The basic principle of low pressure casting is: under the action of pressure, the liquid metal at a certain temperature slowly enters and fills the mold cavity and riser along the riser from bottom to top through the sprue, then pressurizes and holds the pressure until the casting is completely solidified, and finally relieves the pressure, so that the liquid metal in the riser and sprue that has not yet solidified flows back to the holding furnace or crucible due to its own weight. According to the principle of low-pressure casting technology, the process of low-pressure casting can be roughly divided into several stages: liquid rising, mold filling, pressure increasing, pressure maintaining solidification and pressure relief cooling. In the phase of liquid lift filling, compared with gravity filling, the dynamic force of liquid metal flow is different. The filling process of low-pressure casting is to control the pressure applied on the metal surface and push the liquid metal into the cavity along the liquid lift pipe. Its main features are controllable filling process pressure, stable filling of liquid metal, avoidance of vortex, churn, impact and splash under gravity filling, reduction of the tendency of gas absorption and oxide inclusions, in order to obtain castings without porosity and oxide inclusions. The key of low pressure casting is the filling process, which can be divided into two stages: liquid rising stage and filling stage. In the filling process, the main problem is the turbulence of the metal liquid, which can be solved by adjusting the pressure. The filling speed depends on the pressurization speed. Controlling the pressurization speed and keeping the laminar flow of liquid metal is the key to obtain high quality castings.
It can be seen from the principle of low pressure casting that the filling speed of alloy liquid, the stability of liquid flow and the jump speed of pressure are crucial issues for the production process of low pressure casting. Many scientists and technicians at home and abroad have carried out a lot of basic research and engineering practice in this field, and made a lot of new progress.
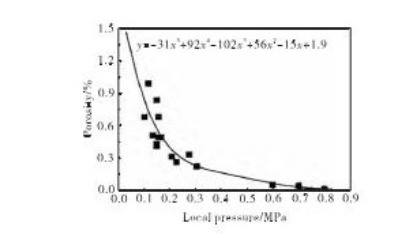
In terms of basic research, sun Chul huh et al. [20] of gyeongshan National University in South Korea took fecrsi metal fiber as reinforcement system to form porous preform, AC8A aluminum alloy as base metal, used low-pressure casting method to infiltrate molten aluminum alloy into porous preform to prepare aluminum matrix composite, and established the best filling process parameters of low-pressure casting, At the same time, the seepage behavior of liquid metal in porous preform is analyzed. The results show that with the increase of pressure, the compression time is shortened and the porosity is gradually reduced. When the pressure is 0.8MPa and the compression time is 1s, the porosity is zero; At the same time, based on Darcy’s formula and direct difference method, the distribution rule of filling pressure in porous preform is calculated. Figure 3 shows the relationship curve between the pressure distribution in preform and the porosity in preform. The results further show that with the increase of filling pressure, the porosity gradually decreases, and the porosity is zero at 0.8 MPa. It is found that the main reason for the decrease of porosity in the composite is that the increase of pressure improves the surface wettability between the metal matrix and the reinforcement. The higher the pressure is, the better the surface wettability between the aluminum alloy liquid and the metal fiber is, which also promotes the infiltration of the alloy liquid in the porous metal fiber preform. The results show that the fatigue life and wear resistance of the engine piston made of aluminum matrix composite materials are better than that of a366.0 aluminum alloy piston.
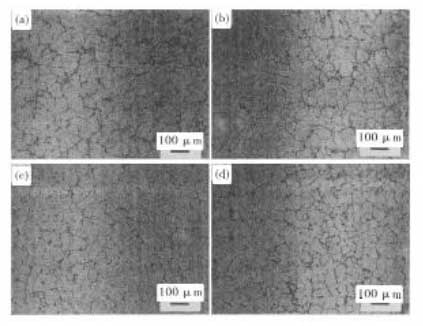
The D.M. maijer research team of the University of British Columbia in Canada has been focusing on the industrial application and development of computer numerical simulation technology in low-pressure casting aluminum alloy parts. Recently, they used numerical simulation technology to predict and analyze the defects of macro porosity, micro porosity and oxide film in the process of low-pressure casting aluminum alloy parts for automobile hub, and combined with the simulation results, they discussed how to optimize the actual low-pressure casting process parameters to reduce these defects and the overall performance of aluminum alloy parts. The results of numerical simulation show that the casting defects of aluminum alloy parts of automobile wheel hub mainly depend on the filling process and heat conduction process of liquid metal in the process of low pressure casting. During the filling process, the uncertainty of the gas movement track in the mold cavity is the main reason why the numerical simulation results of the filling process are difficult to match the actual low-pressure casting process, D. On the basis of considering the influence of gas inside the cavity on the filling process, the research team of M. maijer used the numerical simulation technology to optimize the pressure parameters of the filling process to obtain the flawless A356 aluminum alloy hub model, which was verified by experiments.
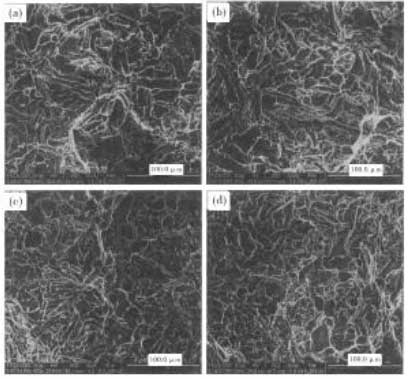
The State Key Laboratory of solidification technology of Northwest University of technology in China has carried out a systematic study on the low pressure casting process. Hao Qitang et al. Used ZL114A aluminum alloy as raw material to cast different thickness plate parts on the self-made low-pressure casting equipment, and studied the filling and solidification characteristics in the low-pressure casting process. The results showed that the actual filling speed of low-pressure casting was less than the theoretical given speed, and the more complex the mold cavity structure, the smaller the casting cross-sectional area, the greater the filling obstruction to the liquid metal, The slower the filling speed is, the better the resistance coefficient should be. The experimental results of different thick plates show that the whole filling process is stable without fluctuation and the occurrence of oxidation inclusions and air entrainment can be effectively reduced under the filling speed of 40mm / s. The solidification structure analysis shows that the casting has no defects and excellent microstructure and properties under this filling speed. The main reason is that on the one hand, the filling process of alloy liquid is sequential, on the other hand, the filling time of low-pressure casting is longer than that of gravity casting, which is conducive to the exhaust of air in the cavity. Li Jianfeng et al. [28] studied the solidification characteristics and filling rules of A357 Alloy under the condition of low pressure casting. The experimental results show that when the filling pressure is increased to 30 kPa and the rising liquid of the alloy liquid is stable and full of the cavity, the high-quality macromorphology, fine grain structure and excellent mechanical properties of the casting can be obtained. Through analysis, the flow law of liquid metal filling cavity is obtained: under the action of certain pressure, the liquid flow entering the cavity tends to maintain its movement direction and momentum, so as to form the undercurrent throughout the filled area. During the movement, the undercurrent constantly exchanges momentum with the surrounding medium, which results in the expansion of the undercurrent, the average flow velocity gradually decreases, and at the same time, eddy current movement occurs on both sides, When the undercurrent reaches the liquid surface, its velocity is still greater than zero, and the free liquid surface is convex, which results in the transverse flow area under the action of static pressure difference.
Huazhong University of science and technology has been developing the CAE software of low-pressure casting process numerical simulation for a long time, and applying the principle of numerical simulation to the continuous research on the filling and solidification process of low-pressure casting. Liao dunming, et al. Simulated the filling and solidification process of low-pressure casting by using the low-pressure module of Huazhu CAE, and the results were in good agreement with the reality. The practical application also showed that the low-pressure casting CAE can effectively evaluate the rationality of low-pressure casting process design. The basic principle of its simulation filling process is based on the incompressible unsteady flow of liquid metal with free surface viscosity. The mathematical description of its motion state needs to use momentum conservation equation, mass conservation equation and energy conservation equation. The movement of free surface is determined by solving volume function equation with SOLA-VOF method. The numerical simulation of two low-pressure castings, aluminum alloy volute and aluminum alloy hub, is carried out and compared with the actual situation. The results show that the two are consistent. Through the numerical simulation, the design of the gating system of low-pressure casting can be effectively improved and the casting quality can be improved.