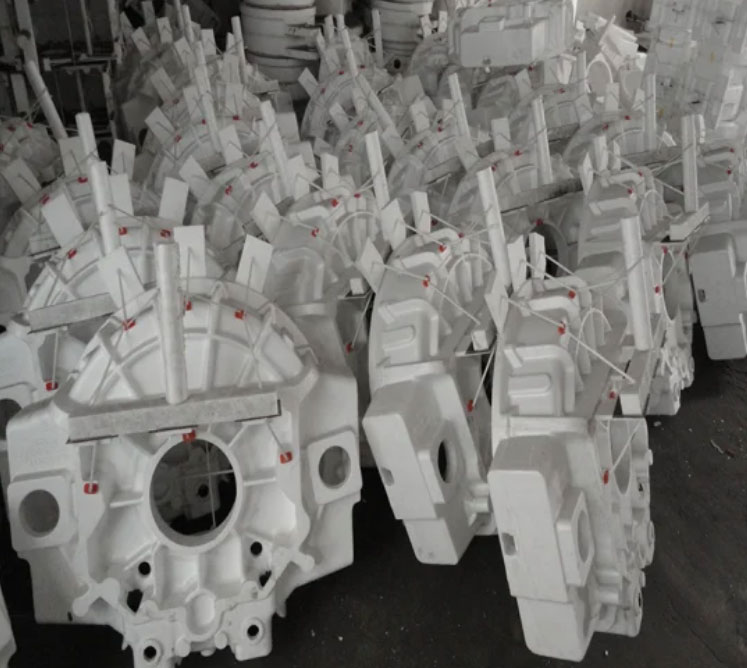
Lost foam casting offers several opportunities to reduce waste and costs in foundries compared to traditional casting methods. By adopting this innovative process, foundries can minimize material usage, decrease post-casting machining requirements, and enhance productivity. Here are some ways in which lost foam casting helps reduce waste and costs:
1. Material Efficiency:
- Lost foam casting produces near net shape castings, which means the final casting requires minimal additional material removal through machining. This results in significant material savings compared to traditional casting methods that require more substantial material allowances for machining.
2. Elimination of Pattern Waste:
- Unlike traditional casting processes that require expendable patterns (e.g., sand, wax, or plastic), lost foam casting uses foam patterns that are entirely vaporized during the casting process. As a result, there is no waste associated with the removal or disposal of pattern materials.
3. Reduced Energy Consumption:
- Lost foam casting typically requires less energy compared to other casting processes that involve heating, melting, and maintaining high temperatures. The elimination of pattern removal and cleaning steps also contributes to energy savings.
4. Simplified Tooling:
- Lost foam casting eliminates the need for complex and costly dies or patterns used in other casting methods, reducing tooling costs. This is especially advantageous for small to medium production runs, as less expensive tooling can be used.
5. Minimized Post-Casting Machining:
- Near net shape castings produced through lost foam casting require less post-casting machining, grinding, or finishing, which reduces the labor and time needed for finishing operations.
6. Improved Productivity:
- Lost foam casting can be a more rapid and efficient process compared to traditional casting methods. The elimination of pattern removal and cleaning steps shortens cycle times and increases overall foundry productivity.
7. Recycling and Reuse:
- The foam patterns used in lost foam casting are expendable and can be easily recycled or reused. This reduces material waste and promotes sustainability in foundry operations.
8. Complexity of Assemblies:
- Lost foam casting allows for the integration of multiple components into a single casting, reducing the need for assembly processes and associated costs.
9. Smoother Surface Finish:
- Lost foam castings typically have a smoother surface finish, reducing the need for additional surface treatments or polishing, thereby lowering post-casting costs.
By embracing lost foam casting, foundries can optimize resource utilization, enhance process efficiency, and achieve cost savings, making it an attractive and competitive option for certain casting applications. As with any casting process, proper process control, skilled craftsmanship, and stringent quality control measures are essential to maximize the benefits of lost foam casting and ensure the production of high-quality castings.