This article focuses on the application of lost foam casting technology in the production of castings, aiming to analyze and solve the problems of casting defects that often occur in this process. Through in-depth research on the causes of defects such as sand sticking, porosity, and sand washing in the production of flywheel housings and other products, corresponding improvement measures are proposed. The research results show that by adjusting the combination process of patterns, optimizing the pouring system, arranging exhaust and slag discharge risers, and ensuring the rational layout of the inner gate inlet, the goal of improving casting quality and reducing defect rates can be achieved. This article provides a theoretical basis and practical reference for promoting the development and application of lost foam casting technology in the casting industry.
1. Introduction
1.1 Overview of Lost Foam Casting Technology
Lost foam casting technology is a modern casting method that has developed rapidly in recent years. It uses expandable polystyrene foam patterns, which are coated with a refractory coating and then buried in unbonded sand. When the molten metal is poured into the mold, the foam pattern vaporizes and is replaced by the metal, resulting in a casting with high dimensional accuracy and good surface quality. This technology has the advantages of low pollution, high flexibility, and low labor intensity, making it widely used in the production of various castings, especially complex shell castings.
1.2 Significance of Studying Lost Foam Casting Defects
Although lost foam casting technology has many advantages, it also faces some challenges, such as the occurrence of casting defects. These defects not only affect the quality and performance of the castings but also increase production costs and reduce production efficiency. Therefore, studying the causes and solutions of lost foam casting defects is of great significance for improving the quality and competitiveness of castings and promoting the sustainable development of the casting industry.
2. Causes and Improvement Measures of Sand Sticking Defects
2.1 Causes of Sand Sticking Defects
Sand sticking defects occur when the molten metal adheres to the sand grains on the surface of the casting during the pouring process. In the production of flywheel housings, the 不合理 placement and structural design of the casting can lead to insufficient vibration compaction of the mold cluster in the sand box, resulting in sand sticking defects. For example, in the production of the 9661 flywheel housing, the existing process has problems such as a large area, thin base wall thickness, and easy deformation. The inner gate size is 50 mm (length) × 30 mm (height) × 6 mm (width), the molten iron tapping temperature is 1460 – 1470 °C, the pouring temperature is 1430 – 1440 °C, the vacuum degree is -0.025 MPa, without film coating and pressure maintaining. The main defect is sand inclusion at the top of the inner cavity of the flywheel housing, with a rejection rate of 20%. The reason for this is that the motor hole is located at the bottom in the existing process, and the angle at the top is greater than 90°. During the vibration process, the molding sand cannot be filled densely, and the top molding sand is relatively loose. During the filling process of the molten iron, the local molten metal adheres to the molding sand, resulting in sand sticking.
2.2 Improvement Measures for Sand Sticking Defects
To solve the sand sticking problem, the following measures can be taken:
Improvement Measure | Specific Method | Effect |
---|---|---|
Adjust the placement of the white pattern | Place the motor hole of the flywheel housing upwards to facilitate the filling of molding sand and ensure sufficient molding sand at the top of the flywheel housing. | Ensure the tightness of the molding sand at the top of the casting and reduce the occurrence of sand sticking defects. |
Increase the distance between two flywheel housings | Increase the distance between two flywheel housings from the original 80 mm to 120 mm to ensure sufficient distance between the two mold clusters and the compactness of the molding sand. | Improve the strength of the molding sand and reduce the probability of sand sticking. |
2.3 Production Verification of Sand Sticking Improvement Measures
After implementing the above improvement measures, production verification was carried out. In the normal production process, while ensuring that variables such as the dipping process, pouring temperature, and vacuum pumping remained unchanged, production verification was carried out from small batches to large batches. The results showed that the sand sticking defect was reduced to 0, achieving the goal of completely solving the sand sticking defect at the top of the flywheel housing.
3. Causes and Improvement Measures of Porosity Defects
3.1 Causes of Porosity Defects
Porosity defects are caused by the gas and residues generated by the vaporization and decomposition of the white pattern not being discharged in time when the molten iron enters the mold cluster, resulting in pores on the surface of the casting. In the production of the flywheel housing of SAIC Maxus, the porosity defect is manifested as smooth holes of different sizes on the surface after machining, with an oxide color on the hole wall, and the pores are mainly concentrated at the top of the product, which is a characteristic manifestation of subcutaneous porosity. The main influencing factors include: low pouring temperature, which leads to incomplete combustion of the foam and incomplete gas discharge, resulting in pores under the skin; too thick coating at the motor hole, which prevents the gas from being discharged after the foam burns, resulting in pores; low vacuum degree, which makes the gas unable to be pumped away in time, resulting in pores; and unreasonable process design, such as the lack of exhaust ports at the top of the flywheel housing, which causes the gas to accumulate at the top of the body and not be completely discharged, resulting in pores.
3.2 Improvement Measures for Porosity Defects
To address the porosity issue, the following measures can be implemented:
Improvement Measure | Specific Method | Effect |
---|---|---|
Increase the pouring temperature | Increase the pouring temperature from 1430 – 1440 °C to 1450 – 1460 °C and pour 10 groups. | Promote the complete combustion of the foam and the discharge of gas, reducing the occurrence of porosity defects. |
Reduce the coating thickness | Reduce the coating thickness at the motor hole from 2.0 mm to 0.5 mm and pour 10 groups. | Facilitate the discharge of gas generated by the combustion of the foam and reduce the formation of pores. |
Increase the vacuum degree | Increase the vacuum degree from -0.025 MPa to -0.045 MPa and pour 10 groups. | Improve the gas discharge efficiency and reduce the probability of porosity defects. |
Add an exhaust piece at the motor hole | Add an exhaust piece with a size of 50 mm (length) × 30 mm (height) × 5 mm (width) at the motor hole and pour 10 groups. | Provide an additional gas discharge channel and effectively solve the porosity problem. |
3.3 Production Verification of Porosity Improvement Measures
After taking the above improvement measures, production verification was carried out. In the process of process testing, the control variable method was used to ensure that the other three process parameters remained unchanged. The results showed that the best result was obtained by adding an exhaust piece at the motor hole, with a porosity ratio of 0%. Subsequent verification from small batches to large batches also showed normal processing, achieving the goal of completely solving the porosity defect at the motor hole.
4. Causes and Improvement Measures of Sand Washing Defects
4.1 Causes of Sand Washing Defects
Sand washing defects occur when the direct runner, transverse runner, and inner runner in the mold cluster pouring system are not completely closed during the pouring process, especially the direct runner, which is prone to siphoning, resulting in sand washing defects. In addition, the unreasonable design of the product pouring system, such as unsmooth filling and high local pressure in the inner runner, can cause the coating to crack due to the scouring of the molten iron, and then the molding sand enters the mold cavity with the molten iron, also leading to sand washing defects. In the production of the connecting rod bracket casting, the material is HT200, the mass is about 50 kg, the contour size is 572 mm × 380 mm × 348 mm, the bottom plate thickness is 12 mm, and the existing process is to introduce the molten iron through three inner runners on the side. The inner runner size is 60 mm × 30 mm × 6 mm, the molten iron tapping temperature is 1460 – 1470 °C, the pouring temperature is 1430 – 1440 °C, the vacuum degree is -0.03 MPa, without film coating and pressure maintaining. The main defect is sand washing, and the location is concentrated near the bottom inner runner, with a rejection ratio of 20%.
4.2 Improvement Measures for Sand Washing Defects
To solve the sand washing problem, the following measures can be taken:
Improvement Measure | Specific Method | Effect |
---|---|---|
Increase the coating thickness of the inner runner | Increase the coating thickness of the inner runner by one dipping process, and the coating thickness is 2.2 mm. | Improve the strength of the inner runner coating and reduce the probability of coating cracking and sand washing. |
Increase the number of inner runners | Add an inner runner of the same size at the bottom two points. | Distribute the flow and reduce the pressure of the molten iron, reducing the scouring of the coating and the occurrence of sand washing defects. |
4.3 Production Verification of Sand Washing Improvement Measures
After implementing the above improvement measures, production verification was carried out. In the process of process testing, while ensuring that the pouring temperature, vacuum degree, and other influencing parameters remained unchanged, production verification was carried out from small batches to large batches. The results showed that the best result was obtained by adding an inner runner at the bottom, with a sand washing ratio of 0. Subsequent verification from small batches to large batches also showed normal processing, achieving the goal of completely solving the sand washing defect of the connecting rod bracket.
5. Conclusion and Outlook
5.1 Summary of Research Results
This article analyzes the causes of sand sticking, porosity, and sand washing defects in the production of flywheel housings and other products by lost foam casting technology and proposes corresponding improvement measures. Through adjusting the combination process of patterns, optimizing the pouring system, arranging exhaust and slag discharge risers, and ensuring the rational layout of the inner gate inlet, the casting quality has been effectively improved, and the defect rates have been significantly reduced. The research results provide a practical reference for solving the problems of lost foam casting defects in the casting industry.
5.2 Future Research Directions
Although certain achievements have been made in this study, there are still some areas that need further research and improvement. Future research can focus on the following aspects:
- Further optimization of the lost foam casting process parameters to improve the quality and performance of castings.
- Development of new refractory coatings and molding materials to adapt to the requirements of different casting products and improve the surface quality and dimensional accuracy of castings.
- Strengthening the research on the mechanism of defect formation in lost foam casting to provide a more theoretical basis for the prevention and control of casting defects.
- Exploring the application of advanced technologies such as numerical simulation in lost foam casting to predict and optimize the casting process and reduce the trial and error costs in production.
In general, the research and application of lost foam casting technology have broad prospects. By continuously improving the technology and process, the casting industry can achieve higher quality, higher efficiency, and more sustainable development.
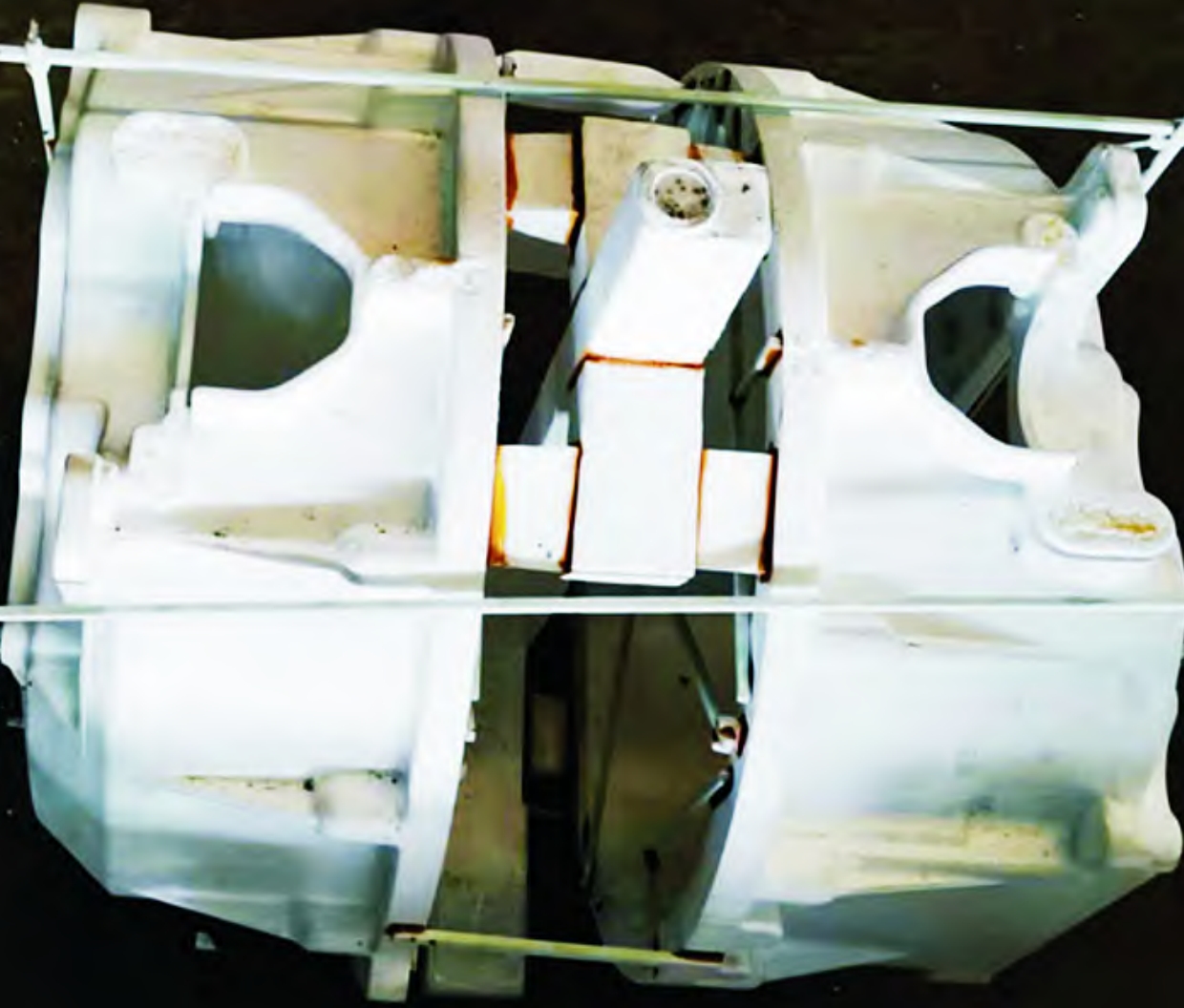