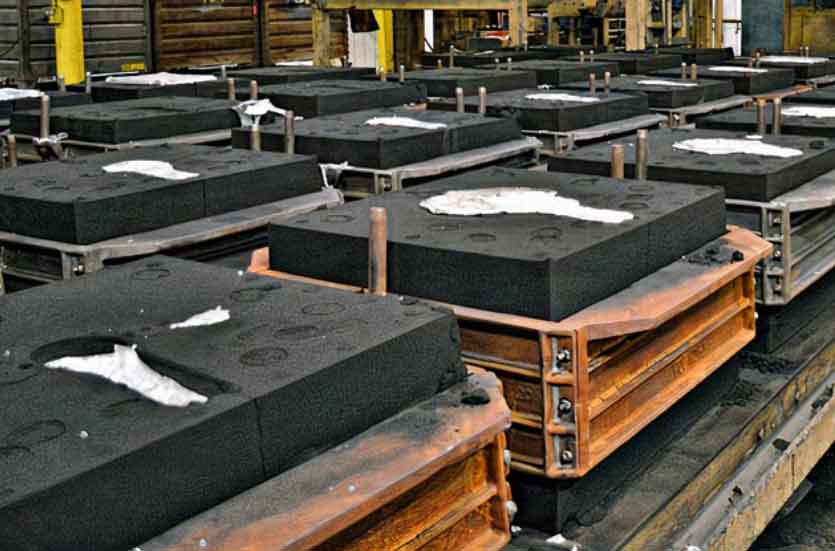
Resin sand casting is indeed a versatile and precise metal casting process that combines the benefits of both resin and sand molds. It is commonly used in the foundry industry to create complex metal parts with high precision and dimensional accuracy. Let’s explore the process and its advantages in more detail:
1. The Process:
a. Pattern Making: The first step in resin sand casting involves creating a pattern of the desired metal part. This pattern can be made from various materials like wood, plastic, or metal. It serves as a replica of the final part and is used to create the mold.
b. Mold Preparation: A two-part mold is used in resin sand casting. The lower part is called the “drag,” and the upper part is known as the “cope.” The pattern is placed in the drag, and resin-coated sand is packed around it.
c. Resin Coating: The sand used in this process is mixed with a special type of resin binder, which helps improve mold strength and dimensional stability. The resin-coated sand is applied in layers, and each layer is compacted to ensure uniform density.
d. Curing: After the mold is filled and compacted, it is left to cure. The curing process involves allowing the resin to harden and bond with the sand particles, creating a robust and stable mold.
e. Mold Assembly: Once the drag is cured, the cope is placed on top, and the two halves are securely fastened together.
f. Pouring: Molten metal is then poured into the mold through a gating system. The metal fills the void left by the pattern and takes the shape of the desired part.
g. Cooling and Solidification: The molten metal cools and solidifies inside the mold. The cooling time is controlled to ensure the metal solidifies without defects.
h. Mold Removal and Finishing: After the metal has solidified, the mold is opened, and the casting is removed. The casting may undergo additional finishing processes like trimming, grinding, and machining to achieve the final required specifications.
2. Advantages:
a. Versatility: Resin sand casting can produce a wide range of complex shapes and sizes, making it suitable for various industries and applications.
b. Precision and Dimensional Accuracy: The use of high-quality resin and sand mixtures, along with careful mold preparation, results in castings with precise dimensions and smooth surfaces.
c. Improved Surface Finish: The resin-coated sand creates a smoother mold surface, which translates into a better surface finish on the final casting.
d. Cost-Effectiveness: Resin sand casting is often more cost-effective than other precision casting methods like investment casting or die casting.
e. Less Defects: The use of resin-coated sand reduces the likelihood of defects like sand inclusions or surface imperfections.
f. Shorter Production Cycle: Compared to some other casting methods, resin sand casting has relatively shorter production cycles.
3. Limitations:
a. Tooling Cost: The initial cost of creating patterns and mold assembly can be relatively high, especially for small production runs.
b. Size Limitations: While resin sand casting can handle a wide range of sizes, extremely large castings may not be practical with this method.
c. Environmental Considerations: The use of resin binders raises environmental concerns due to the release of volatile organic compounds (VOCs) during casting and mold-making.
Resin sand casting offers an excellent balance between precision, versatility, and cost-effectiveness, making it a popular choice for many metal casting applications. However, like any manufacturing process, it is essential to consider specific requirements and limitations before choosing this method for a particular project.