1 Preamble
The thickness of the middle partition of the double-channel vortex shell is 2mm, and the cold insulation defect is easy to occur during the casting process. Through the optimization and improvement of the casting process, the problem of cold insulation in the double flow channel is solved. Cold separation is mainly caused by low temperature, which often occurs at the intersection of molten steel, but the reason for the occurrence of cold separation described in this article is different, although the molten steel does not intersect, but it also occurs. The main reason is due to the influence of the charging force during the filling process The temperature of the molten steel is low and the fluidity is poor, which causes the cold molten steel to be in a fluctuating state, and the cold molten steel cannot be discharged at the same time, resulting in the phenomenon of cold separation on the skin. In view of the above problems, this paper numerical simulation of the process is carried out, and the original process is optimized according to the simulation results, and improvement measures are formulated Shi has achieved good results.
2 Product Introduction
1) Vortex shell material: 1.4837+Nb, its three-dimensional structure is shown in Figure 1, the dimensions are 155mm× 125mm×125mm, and the blank weight is 3.2kg.
2) The thickness of the double runner spacer is 2mm, and the length is long, which is not easy to form during the casting process.
3) The partition is prone to cold isolation in the production process, and the proportion reaches 100%.

Fig.1. Vortex shell parts
3 Casting process design
The original casting process is shown in Figure 2.
1) The blank production adopts the cold core shell molding line, 4 pieces per mold.
2) The pouring weight of each box is 40kg, and the process yield is 32%.
3) The molten steel is melted by medium frequency induction electric furnace and poured by automatic pouring machine, the pouring temperature is 1620~1630 °C, and the pouring time of each box is 6~8s.
4) The cross-sectional area ratio of the gating system is ΣF inside: ΣF horizontal: ΣF straight = 1.4: 1.2: 1.
5) The minimum pouring area is 1250mm².
6) Adopt a bottom-injection gating system to reduce turbulence.
7) Optimize smelting to obtain high-quality molten steel, reduce molten steel oxidation, add trace elements, refine grains, and purify molten steel.
8) The inner core is stained with paint, which reduces the surface roughness value of the casting, and also increases the fluidity, which plays a positive role in reducing the cold separation.
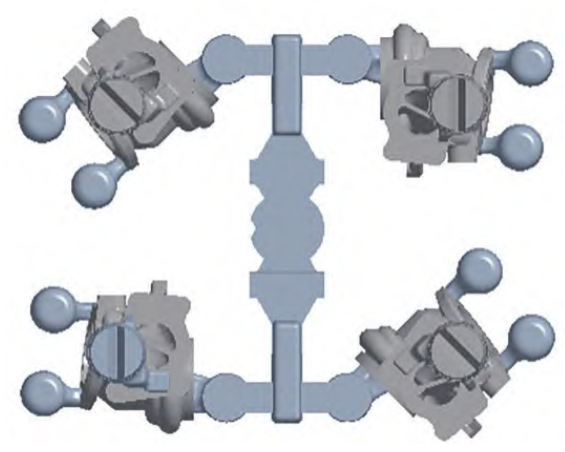
Fig.2. Original casting process
4 Casting process simulation
Procast simulation software is used to numerically simulate the process to determine whether there will be casting defects.
1) The simulated material is set as: 1.4837+Nb, and the chemical composition is shown in Table 1.
2) The pouring temperature is set to 1600°C.
3) The pouring time is set to 6s.
4) The heat transfer coefficient is set to 500W/(m2•K).
5) Calculation method: The coupling calculation results of temperature field and flow field are shown in the figure 3 Figure 4.
Table 1 Chemical composition (mass fraction) of vortex shell castings (%)

The simulation results show that the shrinkage porosity is solved through the process simulation, but the temperature drop of the middle insulation is too large, the fluidity of the molten steel is poor, and the phenomenon of cold isolation is easy to occur.
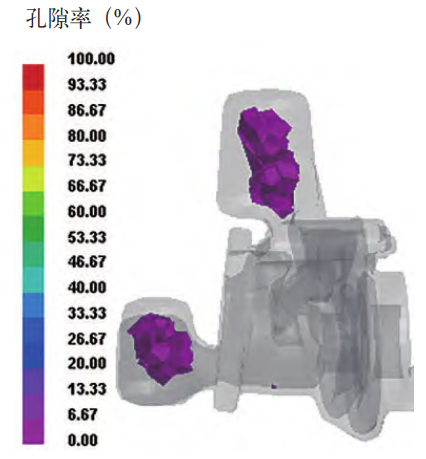
Fig.3 The results of 3% porosity are displayed
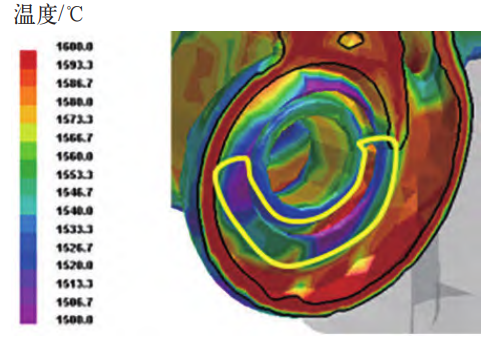
Fig.4 The septum temperature is displayed at 70% of the filling time
5 Verification results and problem analysis
Fig. 5 and Fig. 6 show the appearance and morphology of the vortex shell producing cold separation lines and cold separation, and the product defect detection results are shown in Table 2.

Fig.5. Cold barrier defects
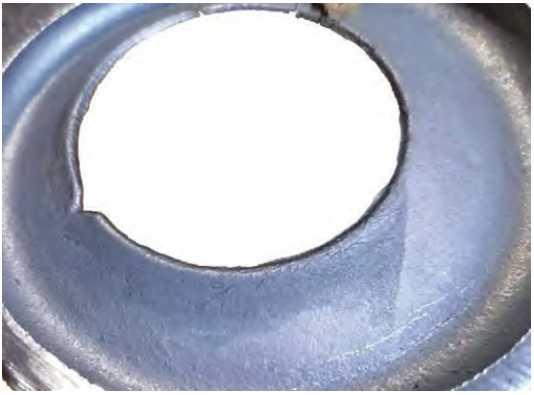
Fig.6. Cold insulation defects
Table 2 Product defect detection results
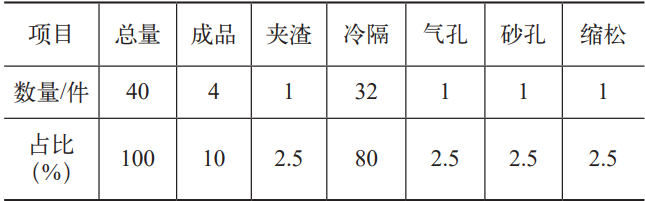
1) From the results of product defect detection, it can be seen that the appearance of cold separation and cold separation lines in the middle septum is the main cause of rejection.
2) According to the verification results and combined with CAE analysis, the temperature of the septum is too fast to reach 1500°C, although it is not lower than the liquidus line, but the fluidity of the molten steel is greatly reduced, because the whole casting is still in the filling state, Therefore, the molten steel is still unstable, although there is no molten steel intersection in the septum, but it is easy to appear cold separator or cold separator lines due to the influence of flow.
6 Improvement Measures
1) Open a 0.2mm overflow groove at the middle spacer position, and discharge the cold steel liquid and gas during the pouring process, but after the actual verification, the effect is not very good, although the proportion of cold separation has been reduced, it is still as high as 50% (see table3), and it makes it difficult to clean up.
Table 3 Detection results of casting defects after opening the overflow groove
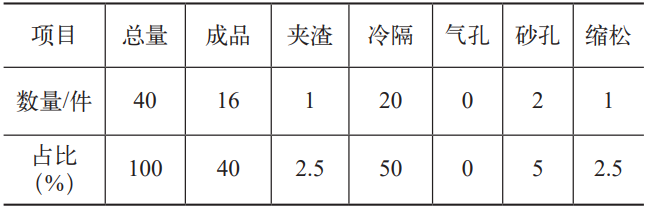
2) Adjust the position of the inlet of the molten steel to ensure that the filling of the middle space is smoother, increase the temperature of the middle space during the pouring process, and avoid cooling down too quickly. Adjusting the position of the inlet (see Fig. 7), the numerical simulation results are shown in Fig. 8, from which it can be seen that the temperature drop in the middle insulation is reduced.
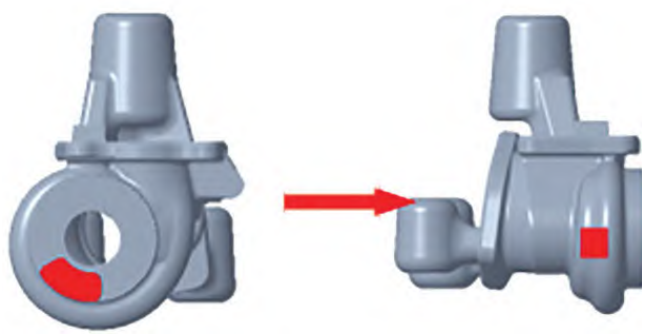
Fig.7. Adjust the water inlet display
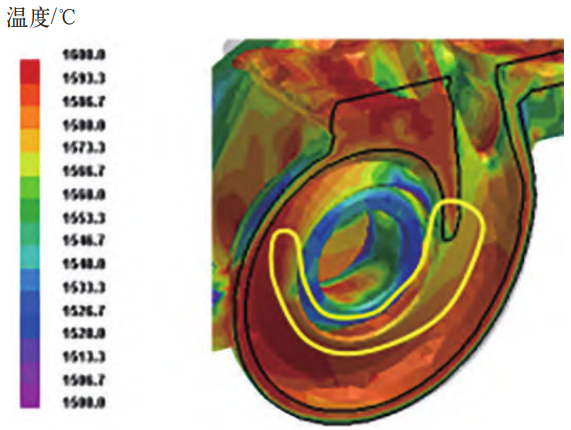
Fig.8. The septum temperature is displayed at 70% of the filling type
7 Improvements
After the improvement and optimization of the vortex shell casting process, the defect detection results of the castings produced are shown in Table 4.
Table 4 Detection results of casting defects after process improvement
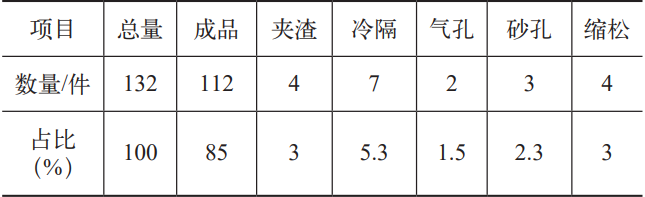
It can be seen from Table 4 that the cold insulation waste products are greatly reduced compared with the original process, and the problem is basically solved.
8 Concluding remarks
1) For the small parts of the vortex shell, the water inlet position should be used as much as possible to avoid the intersection of molten steel, resulting in defects such as cold isolation of castings, secondary oxidation slag inclusion and coil gas.
2) The cold barrier does not necessarily appear at the intersection of the molten steel or the molten steel flow head, and the local temperature cools down too much during the pouring process, which is affected by the dynamic pressure during the pouring process, and the cold isolation or cold separation pattern will also appear. For thin-walled small parts, the pouring temperature drop of different positions of a single casting is generally controlled within 50 °C during process design.
3) By using Procast software for simulation, the position of the cold partition can be judged according to the display of the simulated filling temperature change, and the casting process can be reasonably designed. In the process of work, it is necessary to fully compare the simulation results and reality
Verify and compare, find out the differences, summarize experience, reduce the number of trial production, and reduce costs.