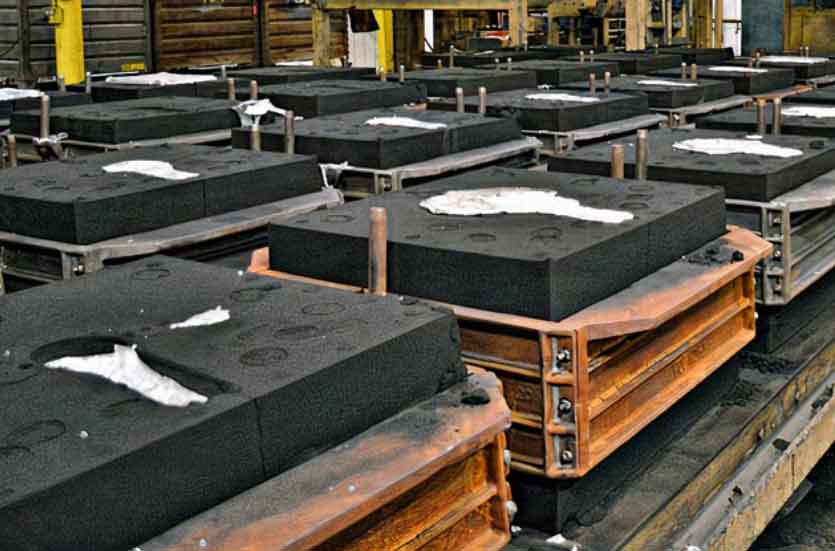
Resin sand casting, also known as shell molding or shell casting, is a versatile and cost-effective metal casting method widely used in the foundry industry. It involves creating sand molds using a resin-bonded sand mixture, which offers several advantages over traditional sand casting techniques. Here’s an overview of resin sand casting and its benefits:
Process Overview:
- Pattern Creation: The process begins with the creation of a pattern, typically made of wood, plastic, or metal, which represents the final shape of the casting.
- Mold Preparation: A two-part mold is made by compressing a resin-coated sand mixture around the pattern. The sand mixture is cured using a catalyst or heat to harden the resin.
- Pattern Removal: Once the mold has hardened, the pattern is removed, leaving a cavity in the sand that replicates the desired casting shape.
- Casting Process: The mold is assembled, and molten metal is poured into the cavity. The metal fills the void left by the pattern, creating the final casting.
- Cooling and Solidification: The molten metal is allowed to cool and solidify within the mold.
- Mold Breakout: After solidification, the mold is broken apart to reveal the completed casting, which may require additional finishing and cleaning.
Benefits of Resin Sand Casting:
- High Dimensional Accuracy: Resin sand casting offers excellent dimensional accuracy and a smooth surface finish due to the precise mold cavity created by the pattern.
- Versatility: The process is suitable for a wide range of metal alloys, including iron, steel, aluminum, and non-ferrous metals, making it adaptable to various casting requirements.
- Cost-Effectiveness: Resin sand casting can be cost-effective for both low and high-volume production runs due to reduced labor and material costs compared to other methods like investment casting.
- Reduced Defects: The use of resin-bonded sand helps minimize defects like sand inclusions, ensuring high-quality castings.
- Complex Shapes: Resin sand casting allows for the production of intricate and complex shapes that might be challenging to achieve with other casting methods.
- Improved Casting Surface: The smooth and fine surface finish of resin sand molds reduces the need for extensive post-casting finishing operations.
- Short Lead Times: Resin sand molds can be produced quickly, reducing lead times and improving overall production efficiency.
While resin sand casting offers many advantages, it may not be the optimal choice for all casting applications. For certain large-scale castings or where cost is a primary concern, traditional sand casting methods may still be preferred. The selection of a suitable casting method depends on the specific requirements of the project, the desired properties of the casting, and the available resources.