A steam turbine, also known as a steam turbine engine, is a rotary steam power unit. The high-pressure steam chamber is a component of the steam turbine and is made of ZG15Cr2Mo1 material. The steam chamber is a chamber set up to balance the steam flow after the steam passes through the main steam valve and enters the regulating steam valve; A rotor can be installed in the circular cavity of the steam chamber, and steam enters through the inlet of the steam chamber and flows out through the outlet of the steam chamber, thereby blowing the rotor to rotate. The service temperature of the high-pressure steam chamber is high, and the pump water pressure is 8.28MPa, about 82 atmospheres, which needs to be maintained for 10 minutes No water leakage; Under these service conditions, the steam chamber must maintain uninterrupted operation for a long time and meet the requirement of a 20-year service life. Therefore, the high-pressure steam chamber is exposed to a high-temperature and high-pressure working environment for a long time, which affects the casting The quality requirements for the body are extremely high, and cast steel parts are often used.
In traditional casting industry, the production of castings generally adopts the steps of trial production first and analysis later. Only by repeatedly adjusting and improving the casting scheme can the correct process be obtained. This not only wastes manpower and material resources, but also increases the production cycle. Using casting simulation software for casting process simulation optimization research can reduce research and development cycles and labor costs. Currently, many types of complex castings (cast steel, cast iron, cast aluminum, etc.) have adopted simulation technology for casting process improvement and optimization. Based on the chemical composition of the casting, it is known that the liquidus line is 1501 ℃, and the obstructed line shrinkage rate of the casting is 1.8%. It is necessary to design a riser for shrinkage treatment to ensure the comprehensive performance of the casting. Each type of casting alloy has its appropriate wall thickness range. If appropriate, it can ensure the mechanical performance requirements of the casting, facilitate casting production, save metal materials, and reduce casting quality. Based on the dimensional characteristics of high-pressure steam chamber cast steel parts, according to the minimum wall thickness list of sand casting cast steel parts in the casting manual, the minimum wall thickness is 20mm. Analysis results of wall thickness of steam chamber castings. analysis It can be seen that this casting meets the minimum wall thickness and critical wall thickness requirements.
The design of casting process plan includes the determination of molding materials, casting pouring positions, parting surfaces, sand cores, and process parameters. The pouring position of a casting refers to the position of the casting in the mold during pouring. Casting parting surface refers to the joint surface between the components of the mold, which is made into several parts to facilitate the extraction of the mold. The selection of parting surface should be as consistent as possible with the pouring position, and the two should be coordinated as much as possible to make the casting process simple and easy to obtain high-quality castings. Reasonable selection of pouring position and parting surface can directly simplify the casting process, improve productivity, reduce costs, and improve casting quality. There are two reasonable pouring positions and parting surfaces for high-pressure steam chambers in castings: vertical and horizontal. The casting is poured in a vertical position, and the height of the sand box will be too high. During the filling process, the metal liquid will have a great impact on the mold cavity, resulting in uneven filling. At the same time, the parting surface is selected on the surface of the steam chamber base to meet the principle of taking the parting surface at the maximum section, but the fitting is prone to misalignment. When casting in a horizontal position, the maximum cross-section can be taken as the parting surface for easy mold removal; When designing the shrinkage filling process, the thick position of the casting is located above, making it convenient to place the riser for shrinkage filling; In addition, the horizontal pouring position can also avoid the use of core supports, simplifying the process design. In summary, the process design adopts a horizontal pouring position and parting surface.
The pouring temperature of steam chamber cast steel parts is relatively high (about 1580 ℃), and the steel liquid has strong thermal impact on the sand mold, requiring high refractory requirements for the sand mold and sand core. The SiO2 content in the selected raw sand should be ≥ 97%. Phenolic resin sand molding and core making are used, and corundum powder alcohol based coating is selected. The spraying method is easy to operate, has high production efficiency, and is fast and effective. The placement of sand cores during casting. Based on the internal cavity structure of the casting, the required sand cores are determined, and it is proposed to design this casting with 3 sand cores.
Conclusion
1) An analysis of the casting process was conducted based on the material and structural characteristics of the high-pressure steam chamber. A preliminary casting process plan for high-pressure steam chamber cast steel parts was designed through theoretical calculations. ProCAST casting simulation software was used to simulate the filling and solidification process of the original casting process plan. The pouring temperature was set to 1600 ℃ and the pouring time was 18 seconds. The heat transfer coefficient between the metal and the sand mold was h=750W/(m2 · K), based on casting defects
Improve the design of the original process plan based on the type and location of production.
2) Design risers at the thick areas on both sides of the convex platform and base at the top of the steam chamber, and place external cooling iron on both sides of the steam inlet partition and the closest defect to the base inside the steam chamber. Perform numerical simulations again on the improved process. The simulation results show that the improved process scheme eliminates shrinkage defects, with a total shrinkage porosity of 2.71%, providing a process design idea for further completely eliminating shrinkage defects.
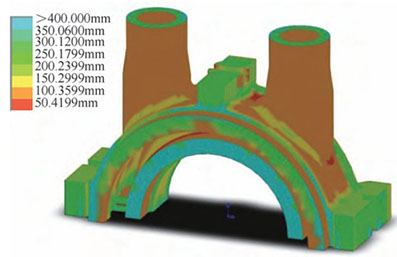