Austenitic steel is widely used in precision casting of boiler pipe fittings. has shown strong application value, in order to reduce CO2 Wait for gas To reduce the emission of carbon dioxide, we should strengthen the research on casting technology and strengthen the Effective development and utilization of fossil energy. In the casting process, with With the increase of supercritical water temperature, high temperature conditions above 650-700℃ The research value of the high-temperature austenitic steel structure materials is relatively high. value, heat-resistant austenitic steel has good corrosion resistance and creep resistance Therefore, in the current casting process, research on the high temperature strength and corrosion resistance of austenitic steel is continuously strengthened. There are research results In high-temperature ultra-fine precipitation strengthened steel, proper cold processing is beneficial to Promote the precipitation of nanometer-sized MC carbide and solid solution treatment of AFA steel After that, cold rolling and annealing can promote the precipitation of Laves phase. precipitation. This article analyzes the heat-resistant austenitic steel for precision casting boiler tube fittings The relevant performance of the is studied and discussed.
Process research
Two typical welding joints were selected for analysis, namely ultra Critical boiler heating surface component radial tube SA-213S30432, ultra-supercritical The heating surface components of the boiler, including SA-213T91+SA-213TP347H, are welded by argon tungsten arc welding in vertical butt welding, using two types of welding Parameters: SA-213S30432 preheating temperature ≥5℃, voltage 13~ 14V, 3 layers of welding, current 190-200A, interlayer temperature 50- 230℃; SA-213T91+SA-213TP347H, preheating temperature ≥5 ℃, voltage 13-16V, welding layer number 3, current 185-210A, The temperature between layers is 160-280℃. Carry out hardness test on the welded joint. Horizontal bending, tensile test, room temperature impact toughness test.
In order to study the internal quality of welds, according to the boiler pressure components The welding fracture inspection method is used to carry out fracture inspection to ensure that no cracks occur. There are cracks and incomplete fusion in the pipe butt joint fracture preparation. The depth of the 1/3T groove ensures the integrity of the fracture surface of the fractured sample. The heat-resistant austenitic steel used for dense casting boiler pipe fittings is Fe-15%Cr. 25%Ni3.5%Al-0.6%Nb-2%Mo-0.02%C (mass fraction number), smelted in a vacuum induction furnace, and the resulting ingot height 250mm, diameter 100mm, combined with the actual use of boiler pipe fittings The demand, forging ratio is set to 3:1, and the casting length, width, and height are 60mm×50 mm x 80mm ingot. At 1200℃, the alloy passes through 40 After the min solution treatment, water quenching is performed to obtain a solid solution sample. Carry out thermodynamic calculations using JMatPro software. Use oxygen, nitrogen, and hydrogen analysis The alloy composition was detected using an EMGA-830 X-ray fluorescence spectrometer.
Analysis of results
Study the appearance of fracture samples and ensure their effectiveness in welding operations Avoid the occurrence of poor phenomena such as lack of fusion and slag inclusion in the weld, otherwise Strength reduction of tensile test samples and bending test samples are prone to occur in the process of production. Risk of fracture, and possible weld layer defects in metallographic examination The phenomenon of intercalated slag in the form of sheets.
Metallographic examination of welded joints using optical microscopy, The interlayer sheet-like slag was found, which was visible through the weld formation, and high-current welding was used. The welding speed is fast, and the high temperature residence time of the weld metal during welding operation Longer, after leaving the gas protection area of the argon arc welding gun, it is easy to Air contact, oxidation phenomenon, slag inclusion is prone to occur in weld deposition welding. Small-diameter pipes have a groove surface with a large curvature, which can easily cause fusion defects. The weld metal melts and flows down, resulting in a lack of fusion between the layers of the weld. During the welding process of argon tungsten arc welding, it should be ensured that the heated end of the welding wire is kept The purpose of shielding gas is to prevent hot end oxidation from occurring in the weld Metal pollution phenomenon. During high-current rapid welding, pay attention to avoid The phenomenon of oxidation of the end of the welding wire caused by improper operation, in order to prevent welding The appearance of slag in the seam. The width of the heat affected zone will be affected to some extent. Affect the performance of welded joints. The welding heat affected zone refers to the area of material The area where mechanical properties and metallographic structure change due to heating. Close to the welding The overheated and coarse crystalline zones of the joint are more obvious. Metallographic examination shows that The width of the coarse grain zone of the welded joint has increased.
In order to avoid the expansion of grain in the heat affected zone and the occurrence of welding heat Poor phenomena such as cracks and carbide precipitation can be appropriately controlled to a low level The interlayer temperature is controlled at 100℃ to enhance the corrosion resistance and toughness of the welded joint. The alloy matrix is a single-phase austenite with a large amount of twin crystals, which are solid solution The residual strain of the AFA-0 experimental steel is 0.081%, Dislocation density 1.603×1014%, average grain size under optical microscope Diameter 173μm; AFA-20% experimental steel residual strain 0.171%, position The density error is 6.571×1014%, and the S grain boundary is straight after solution treatment, without See the precipitate; the residual strain of AFA-50% experimental steel is 0.216%, and the position The density error is 10.363×1014%.
Thermodynamic Calculation of Heat-resistant Austenitic Steel
Analyze the composition and quality of AFA15-25 heat-resistant austenitic steel The thermodynamic numerical value of the quantity fraction, under the temperature environment of 600-1200℃, The AFA15-25 heat-resistant austenitic steel has a single-phase austenite matrix, The precipitated phases are NiAl, σ phase, M23 C6 , MC carbide. The histogram of the phase distribution at 650°C is shown, with the mass fraction of σ phase 10.88%, with 82% austenite and 18% NiAl The number is 6.64%, and the MC mass fraction is 0.19%. 600-1200 The thermodynamic calculation and phase distribution at 100℃ are shown in the figure.
Influence of Cold Deformation on the Mechanical Properties of Heat-resistant Austenitic Steel
When the amount of cold deformation increases, the heat-resistant austenitic steel The strength and tensile strength of the fabric are correspondingly improved, while the elongation after breakage is slightly reduced Low. At this time, the tensile strength of AFA-0 is 798MPa, and the yield strength 405MPa, elongation after fracture 50%; compared with AFA-0, The tensile strength of AFA-20% is relatively higher. When the deformation increases from 20%, After being increased to 50%, the tensile strength is 1131MPa, and the yield strength 889MPa, which is slightly higher than that of AFA-20%, but the tensile strength after fracture The elongation rate is correspondingly reduced. After proper cold deformation treatment, the strength The degree of improvement is significant, indicating the presence of NiAl phase and dislocation after cold deformation the interaction.
Comprehensive performance of strength improvement when increasing deformation Not obvious enough, but it can reduce the plasticity of the material to a certain extent. Under high temperature conditions, the tensile strength and yield strength increase first and then decrease with an increase in cold deformation, while the elongation after fracture After a period of decrease, it slightly increased. AFA-50% Both the tensile strength and elongation at break of the AFA-20% were reduced The dynamic difference is not obvious, mainly due to the toughening effect of NiAl phase. Brittle transition plays a good strengthening role at room temperature, It is difficult to achieve good strengthening effect in high temperature environment, but The material plasticity can be appropriately improved during the operation process.
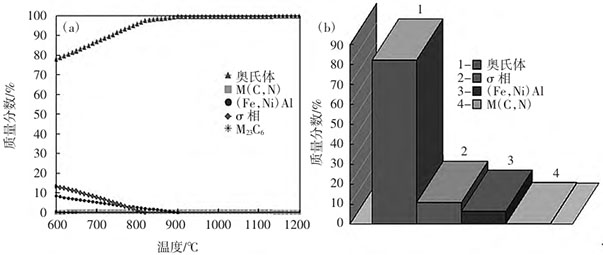
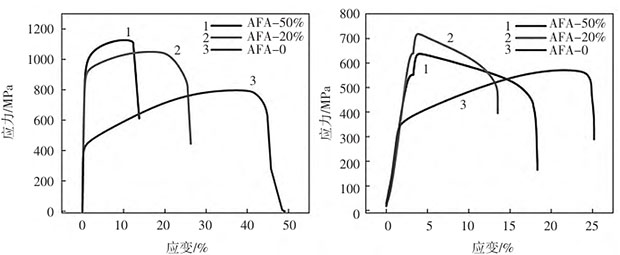
Corrosion analysis of heat-resistant austenitic steel
Study the corrosion of material surface at different temperatures. The surface of the material has appeared corrosion pits, external oxidation layers, and internal oxidation zones, which further The size range of the research is determined. The precision casting boiler used in the test The tube is a BTF-1200C-III tubular heating furnace, and the experimental temperature is divided into Do not set it to 650℃, 675℃, 700℃, 725℃, etc. Introduce nitrogen into the furnace at a rate of less than 5°C/min, and introduce it into the furnace tube Start the syringe pump, close the cylinder valve, and fill it with nitrogen. Remove the sample. The liquid water flow rate of the heating furnace is 0.8036 μL/min, The total flow rate of the mixed gas is 40.0 mL/min, and the volume fraction is 77.0%N2 +15%CO2 +3.75%O2 +5.0%H2 O(g)+0.32%SO2 , The pressure is 105kPa. Table 4 shows that the degree of oxidation and corrosion of materials is related to temperature. The degree is proportional to the resistance to oxidation and corrosion of S31042 material. The anti-oxidation and corrosion resistance of S31035 and C-HRA-5 materials It’s fair enough.
Conclusion remarks
At 1200℃, the alloy After solid solution treatment for 40 minutes, water quenching produces a solid solution sample. When the cold deformation is 20%, the yield strength of the experimental steel can be appropriately increased. Strength, after the cold deformation is increased to 50%, the strength improvement is significant. Not obvious, but it is easy to reduce plasticity. Properly controlling the interlayer temperature can It is beneficial to enhance the corrosion resistance and ductility of welded joints, avoiding the appearance of weld defects. The quality fraction of σ phase at 650℃ 10.88%, austenite mass fraction of 82%, NiAl mass fraction 6.64%, MC mass fraction of 0.19%, and an increase in deformation from 20% After reaching 50%, the tensile strength is 1131MPa, and the yield strength is slightly increased. The elongation rate decreases after the fracture. In summary, the optimal conditions for cold deformation are 20%, at which the overall plasticity of the heat-resistant austenitic steel is relatively good, The degree of hardness is high, which can meet the process requirements of precision casting for boiler pipe fittings.