Lost foam casting, known for its ability to create complex and precise metal parts, is evolving with the integration of digital technologies. These advancements aim to enhance real-time quality control, ensuring higher efficiency, accuracy, and consistency in production. This article explores the integration of digital technologies in lost foam casting and their impact on real-time quality control.
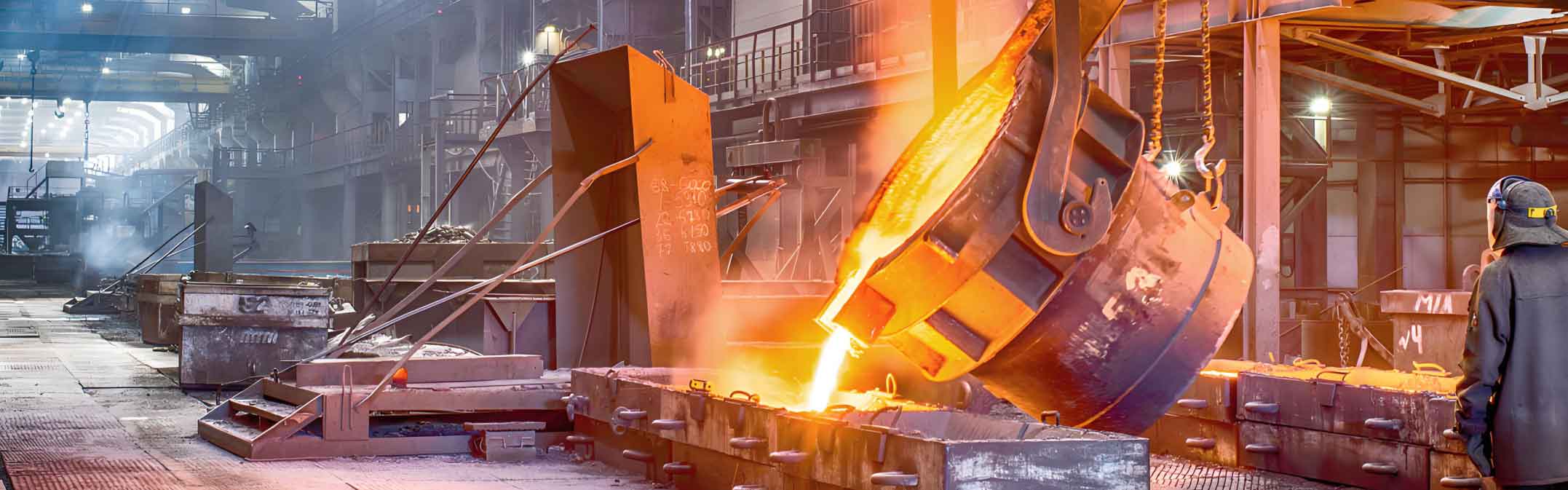
Introduction
Lost foam casting (LFC) involves using a foam pattern, coated with refractory material, which is then surrounded by sand. When molten metal is poured into the mold, the foam vaporizes, leaving a precise metal casting. Integrating digital technologies into this process can significantly improve quality control, reducing defects and increasing productivity.
Digital Technologies in Lost Foam Casting
Several digital technologies are being integrated into lost foam casting to enhance real-time quality control. These include:
- 3D Scanning and Imaging
- Internet of Things (IoT)
- Artificial Intelligence (AI) and Machine Learning (ML)
- Real-Time Data Analytics
- Advanced Sensor Technologies
3D Scanning and Imaging
3D scanning and imaging technologies are used to create detailed digital models of the foam patterns and final castings. These models are compared to the original CAD designs to identify any deviations or defects.
Benefits:
- High precision in pattern and mold inspection
- Early detection of defects and deviations
- Enhanced accuracy in quality control
Internet of Things (IoT)
IoT devices are employed to monitor various parameters in real-time, such as temperature, pressure, and humidity during the casting process. These devices communicate with a central system to provide continuous data streams.
Benefits:
- Real-time monitoring and control of casting conditions
- Immediate identification of anomalies
- Improved process consistency
Artificial Intelligence (AI) and Machine Learning (ML)
AI and ML algorithms analyze the data collected from IoT devices and other sources to predict potential defects and optimize the casting process.
Benefits:
- Predictive maintenance and defect prevention
- Optimization of casting parameters for better quality
- Automated decision-making for process adjustments
Real-Time Data Analytics
Real-time data analytics systems process the vast amount of data generated during the casting process to provide actionable insights for quality control.
Benefits:
- Instant feedback on process performance
- Data-driven decision making
- Enhanced process transparency and traceability
Advanced Sensor Technologies
Advanced sensors are used to measure critical parameters with high accuracy and reliability. These sensors provide real-time feedback to the control systems.
Benefits:
- High accuracy in parameter measurement
- Early detection of process variations
- Improved control over the casting process
Comparative Table of Digital Technologies in Lost Foam Casting
Technology | Application Area | Benefits |
---|---|---|
3D Scanning and Imaging | Pattern and mold inspection | High precision, early defect detection |
Internet of Things (IoT) | Real-time monitoring of casting conditions | Immediate anomaly detection, improved consistency |
AI and ML | Data analysis and process optimization | Predictive maintenance, automated decision-making |
Real-Time Data Analytics | Process performance analysis | Instant feedback, data-driven decision making |
Advanced Sensor Technologies | Measurement of critical parameters | High accuracy, early process variation detection |
Detailed Analysis
- 3D Scanning and Imaging3D scanning and imaging technologies create digital replicas of foam patterns and finished castings. These digital models can be analyzed for dimensional accuracy and surface quality, ensuring the patterns and castings meet design specifications. This technology allows for early detection of defects, reducing the need for costly rework.
- Internet of Things (IoT)IoT devices embedded in the casting environment collect real-time data on various parameters. This data is transmitted to a central system for continuous monitoring. By tracking parameters such as temperature and pressure, IoT devices help maintain optimal casting conditions, thereby improving the quality and consistency of the castings.
- Artificial Intelligence (AI) and Machine Learning (ML)AI and ML algorithms process data from IoT devices and other sources to identify patterns and predict potential issues. These technologies enable predictive maintenance, where potential defects are identified before they occur, and the casting process is adjusted in real-time to prevent them. This proactive approach ensures higher quality and reduces downtime.
- Real-Time Data AnalyticsReal-time data analytics systems provide immediate insights into the casting process. These systems analyze data as it is collected, offering real-time feedback on process performance. This allows for quick adjustments to the casting parameters, ensuring optimal conditions are maintained throughout the process.
- Advanced Sensor TechnologiesAdvanced sensors provide accurate and reliable measurements of critical parameters such as temperature, pressure, and humidity. These sensors are crucial for maintaining control over the casting process and ensuring that the conditions remain within the specified range. Early detection of deviations helps prevent defects and ensures the quality of the castings.
Practical Applications
- Automotive Industry
- Real-time quality control in the production of engine blocks, cylinder heads, and other complex components.
- Improved consistency and reduced defect rates in high-volume production environments.
- Aerospace Industry
- Enhanced precision in the manufacturing of turbine blades, structural components, and other critical parts.
- Increased reliability and safety of aerospace components through improved quality control.
- Industrial Machinery
- Real-time monitoring and control in the production of large, complex machine parts.
- Reduced downtime and maintenance costs through predictive maintenance.
- Medical Devices
- High precision and quality control in the production of surgical instruments, implants, and other medical devices.
- Improved patient safety and device reliability through enhanced quality assurance.
Future Trends and Research
- Integration of AI and ML with IoT
- Development of more advanced AI and ML algorithms that can process larger datasets and provide more accurate predictions.
- Enhanced integration of IoT devices with AI systems for fully automated quality control.
- Advanced 3D Scanning Technologies
- Improvement in 3D scanning technologies to provide higher resolution and faster scanning speeds.
- Integration of 3D scanning with real-time data analytics for instant feedback on pattern and casting quality.
- Sustainability and Efficiency
- Development of more energy-efficient IoT devices and sensors to reduce the environmental impact of the casting process.
- Research into sustainable materials for foam patterns and refractory coatings.
Conclusion
The integration of digital technologies in lost foam casting offers significant improvements in real-time quality control. Technologies such as 3D scanning, IoT, AI, ML, real-time data analytics, and advanced sensors enhance the precision, efficiency, and consistency of the casting process. By adopting these technologies, manufacturers can achieve higher quality castings, reduce defects, and increase productivity, positioning themselves for success in a competitive market.