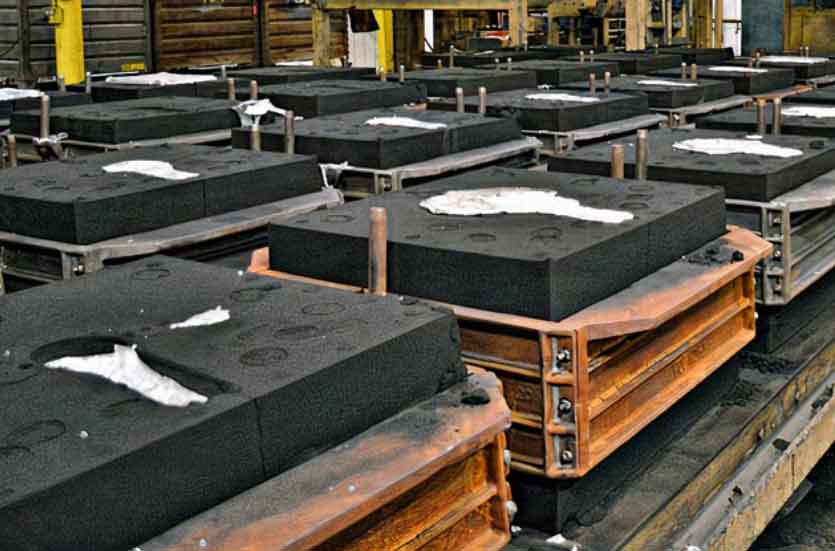
Resin sand casting is a popular casting process used to create intricate metal parts. It involves creating a mold from a mixture of resin and sand, which is then used to shape and cast the metal. In this comprehensive guide, we will explore the resin sand casting process in detail, including its applications, advantages, and limitations.
1. Process Overview:
Resin sand casting, also known as the no-bake casting process, consists of the following steps:
Pattern Creation: First, a pattern of the desired metal part is created using various materials, such as wood, plastic, or metal. The pattern should have the exact shape and dimensions of the final part.
Mold Preparation: A flask, typically made of metal, is divided into two halves: the cope (top) and the drag (bottom). The pattern is placed in the drag, and a release agent is applied to prevent the resin sand mixture from sticking to the pattern.
Resin Sand Mixture: Resin and sand are mixed together to form a mold. The sand is usually silica sand, and the resin is a synthetic material that hardens when exposed to a catalyst or curing agent.
Mold Assembly: The cope and drag are brought together, sandwiching the pattern between them. The two halves are securely clamped to maintain the shape of the mold.
Curing: The resin in the mold is cured by adding a catalyst or curing agent. This initiates a chemical reaction that hardens the resin and creates a rigid mold.
Pattern Removal: After the resin has cured, the pattern is removed from the mold. This leaves a cavity in the shape of the pattern, ready to receive the molten metal.
Casting: Molten metal, such as aluminum, iron, or bronze, is poured into the mold cavity. The metal fills the cavity, taking the shape of the pattern.
Cooling and Solidification: The molten metal is allowed to cool and solidify within the mold, ensuring that it takes on the desired shape.
Mold Breakout: Once the metal has solidified, the mold is broken apart to reveal the cast metal part.
Finishing: The cast part is cleaned, excess material is removed, and any required post-processing, such as machining or surface treatment, is performed.
2. Applications of Resin Sand Casting:
Resin sand casting offers versatility and is suitable for a wide range of applications across various industries. Some common applications include:
Automotive Industry: Resin sand casting is used to manufacture engine components, transmission parts, intake manifolds, and other automotive parts.
Aerospace Industry: The process is employed for producing aircraft engine components, turbine blades, and structural parts.
Industrial Machinery: Resin sand casting is used to create complex industrial machinery parts, such as pumps, valves, gears, and housings.
Energy Sector: The process is utilized in the production of wind turbine components, oil and gas industry equipment, and power generation components.
Art and Sculpture: Resin sand casting enables the creation of intricate metal sculptures and art pieces.
3. Advantages of Resin Sand Casting:
Resin sand casting offers several advantages over other casting processes:
Versatility: It can produce parts of various sizes, complexities, and shapes, including those with undercuts and internal features.
Good Surface Finish: Resin sand casting typically results in smooth surface finishes, reducing the need for extensive post-processing.
Cost-Effective: The process is generally cost-effective compared to other casting methods, especially for low to medium production volumes.
Dimensional Accuracy: Resin sand casting allows for high dimensional accuracy and tight tolerances.
Wide Material Selection: A wide range of metals, including ferrous and non-ferrous alloys, can be cast using resin sand casting.
4. Limitations of Resin Sand Casting:
While resin sand casting offers numerous benefits, it also has some limitations:
Pattern Wear: The pattern used in the process may wear out over time due to the repetitive molding process. It may need to be replaced or repaired periodically.
Production Time: The resin sand casting process can be time-consuming, especially for complex parts that require intricate mold assembly and curing.
High Tooling Cost: Initial tooling costs for resin sand casting can be relatively high compared to certain other casting methods.
Size Limitations: Very large parts may be challenging to produce using resin sand casting due to the handling and weight limitations of the molds.
Resin sand casting is a versatile and widely used casting process that allows for the production of complex metal parts with good dimensional accuracy and surface finish. It finds applications in industries such as automotive, aerospace, and industrial machinery. While it has some limitations, resin sand casting remains a popular choice due to its flexibility and cost-effectiveness.