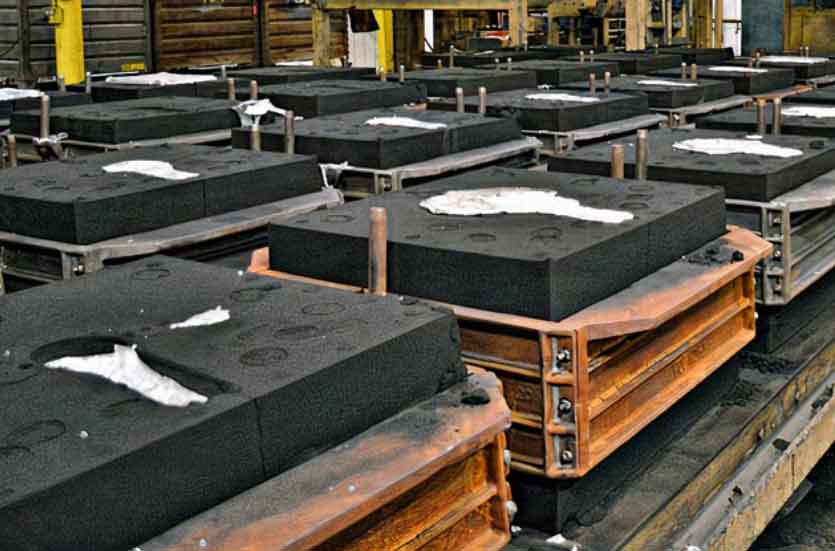
Resin sand casting, also known as no-bake sand casting or furan sand casting, is a versatile and widely used casting process that involves creating molds using a mixture of resin and sand. The process is suitable for both small and large-scale production and offers numerous benefits, making it popular in various industries. In this comprehensive guide, we’ll explore the resin sand casting process, its applications, advantages, and some essential considerations.
Resin Sand Casting Process:
- Pattern Making: The process starts with the creation of a pattern, typically made of wood, plastic, or metal, in the shape of the desired final product.
- Mold Preparation: A two-part mold is made using sand mixed with a thermosetting resin binder. This binder is usually furan resin or a urethane resin. The mold consists of two halves – the cope (top half) and the drag (bottom half).
- Mold Assembly: The cope and drag are put together to form a complete mold cavity. The pattern is placed within this cavity.
- Sand Compaction: The sand mixture is packed tightly around the pattern to ensure the mold takes the desired shape and maintains its structural integrity during pouring.
- Pattern Removal: Once the sand has sufficiently hardened, the pattern is removed from the mold, leaving behind a cavity that matches the pattern’s shape.
- Pouring: Molten metal, such as aluminum, bronze, iron, or steel, is poured into the mold cavity.
- Solidification: The poured metal cools and solidifies, taking the shape of the mold cavity.
- Mold Breakout: After the metal has cooled and solidified, the mold is broken open, and the casting is removed.
- Finishing: The casting may undergo further finishing processes, such as trimming excess material, removing any imperfections, and surface treatment.
Applications of Resin Sand Casting:
Resin sand casting finds extensive applications across various industries, including:
- Automotive: Used for manufacturing engine blocks, transmission components, cylinder heads, and other automotive parts.
- Aerospace: Producing critical components like turbine blades, impellers, and housings.
- Heavy Machinery: Used to create parts for construction equipment, agricultural machinery, and mining equipment.
- Art and Sculptures: Artists and sculptors often use resin sand casting for creating metal art and sculptures.
- Pumps and Valves: Manufacturing parts for pumps, valves, and other fluid-handling systems.
- Marine: Used to produce marine components, including propellers, marine engine parts, and ship fittings.
- Electrical and Electronics: Producing housings and enclosures for electrical and electronic devices.
Advantages of Resin Sand Casting:
- Versatility: Resin sand casting is suitable for a wide range of metals, making it a versatile casting process.
- Complex Geometry: It allows for the creation of intricate and complex shapes and designs.
- Cost-Effective: The process is relatively cost-effective for both low and high production volumes.
- Good Surface Finish: Resin sand casting can produce castings with a smooth surface finish.
- Dimensional Accuracy: It offers good dimensional accuracy and tight tolerances.
- Less Post-Casting Machining: Often requires minimal post-casting machining, reducing overall production time and costs.
- Environmentally Friendly: The process does not generate harmful emissions, making it environmentally friendly.
Considerations and Limitations:
- Casting Size: While resin sand casting is suitable for a wide range of sizes, extremely large castings may be challenging to produce.
- Mold Life: Resin sand molds have a limited lifespan, leading to more frequent mold changes in high-volume production.
- Pattern Costs: The initial pattern creation can be costly, especially for intricate designs.
- Casting Weight: Handling heavy castings can be labor-intensive and require specialized equipment.
- Surface Defects: Resin sand casting may result in minor surface defects, such as pinholes, compared to other casting methods like investment casting.
- Environmental Conditions: The curing process of the resin binder may be sensitive to temperature and humidity, requiring controlled conditions.
Resin sand casting is a highly versatile and efficient casting process that can be employed for a wide range of applications. Its advantages, such as cost-effectiveness, good surface finish, and dimensional accuracy, make it an attractive option for various industries. However, it’s essential to consider the specific requirements of each project and weigh them against the limitations of the process to ensure optimal results.