With the rapid development of the world economy, the overall precision manufacturing of large thin-walled complex components has become the development trend of the manufacturing technology of light alloy structural parts at home and abroad. The so-called thin-walled complex component refers to the casting with a wall thickness of 1-3mm and a complex shape, especially the casting prepared by the integral casting technology, which is more complex and difficult to achieve near net forming. However, the investment casting technology of large-scale integral thin-walled structure parts, such as low-pressure casting technology, centrifugal casting technology and so on, can obtain castings with good overall structure, high reliability, light quality and low processing cost. Therefore, this kind of technology is highly concerned by the domestic and foreign aerospace and civil fields. Low pressure casting technology has the advantages of less allowance and no allowance forming, and it is also an important measure to realize the precision, thin-walled, lightweight and energy-saving of automobile castings, which has been paid more and more attention by the casting industry. With the rapid increase of demand for large-scale, complex, thin-walled, precision, high-quality and high-strength light alloy castings in various industries, the whole precision casting technology of large-scale thin-walled complex aluminum alloy components has been paid attention to. Therefore, the research on the forming theory and preparation process of low-pressure casting technology has important theoretical and practical value for the wide application of light alloy complex thin-walled components in China.
How to effectively control the filling process and obtain the solidification structure with uniform composition, dense microstructure and fine grain size is the core problem to be solved in the preparation of high-quality large-scale thin-walled complex aluminum alloy parts by low-pressure casting technology. At present, researchers and engineers mainly study the low-pressure casting process, filling process, casting mold and casting materials to find the best way to improve the quality of castings. In this paper, the development of low-pressure casting technology is introduced. The principle of low-pressure casting, the technological characteristics of filling process and the development of casting materials are discussed. The development trend of low pressure casting technology in the future is also prospected.
The earliest origin of low-pressure casting technology can be traced back to the beginning of the 20th century. S.P. Wetherill and J.P. wetheriljr of the United States submitted a patent in 1906, which made the low-pressure metal mold casting equipment successfully used to cast a series of zinc aluminum alloy castings. According to the former Karl Schmidt company in West Germany, in 1910 a.l.j. Queneau studied the resistance crucible furnace as a low-pressure casting equipment for aluminum bronze and manganese bronze castings. At the same time, British E.F. Lake invented a patent for casting equipment of lead and tin alloy up to 300 ℃, which is also the recognized origin of low-pressure casting technology in the public literature . In 1917, France published a low-pressure casting machine for aluminum casting, which uses the pressure generated by water evaporation as a pressure device. In 1924, the German company allgemein elecktricit TS gesellscl ft made a device for mounting several molds on the turntable, casting conduit on it and continuous casting when rotating [9]. However, after about 20 years of industrial application, especially after the use of metal mold casting, there has been little development. After World War II, it was found that low-pressure casting could solve the wall thickness effect of heavy section aluminum alloy castings, that is, the mechanical properties of aluminum alloy castings decreased sharply due to the increase of wall thickness. Because of the high feeding pressure and temperature gradient, the densification of heavy section castings is improved effectively. This technology is still used in the casting of heavy section castings [11]. After World War II, E.C. Lewis of British alumasc company carried out the research on low-pressure casting technology, and his achievements were widely used in the production of textile machine parts, underwater engineering parts and general mechanical castings in Japan and other countries, with remarkable results. Especially in 1950, the beer barrel made of light alloy was successfully studied. In the next 10 years, we have basically achieved a high degree of production seriation. It is the Thin-walled Casting of the beer barrel made by casting, which is welded by automatic argon arc welding. In the same year, the Austrian company Mandle Berger introduced the low-pressure casting technology of alumasc company, especially the research of casting machine, which expanded the production range of automobile parts and successfully carried out mass production. In 1954, the former Karl Schmidt company of West Germany introduced technology from Berger company and signed a technical contract with E.C. Lewis. It carried out the research and development of auto parts and the mechanized production of metal mold, and carried out the research of typical casting unit, thus expanding the original planned production. This technology has aroused the interest of American automobile manufacturer GM company. They have introduced technology and accepted dozens of casting machines. They have paid great attention to this technology in the light alloy casting factory (Massena) of air-cooled engine of Corvair vehicle. Later, they have carried out the research on low frequency induction furnace for low-pressure casting together with Otto Junker company. Especially after 1950, due to the development of automobile industry, low-pressure casting technology and equipment has made a leap. Due to the high quality requirements, the structure of automobile hub is suitable for low-pressure casting, and the demand is large, so it greatly promotes the development of low-pressure casting technology [13]. In the 1960s, Britain took the lead in the development of low-pressure casting automobile hub, followed by the United States, Japan and the former West Germany. According to the statistics in 1989, the annual output of low-pressure casting wheel hubs of parkficld Wheel Co., Ltd. in the United States has reached 2.5 million, and 14 automatic low-pressure casting machines have been used in Hitachi metal manufacturing Institute in Japan, with an annual output of 1.8 million aluminum alloy wheel hubs. Stahlschmidt & maiworn, Germany, uses 30 low-pressure casting machines to produce 2 million aluminum wheels per year. 80% to the O.E.M market, including Audi, Ford, GM, Mercedes Benz, Porsche and Volvo. All of Renault’s engine cylinder heads are produced by low-pressure casting, with 11 low-pressure casting machines and 5500 cylinder heads per day. The market share of cast aluminum wheel hub was only 4% in 1981, increased to 40% in 1994 and 60% in 2000. Most of the production of cast aluminum wheel hub adopts low-pressure casting in the world. At present, the famous foreign manufacturers of low-pressure casting machine and complete set of equipment are: EM pire company in the United States, Isuzu company in Japan, plume company in the United Kingdom, rimatic company in Denmark, and GIMA and Kurtz company in Germany. The product specifications are relatively complete, and the aluminum alloy capacity of the holding furnace is 300-1000kg. Series products have entered Chinese enterprises.
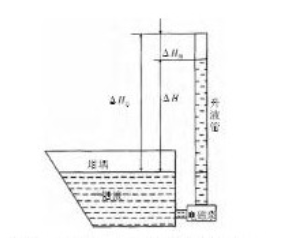
Low pressure casting has been studied in China since 1950s, but its development has been relatively slow. With the development of automobile industry and the adoption of a large number of new technologies, around 2000 [8,11,14,15], low-pressure casting has developed rapidly in China. The function and performance of the domestic low-pressure casting machine, as well as the stability and reliability of its use have approached or reached the international advanced level, and it has been widely used in the production of automobile wheel hub, automobile cylinder head and other castings. The main manufacturers of domestic low-pressure casting machine include Jinan casting and Forging Research Institute (J455), Shanghai Machinery Manufacturing Technology Research Institute (fdz-a, fdz-c), Jiangsu Guannan die casting machine factory (j453a, j453b), Tianshui casting machine factory (J452, j453) and Shenyang Casting Research Institute (803 liquid surface pressing system), etc. Domestic low-pressure casting machine is not series, no complete set of supply capacity. The most important problem is that the disconnection of equipment and process makes the product yield low, the production failure frequent, and the productivity low. The low-pressure casting machines of Qinhuangdao daika hub company, the largest hub factory in China, and Guangdong Zhongnan aluminum alloy hub company are provided by German and American companies respectively.
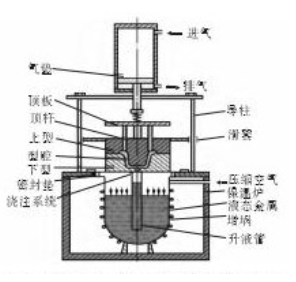
There are two pouring methods in low-pressure casting, one is to pressurize with gas, the other is to transport conductive liquid metal by electromagnetic pump. Electromagnetic low-pressure casting was invented by British cos worth company and later called Cosworth process. Its principle is shown in Figure 1. The electromagnetic pump of the casting method has poor utilization ratio, and the pump head is easy to be damaged, so it must be replaced frequently. Zircon sand is selected as the sand mold, which is expensive, so the cost of electromagnetic low-pressure casting is high. In comparison, the control method of gas pressurization has the advantages of low cost, low power consumption and easy promotion.
The traditional gas pressurized low-pressure casting is a forming method that the molten metal is filled from bottom to top under the action of low gas pressure, and then solidified under pressure to obtain the casting. The principle is shown in the figure. It is to apply 0.0098 ~ 0.049mpa dry gas on the metal liquid surface of the sealed crucible, and the pressure rises gradually, so that the metal liquid rises along the high temperature resistant pipe (commonly known as the rising liquid pipe) placed in the metal liquid and flows into the mold cavity above the crucible, and the pressure stops when the metal liquid completely solidifies from the upper part of the mold to the gate; the metal liquid in the rising liquid pipe flows back to the crucible and demoulds the parts.