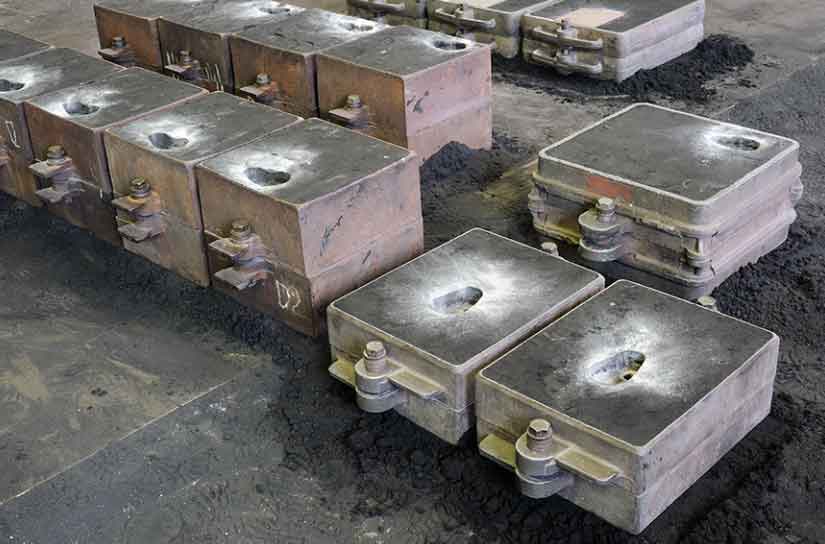
Resin sand casting is a reliable and widely used metal casting process that combines traditional foundry techniques with modern advancements. It is favored for its versatility, cost-effectiveness, and ability to produce intricate metal components. Here’s an overview of the resin sand casting process:
1. Pattern Making:
The process begins with the creation of a pattern, which is a replica of the desired metal component. Patterns can be made from various materials such as wood, plastic, or metal. Skilled pattern makers ensure the pattern accurately represents the final part’s shape and dimensions.
2. Mold Preparation:
A two-part mold, consisting of the “drag” (lower part) and the “cope” (upper part), is used in resin sand casting. The pattern is placed in the drag, and special sand mixed with a resin binder is packed around it. The resin-coated sand provides strength and cohesion to the mold.
3. Resin Coating:
The sand used in resin sand casting is coated with a resin binder, typically a phenolic urethane or furan resin. This resin-coated sand is applied in layers and compacted to ensure uniform density and optimal mold strength.
4. Curing:
Once the mold is filled and compacted, it undergoes a curing process. Curing involves allowing the resin to harden and bond with the sand particles, forming a robust and stable mold.
5. Mold Assembly:
After curing, the cope is placed on top of the drag, and the two halves are securely fastened together. The combination of the drag and cope creates a cavity that matches the shape of the desired metal component.
6. Pouring:
Molten metal is then poured into the prepared mold through a gating system. The gating system controls the flow of metal, minimizing turbulence and ensuring even distribution within the mold cavity.
7. Cooling and Solidification:
As the molten metal fills the mold, it starts to cool and solidify into the shape of the pattern and the mold cavity. The cooling time is carefully managed to ensure uniform solidification and prevent defects in the final casting.
8. Mold Removal and Finishing:
Once the metal has fully solidified, the mold is opened, and the casting is carefully removed. The casting may undergo additional finishing processes such as trimming, grinding, and surface treatments to achieve the desired specifications.
Resin sand casting’s reliability and popularity stem from its ability to produce high-quality, precise metal components with complex geometries. Its adaptability to various metals and alloys, cost-effectiveness, and shorter production cycles make it an attractive choice for a wide range of industries, including automotive, aerospace, machinery manufacturing, and more. As technology continues to advance, resin sand casting is likely to remain a reliable and vital process in the world of metal casting.