A lot of research and application have been carried out on Squeeze Casting Technology in foreign countries. For example, casting technology company and Delphi chassis systems have started the joint development of automobile light alloy front steering knuckle since 1994, and in recent years, they have produced large parts such as automobile V6 engine cylinder, engine support and tank load wheel. In terms of equipment, manufacturers in Japan, Switzerland and other countries have produced large-scale squeeze casting special equipment with a clamping force of 3550 tons. In view of the confidentiality measures taken by relevant technical parties, there are very few foreign countries with reference value except product samples and advertisements.
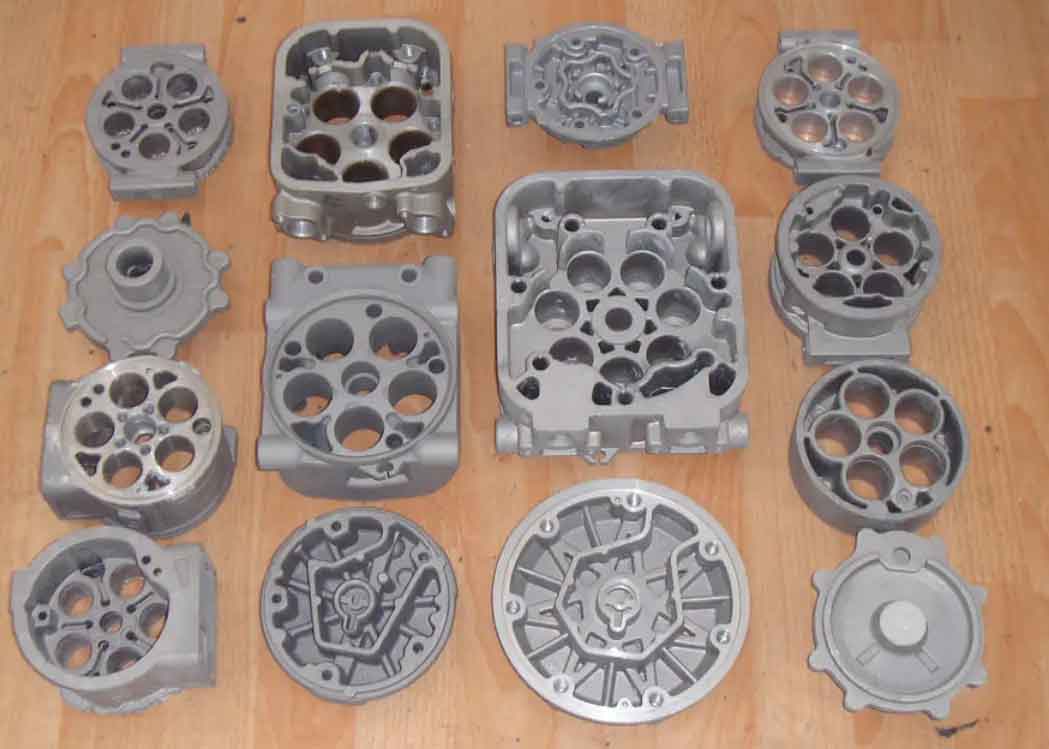
Limited by the research conditions, the domestic research on squeeze casting mainly focuses on the forming of small and medium-sized parts. For example, Bulei et al. Designed the indirect squeeze casting die for automotive fork parts; Luo Jiping simulated the indirect squeeze casting process of motorcycle tongs, and obtained the optimized process parameters; Zhaohongjin et al. Carried out experimental research on direct squeeze casting of magnesium alloy shaft and tube; Zhang Zhanzhan et al. Studied the squeeze casting process of magnesium alloy wheel hub, and obtained the best process parameters by experimental method; Chenjuanjuan et al. Studied the double squeeze casting forming technology of aluminum alloy connecting rod, and analyzed the die structure and process flow.
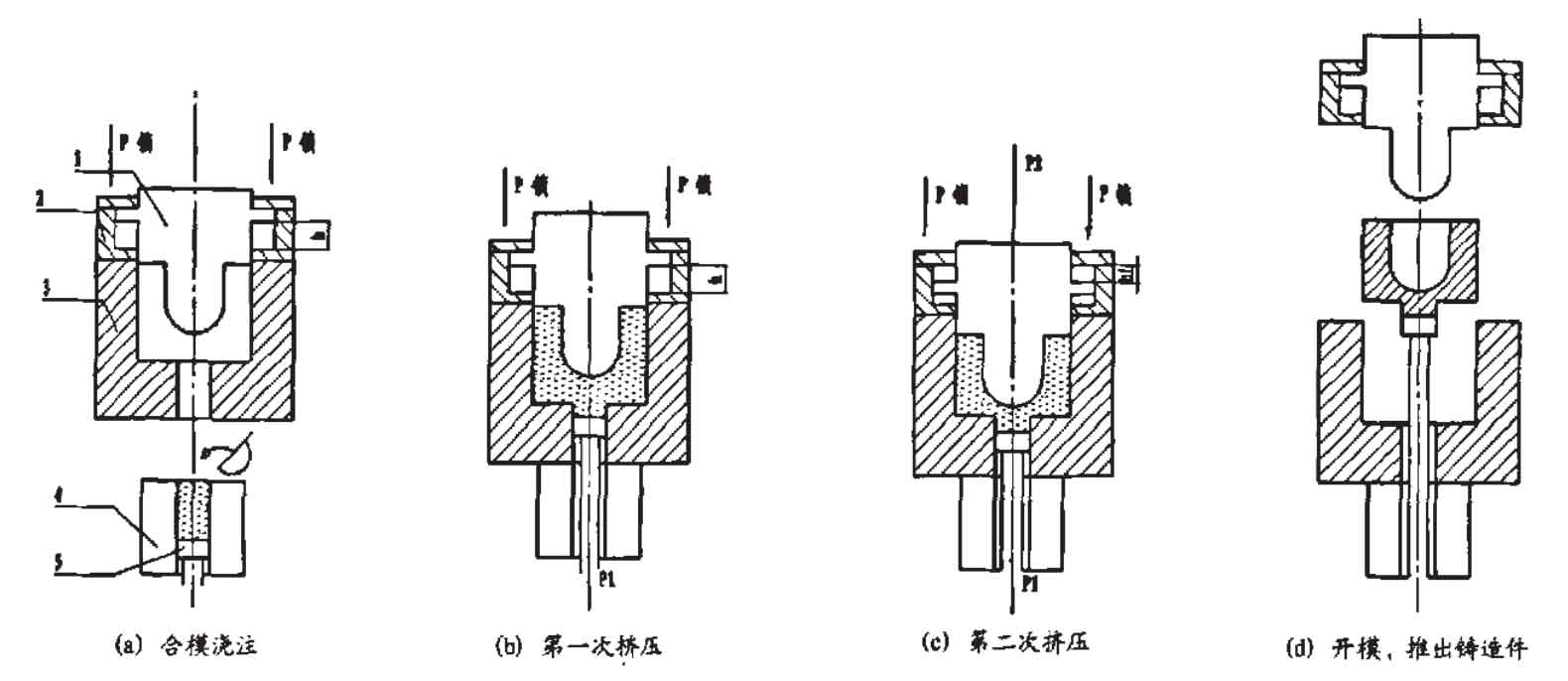
In particular, in recent years, qipixiang and others have proposed a double squeeze casting method, which is also called continuous casting and continuous forging or casting forging double control forming. Its working principle is that the mold filling head sends the metal melt in the mold filling device into the cavity composed of the upper and middle mold with pre closed and locked mold and the upper mold with a certain amount of reduction reserved and continues to maintain the pressure, and then the upper mold goes down to implement the second extrusion on the semi solidified or solidified castings, Until the casting solidifies, as shown in the figure. This method is formed by two times of squeeze casting, the first is indirect squeeze casting, the second is direct squeeze casting, and its technical core is secondary extrusion. The double squeeze casting method has high requirements for equipment, and a three action extrusion equipment controlled by computer must be used.
At present, there is relatively little research on the squeeze casting method and process of complex large parts in China, and indirect squeeze casting is mainly used. For example, Li Yuanyuan and others use Al Cu Mn material to study the indirect squeeze casting of large wheel hubs. The mechanical property test results of castings after T5 state heat treatment show that the average tensile strength and elongation of castings reach 390mpa and 10% respectively; Liyuanyuan et al. Also studied the electromagnetic pump assisted indirect squeeze casting of large aluminum alloy gold support, which proved the feasibility of the electromagnetic filling indirect squeeze casting process; Houliqun et al. Used the existing cast aluminum alloy and deformed aluminum alloy materials to study the squeeze casting forming of the light combat vehicle load wheel, and studied the effects of direct punch extrusion, indirect extrusion and double extrusion on the mechanical properties of the formed parts. The maximum overall dimension of the formed load wheel is 580mm, and the weight is about 30kg. The research results show that the tensile strength of the formed load wheel is 227 ~ 375mpa under 50MPa extrusion specific pressure, The elongation is 5 ~ 12%.
At present, the main reason that hinders the application of squeeze casting technology for large parts at home and abroad is the lack of extrusion casting methods and equipment for large parts, which restricts the development of related technologies.