Figure 1 shows the equivalent stress nephogram of vermicular cast iron pressure plate. It can be seen that the equivalent stress on the surface of vermicular cast iron pressure plate is different and the stress distribution is uneven. The general rule is that the effective stress gradually decreases from the inner circle to the outer circle of vermicular cast iron pressure plate: the residual stress in the inner circle is higher, the residual stress in the three large lugs connected with the riser is higher, and the effective stress in the three small lugs is lower. The closer the vermicular cast iron pressure plate surface is to the outer circle, the smaller the equivalent stress is.
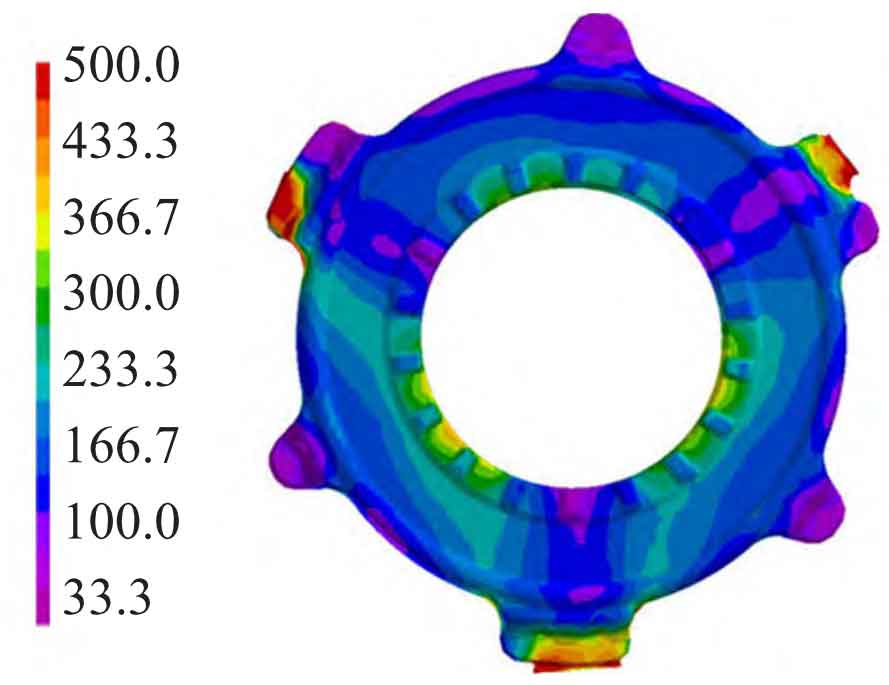
During the solidification process, the vermicular cast iron pressure plate gradually shrinks, and the cooling rates of different parts are different. Therefore, the shrinkage rates of various parts of the vermicular cast iron pressure plate are different, which interfere with each other, causing the vermicular cast iron pressure plate to deform and produce residual stress. It can be seen from Figure 1 that during the casting process, the equivalent stress of some surfaces (inner circle) of vermicular cast iron in contact with the sand mold and the large lug connected with the riser is too large, especially the equivalent stress of the large lug is as high as 360MPa, so there is a risk of crack formation. After sand falling, the thermal stress produced in the casting process will be retained, which will have an impact on the later primary and finish machining.
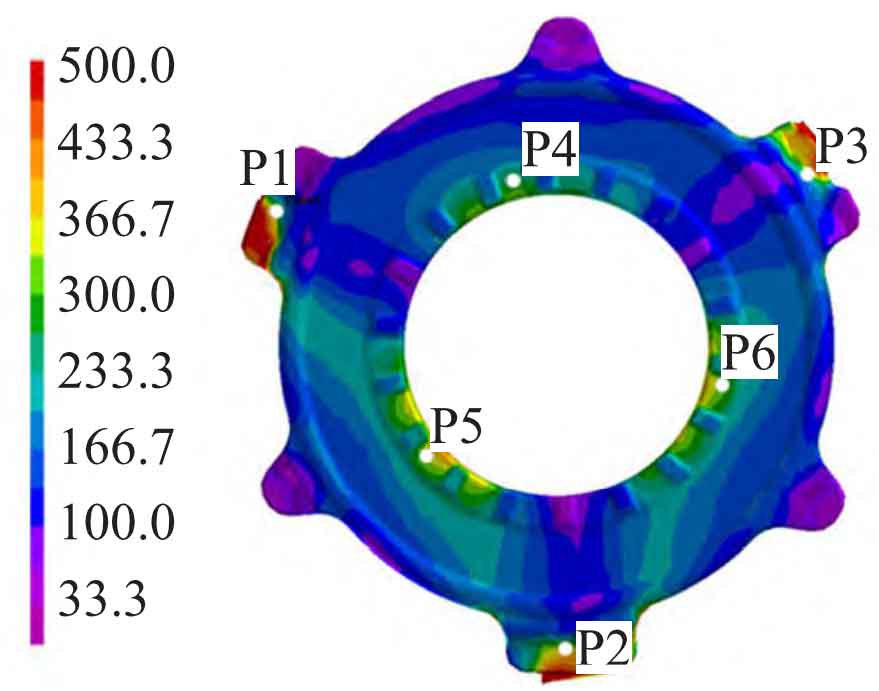
In order to deeply understand the change of stress of compacted vermicular cast iron pressure plate, the following nodes are selected to analyze the change of stress during mold filling, cooling and solidification of compacted vermicular cast iron. Principle of selecting nodes: select the points with large stress and easy to produce cracks. The schematic diagram of the selected node is shown in Figure 2, and the corresponding equivalent stress curve of the node is shown in Figure 3.
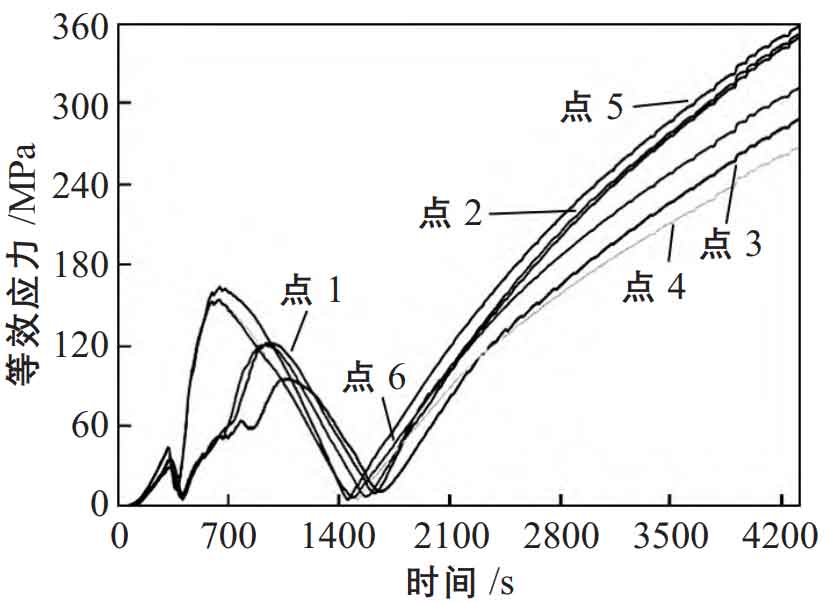
In Figure 3, it can be seen that the stress change of the node is roughly divided into three stages: the stage of rapid increase at the beginning, and then gradually decreases and then gradually increases as the cooling continues. First, when the vermicular cast iron starts to cool, the solid phase ratio of vermicular cast iron continues to increase. As the vermicular cast iron continues to solidify, the vermicular cast iron continues to shrink. At this time, different wall thicknesses of vermicular cast iron interfere with each other, and the sand mold also hinders each point. At this time, the equivalent stress of vermicular cast iron increases rapidly. With the continuous solidification of vermicular cast iron, secondary phase transformation occurs, and the volume will increase, which reduces the barrier effect between vermicular vermicular cast iron, thus reducing the equivalent stress. Finally, after the vermicular cast iron is completely solidified, the residual stress of vermicular cast iron increases continuously because of the different cooling rates at different parts, but the change rate of residual stress at this time is much smaller than that at the beginning of solidification.