In the spatial structure of buildings, cast steel nodes play an important role, connecting and supporting various components of the structure, bearing various mechanical loads, and ensuring the stability and safety of the building. However, various casting defects may occur during the manufacturing process of cast steel nodes, which pose a potential threat to the performance and reliability of the structure. Therefore, it is crucial to study the casting defects of cast steel joints and their detection techniques, aiming to ensure the quality of building spatial structures.
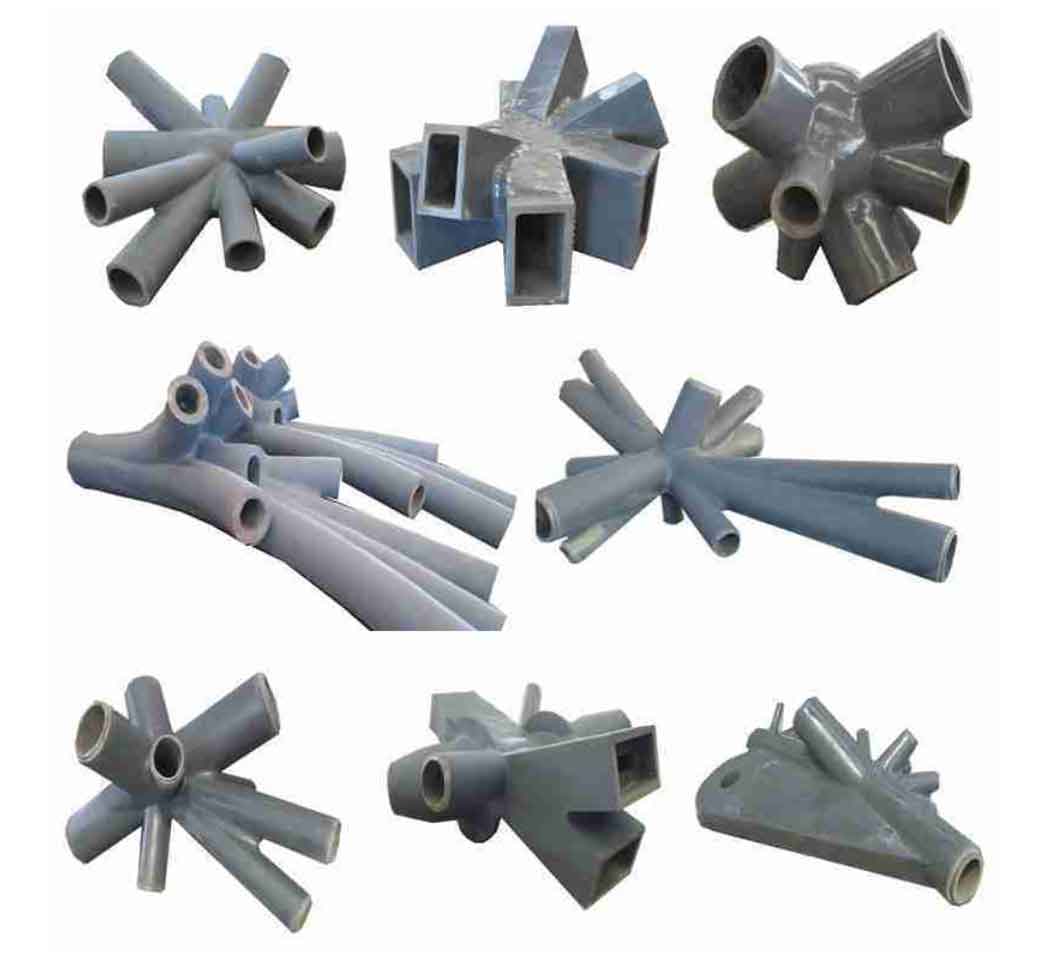
1、 Analysis of Casting Defects in Cast Steel Nodes in Building Space Structures: Pores are gas pores or bubbles formed during the casting process, which may exist inside the cast steel nodes. These small pores may become stress concentration points when the nodes bear loads, leading to a decrease in the strength and toughness of the nodes. The formation of pores is usually related to various factors, including the gas content of raw materials, pouring temperature, and pressure. Therefore, it is necessary to conduct in-depth research on the formation mechanism of stomata.
Inclusion refers to the presence of non-metallic substances such as sand, impurities, or other external substances in castings. Inclusions may form inside or on the surface of nodes, posing a threat to their strength and toughness. These inclusions may become the starting point of cracks, leading to node damage. The generation of inclusions is closely related to the quality and processing of raw materials, so careful control and management are necessary.
Hot cracks are caused by uneven or rapid cooling, which can lead to internal or surface cracking of nodes. These cracks can affect the strength and durability of nodes, posing a potential threat to the quality of the structure. Therefore, it is necessary to control the temperature gradient during the casting process to reduce the occurrence of hot cracks.
2、 The casting defect detection technology for cast steel joints in building spatial structures is crucial for the safety of the entire structure, as the quality and reliability of cast steel joints are crucial. To ensure that there are no casting defects in the nodes, advanced casting defect detection techniques need to be adopted.
X-ray inspection utilizes the strong penetration ability of X-rays to examine casting defects inside the casting material, such as pores, inclusions, and cracks. X-ray inspection can provide high-resolution images to display subtle casting defects inside materials, helping engineers determine the location and properties of casting defects. This method is a non-invasive detection technique that does not require contact with the object being tested, so it will not have any impact on cast steel nodes.
Ultrasonic testing is the use of the propagation characteristics of ultrasonic waves to detect casting defects inside materials by emitting and receiving ultrasonic waves. Ultrasonic waves can penetrate materials, and when encountering casting defects, some energy will be reflected or absorbed, forming echoes. By analyzing the characteristics of echoes, the location, size, and properties of casting defects can be determined. This method can be used for on-site inspection of cast steel joints, and potential casting defects can be quickly and accurately discovered. In addition, ultrasonic testing can detect different types of casting defects, including porosity, inclusions, and cracks.
Magnetic particle testing is a method used to detect surface casting defects in casting materials, such as cracks, inclusions, and other surface casting defects. The principle of magnetic particle testing is to coat magnetic powder on the surface being tested and apply a magnetic field. When magnetic powder enters casting defects or cracks, it forms a pile up of magnetic powder, which can be observed and analyzed by visual or camera equipment for the position and shape of casting defects. This method is very suitable for on-site inspection of cast steel joints, which can quickly detect surface casting defects and improve work efficiency.
3、 Prevention and control measures for casting defects in steel joints in architectural spatial structures
In construction engineering, cast steel nodes are an important part of the connection and support structure, and their quality and reliability are directly related to the safety of the entire building. To ensure that cast steel joints are not affected by casting defects, prevention and control measures are crucial.
Firstly, there is no doubt that controlling from the source is the most effective preventive measure. Therefore, choosing high-quality raw materials is crucial. Engineers and manufacturers should carefully select qualified steel suppliers to ensure that raw materials comply with relevant standards and specifications. The quality of raw materials plays a decisive role in the quality of the final product. In addition, attention should be paid to the impurities and gas content in the raw materials, as they may lead to the formation of pores and inclusions.
Secondly, optimizing the casting process is also crucial for controlling casting defects. Proper temperature and pressure control is crucial in preventing porosity and hot cracking during the casting process. Appropriate pouring temperature and speed can reduce gas solubility and reduce the risk of porosity. In addition, appropriate pressure can ensure the uniformity of the melt filling mold and reduce the generation of cracks. Engineers need to closely monitor each production process to ensure that all steps are carried out according to best practices.
Once again, taking appropriate control measures during the casting process can reduce the risk of inclusions, including controlling the preparation and treatment of the mold to ensure a smooth surface and reduce the introduction of pollutants and impurities. In addition, using appropriate pouring techniques, such as vacuum pouring or gas shielded pouring, can reduce the formation of inclusions.
Finally, quality control and inspection are crucial steps in preventing casting defects. After casting is completed, non-destructive testing techniques such as X-ray testing, ultrasonic testing, and magnetic particle testing should be used to inspect the quality of cast steel joints. These techniques can quickly detect potential casting defects and ensure that cast steel joints meet design standards. In addition, establishing a sound quality management system, including the retention and tracking of production records, as well as quality review and certification, is also essential.
In summary, the research on casting defects and detection of cast steel joints in building spatial structures is a complex and important task, which is related to the safety and stability of the structure. By conducting in-depth research on the casting defects and detection techniques of cast steel joints, we can better understand this problem and take appropriate measures to prevent and solve it. In the future, with the continuous development of science and technology, detection technology will continue to be optimized, which will better ensure the safety of building structures.