e fittings. It includes an analysis of welding processes, metallurgical examinations, thermodynamic calculations, the impact of cold deformation on mechanical properties, and corrosion analysis. The aim is to optimize the properties of the steel for better performance in boiler applications.
1. Introduction
Boiler pipe fittings play a crucial role in the efficient operation of boilers. Heat-resistant austenitic steel is widely used in their precision casting due to its excellent properties such as corrosion resistance and good creep resistance. With the increasing demand for energy efficiency and the reduction of emissions, it is essential to study and improve the performance of this steel in boiler applications. This article presents a comprehensive study on the heat-resistant austenitic steel used for precision casting of boiler pipe fittings.
2. Experimental Methods
2.1 Welding Process
Two types of typical welded joints were selected for analysis: the supercritical boiler heating surface component diameter pipe SA -213S30432 and the super-supercritical boiler heating surface component diameter pipe SA -213T91 + SA -213TP347H. Tungsten inert gas arc welding (TIG) was used for vertical butt welding. Different welding parameters were set for each joint type. For SA -213S30432, the preheating temperature was ≥5 °C, the voltage was 13 – 14 V, the number of welding layers was 3 layers, the current was 190 – 200 A, and the interlayer temperature was 50 – 230 °C. For SA -213T91 + SA -213TP347H, the preheating temperature was ≥5 °C, the voltage was 13 – 16 V, the number of welding layers was 3 layers, the current was 185 – 210 A, and the interlayer temperature was 160 – 280 °C. After welding, hardness tests, transverse bending tests, tensile tests, and room-temperature impact toughness tests were carried out on the welded joints.
2.2 Material Preparation
The heat-resistant austenitic steel used for precision casting of boiler pipe fittings had a chemical composition of Fe – 15%Cr – 25%Ni – 3.5%Al – 0.6%Nb – 2%Mo – 0.02%C (by mass). It was melted in a vacuum induction furnace, and the resulting ingot had a height of 250 mm and a diameter of 100 mm. The forging ratio was set to 3:1, and a steel ingot with dimensions of 60 mm × 50 mm × 80 mm was cast. After 40 min of solution treatment at 1200 °C, a solution-treated sample was obtained by water quenching. The alloy composition was detected using an oxygen-nitrogen-hydrogen analyzer (EMGA – 830) and an X-ray fluorescence spectrometer.
2.3 Other Tests
To study the internal quality of the weld, a fracture inspection was carried out according to the boiler pressure element weld fracture inspection method. A 1/3T groove was machined during the preparation of the pipe butt joint fracture to ensure the integrity of the fracture sample section. In addition, to reduce processing costs, magnesium was appropriately added to the steel liquid to increase the absorption rate of magnesium.
3. Results and Discussion
3.1 Metallurgical Examination
3.1.1 Weld Defects
Metallurgical examination of the welded joints was carried out using an optical microscope. Layered slag inclusions were found between the weld layers. This was due to the fast welding speed with a large current, resulting in a long residence time of the weld metal at high temperatures. After leaving the gas protection area of the argon arc welding gun, the weld metal was easily oxidized and slag inclusions occurred. In addition, for small-diameter pipes with a large curvature of the groove surface, the molten weld metal was prone to flow down, resulting in incomplete fusion between the weld layers. To avoid these problems, it is necessary to ensure that the heating end of the welding wire is in the protection gas during tungsten inert gas arc welding and to avoid oxidation of the wire end due to improper operation during fast welding with a large current.
3.1.2 Grain Structure
Both SA -213TP347H and SA -213S30432 are austenitic stainless steels. To avoid 不良现象 such as grain growth in the heat-affected zone, welding hot cracks, and carbide precipitation, a relatively low interlayer temperature can be appropriately controlled to enhance the corrosion resistance and plasticity-toughness of the welded joint. The alloy matrix was a single-phase austenite with a large number of twins and sufficient solid solution. The residual strain of the AFA – 0 experimental steel was 0.081%, the dislocation density was 1.603 × 1014 %, and the average grain diameter under an optical microscope was 173 μm. The residual strain of the AFA – 20% experimental steel was 0.171%, the dislocation density was 6.571 × 1014 %, and the S grain boundary was straight after solid solution treatment without any precipitates. The residual strain of the AFA – 50% experimental steel was 0.216%, and the dislocation density was 10.363 × 1014 %.
3.2 Thermodynamic Calculations
The thermodynamic values of the mass fractions of each component of the AFA15 – 25 heat-resistant austenitic steel were analyzed. At 600 – 1200 °C, the AFA15 – 25 heat-resistant austenitic steel had a single-phase austenite matrix, and the precipitated phases were NiAl, σ phase, M23C6, and MC carbides. The distribution histogram of the σ phase at 650 °C showed that the mass fraction of the σ phase was 10.88%, the mass fraction of austenite was 82%, the mass fraction of NiAl was 6.64%, and the mass fraction of MC was 0.19%.
3.3 Impact of Cold Deformation on Mechanical Properties
3.3.1 At Room Temperature
At 26 °C, as the cold deformation amount increased, the yield strength and tensile strength of the heat-resistant austenitic steel increased, while the elongation after fracture decreased. For example, the tensile strength of AFA – 0 was 798 MPa, the yield and the difference in elongation after fracture was not obvious. This was mainly because the NiAl phase underwent a ductile-brittle transition, which had a good strengthening effect at room temperature but was less effective at high temperatures. However, the operation process could appropriately increase the plasticity of the material.
3.4 Corrosion Analysis
The corrosion of the material surface was studied at different temperatures. The test used a BTF – 1200C – Ⅲ type tubular heating furnace, and the experimental temperatures were set to 650 °C, 675 °C, 700 °C, and 725 °C. Nitrogen was introduced into the furnace at a rate lower than 5 °C/min, and a mixed gas was introduced into the furnace tube. The injection pump was opened, the gas cylinder valve was closed, and nitrogen was introduced. Samples were then taken. The liquid water flow rate of the heating furnace was 0.8036 μL/min, and the total flow rate of the mixed gas was 40.0 mL/min, with a volume fraction of 77.0% N2 + 15% CO2 + 3.75% O2 + 5.0% H2O(g) + 0.32% SO2 and a pressure of 105 kPa. The results showed that the degree of oxidation corrosion of the material was proportional to the temperature. The S31042 material had the strongest oxidation and corrosion resistance, and the S31035 and C – HRA – 5 materials had approximately the same oxidation and corrosion resistance.
4. Conclusions
In this study, at 1200 °C, after 40 min of solution treatment, a solution-treated sample was obtained by water quenching. When the cold deformation amount was 20%, the yield strength of the experimental steel could be appropriately increased. When the cold deformation amount increased to 50%, the strength increase was not obvious, but the plasticity was easily reduced. Appropriate control of the interlayer temperature was beneficial to enhancing the corrosion resistance and plasticity-toughness of the welded joint and avoiding 不良现象 such as incomplete fusion of the weld and slag inclusions. At 650 °C, the mass fraction of the σ phase was 10.88%, the mass fraction of austenite was 82%, the mass fraction of NiAl was 6.64%, and the mass fraction of MC was 0.19%. After the deformation amount increased from 20% to 50%, the tensile strength was 1131 MPa, and the yield strength increased while the elongation after fracture decreased. Overall, the optimal cold deformation condition was 20%, at which the heat-resistant austenitic steel had relatively good plasticity and high strength, meeting the process requirements for the precision casting of boiler pipe fittings.
5. Future Research Directions
Although this study has provided valuable insights into the heat-resistant austenitic steel for precision casting of boiler pipe fittings, there are still several areas that require further investigation.
5.1 Optimization of Welding Parameters
The welding parameters used in this study were based on existing experience and standards. However, there may be room for further optimization to improve the quality of the welded joints. Future research could focus on exploring different combinations of welding parameters, such as varying the preheating temperature, voltage, current, and interlayer temperature, to determine the optimal settings for different types of boiler pipe fittings and welding materials. This could involve conducting a series of experiments with different parameter combinations and evaluating the resulting welded joints based on hardness, tensile strength, impact toughness, and corrosion resistance.
5.2 Study of Microstructure Evolution during Service
The microstructure of the heat-resistant austenitic steel can change during the service life of the boiler pipe fittings due to factors such as temperature, pressure, and corrosive environments. Understanding these changes is crucial for predicting the long-term performance and reliability of the fittings. Future research could involve in-situ monitoring of the microstructure evolution using advanced techniques such as electron microscopy and X-ray diffraction. This would allow for a detailed understanding of how the microstructure changes over time and how these changes affect the mechanical and corrosion properties of the steel.
5.3 Development of New Heat-Resistant Austenitic Steels
With the increasing demand for higher efficiency and better performance in boiler applications, there is a need to develop new heat-resistant austenitic steels with improved properties. This could involve exploring new alloy compositions and heat treatment processes to achieve higher strength, better corrosion resistance, and enhanced creep resistance. Research could focus on incorporating elements such as rare earth metals or advanced ceramic particles into the steel matrix to improve its properties. Additionally, the development of new heat treatment processes could be explored to optimize the microstructure and mechanical properties of the steel.
5.4 Investigation of the Interaction between Different Phases
The heat-resistant austenitic steel contains multiple phases such as austenite, NiAl, σ phase, M23C6, and MC carbides. The interaction between these phases plays a crucial role in determining the mechanical and corrosion properties of the steel. Future research could focus on investigating the nature of these interactions in more detail. This could involve using theoretical models and computational simulations to predict how the phases interact and how these interactions affect the overall performance of the steel. Additionally, experimental techniques such as transmission electron microscopy and energy-dispersive X-ray spectroscopy could be used to observe and analyze the phase interactions directly.
6. Summary
This article has presented a comprehensive study on the heat-resistant austenitic steel for precision casting of boiler pipe fittings. The welding process, metallurgical examination, thermodynamic calculations, impact of cold deformation on mechanical properties, and corrosion analysis were discussed in detail. The results showed that appropriate control of welding parameters and cold deformation amount could optimize the properties of the steel for better performance in boiler applications. Future research directions were also proposed to further improve the understanding and performance of heat-resistant austenitic steels in boiler pipe fittings.
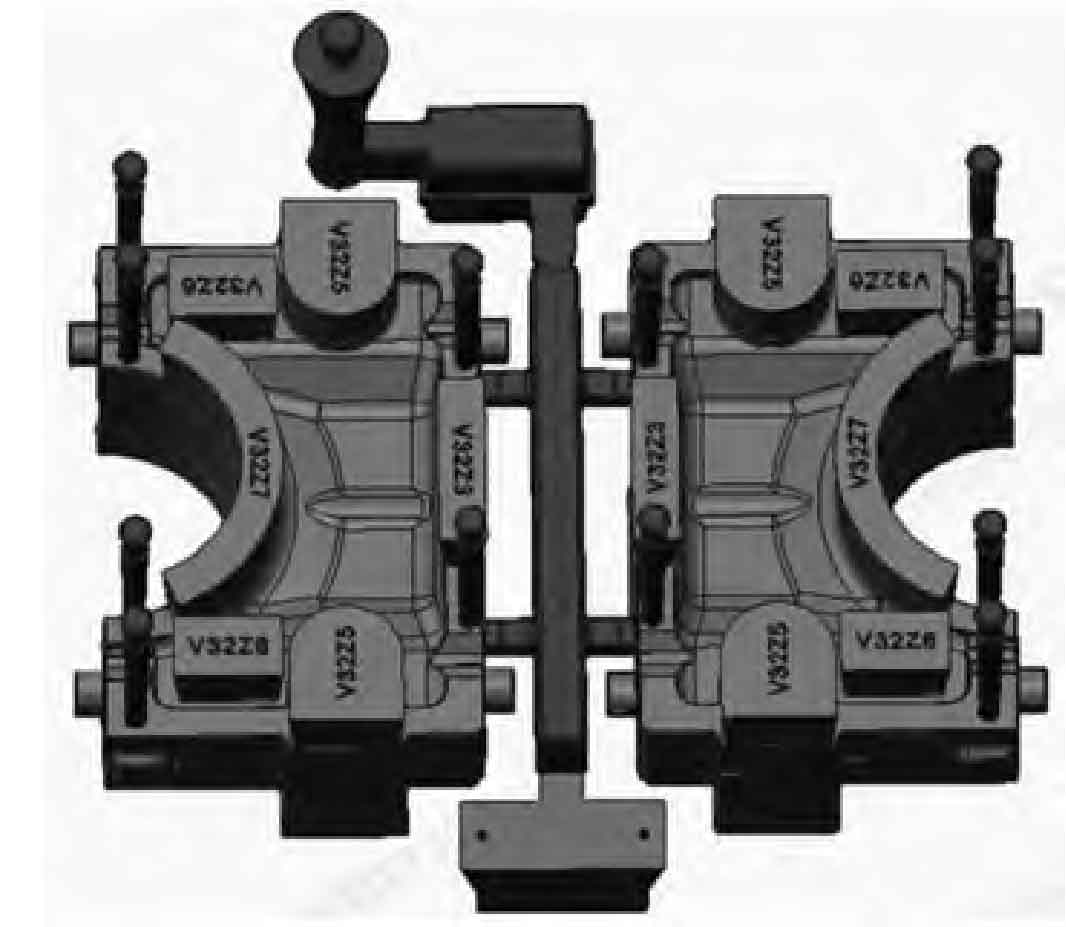