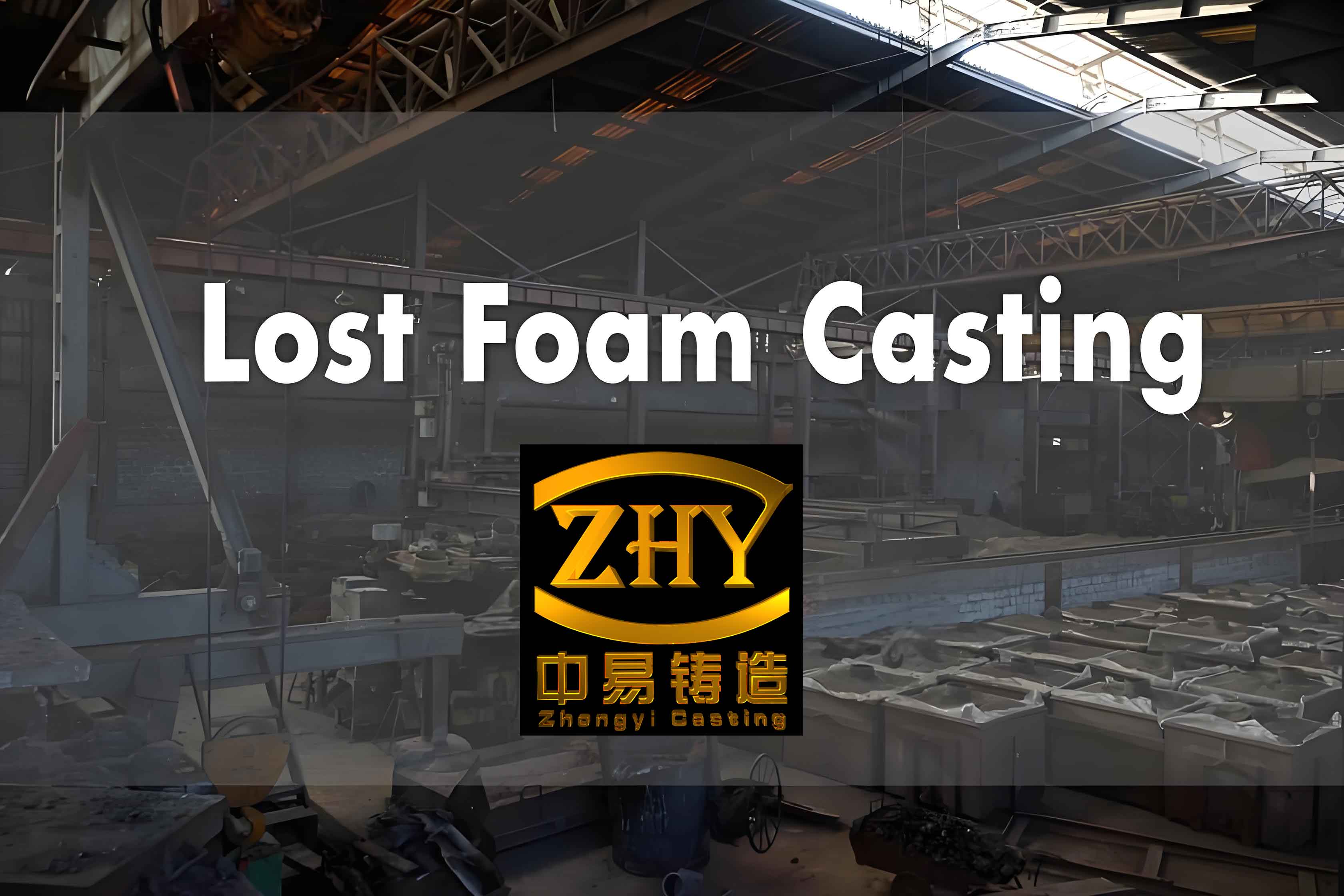
Importance of Surface Finishing and Post-Processing
Surface finishing and post-processing are crucial for enhancing the functional and aesthetic qualities of lost foam casting. These techniques offer several benefits:
- Improved Surface Finish: Achieves smooth and uniform surfaces.
- Enhanced Mechanical Properties: Strengthens and toughens the material.
- Dimensional Accuracy: Refines the dimensions to meet precise tolerances.
- Defect Reduction: Mitigates casting defects and surface imperfections.
- Corrosion Resistance: Increases resistance to environmental degradation.
Surface Finishing Techniques
1. Shot Blasting
Shot blasting is a mechanical surface finishing technique used to clean, strengthen, or polish the metal surface. It involves blasting lost foam casting with high-velocity abrasive materials.
Process:
- The lost foam casting is exposed to a stream of abrasive media such as steel shots or grit.
- The abrasives impact the surface, removing any oxides, scale, or residual sand.
Benefits:
- Surface Cleaning: Removes surface contaminants and impurities.
- Surface Hardening: Increases surface hardness and fatigue resistance.
- Texture Improvement: Provides a uniform surface texture.
2. Tumbling
Tumbling, also known as barrel finishing, is a process where castings are placed in a rotating barrel with abrasives to deburr, polish, or clean the surfaces.
Process:
- Castings are loaded into a barrel along with abrasive media.
- The barrel is rotated, causing lost foam casting and media to tumble and interact.
Benefits:
- Deburring: Smooths out sharp edges and burrs.
- Polishing: Achieves a polished and shiny surface finish.
- Consistency: Ensures consistent finishing across multiple castings.
3. Grinding and Polishing
Grinding and polishing are manual or automated processes that involve removing material from lost foam casting surface to achieve the desired finish.
Process:
- Grinding wheels or abrasive belts are used to remove surface material.
- Polishing compounds and buffing wheels are employed to attain a smooth finish.
Benefits:
- Precision: Allows for precise control over surface finish.
- Smoothness: Achieves a high level of smoothness and gloss.
- Defect Removal: Eliminates surface defects and imperfections.
Post-Processing Techniques
1. Heat Treatment
Heat treatment involves heating and cooling the lost foam casting to alter their physical and mechanical properties. It is essential for enhancing strength, toughness, and wear resistance.
Process:
- Annealing: Heating lost foam casting to a specific temperature and then slowly cooling it to relieve internal stresses.
- Quenching: Rapidly cooling lost foam casting from a high temperature to increase hardness.
- Tempering: Reheating the quenched lost foam casting to a lower temperature to improve toughness.
Benefits:
- Strength Enhancement: Increases tensile and yield strength.
- Toughness Improvement: Enhances impact resistance.
- Stress Relief: Reduces residual stresses from lost foam casting.
2. Machining
Machining is a post-processing technique used to achieve precise dimensions and tolerances. It involves removing material using cutting tools.
Process:
- Turning: Rotating lost foam casting while a cutting tool removes material.
- Milling: Using rotary cutters to remove material from lost foam casting.
- Drilling: Creating holes in lost foam casting with a drill bit.
Benefits:
- Dimensional Accuracy: Achieves precise dimensions and tight tolerances.
- Surface Finish: Improves the surface finish to meet specifications.
- Customization: Allows for custom features and modifications.
3. Coating and Plating
Applying protective coatings or plating to lost foam casting enhances its surface properties, such as corrosion resistance and aesthetic appeal.
Process:
- Painting: Applying paint to the surface for protection and appearance.
- Powder Coating: Electrostatically applying powdered paint and curing it to form a hard finish.
- Electroplating: Depositing a metal layer on lost foam casting surface using an electric current.
Benefits:
- Corrosion Resistance: Protects against environmental degradation.
- Aesthetic Improvement: Enhances the appearance with various finishes.
- Durability: Increases wear and scratch resistance.
Tables for Surface Finishing and Post-Processing Techniques
Table 1: Surface Finishing Techniques
Technique | Process | Benefits |
---|---|---|
Shot Blasting | High-velocity abrasives impact the surface | Surface cleaning, surface hardening, texture improvement |
Tumbling | Castings tumble with abrasive media in a rotating barrel | Deburring, polishing, consistency |
Grinding and Polishing | Abrasive tools remove material | Precision, smoothness, defect removal |
Table 2: Post-Processing Techniques
Technique | Process | Benefits |
---|---|---|
Heat Treatment | Heating and cooling to alter properties | Strength enhancement, toughness improvement, stress relief |
Machining | Removing material with cutting tools | Dimensional accuracy, surface finish, customization |
Coating and Plating | Applying protective layers | Corrosion resistance, aesthetic improvement, durability |
Lists for Key Techniques and Benefits
Key Surface Finishing Techniques
- Shot Blasting
- Process: High-velocity abrasives impact the surface.
- Benefits: Surface cleaning, surface hardening, texture improvement.
- Tumbling
- Process: Castings tumble with abrasive media in a rotating barrel.
- Benefits: Deburring, polishing, consistency.
- Grinding and Polishing
- Process: Abrasive tools remove material.
- Benefits: Precision, smoothness, defect removal.
Key Post-Processing Techniques
- Heat Treatment
- Process: Heating and cooling to alter properties.
- Benefits: Strength enhancement, toughness improvement, stress relief.
- Machining
- Process: Removing material with cutting tools.
- Benefits: Dimensional accuracy, surface finish, customization.
- Coating and Plating
- Process: Applying protective layers.
- Benefits: Corrosion resistance, aesthetic improvement, durability.
Conclusion
Surface finishing and post-processing techniques are integral to the lost foam casting process, ensuring that castings meet the required quality standards and performance criteria. By employing advanced methods such as shot blasting, tumbling, grinding, heat treatment, machining, and coating, manufacturers can enhance the surface finish, mechanical properties, and overall reliability of lost foam casting. These techniques not only improve the aesthetic and functional qualities of lost foam casting but also contribute to their longevity and performance in various applications. Through continuous innovation and optimization in surface finishing and post-processing, the lost foam casting industry can achieve higher standards of quality and efficiency.