Resin sand casting is a popular casting process that involves the use of resin-bonded sand molds to create complex metal components. Here’s an overview of the resin sand casting process and its applications:
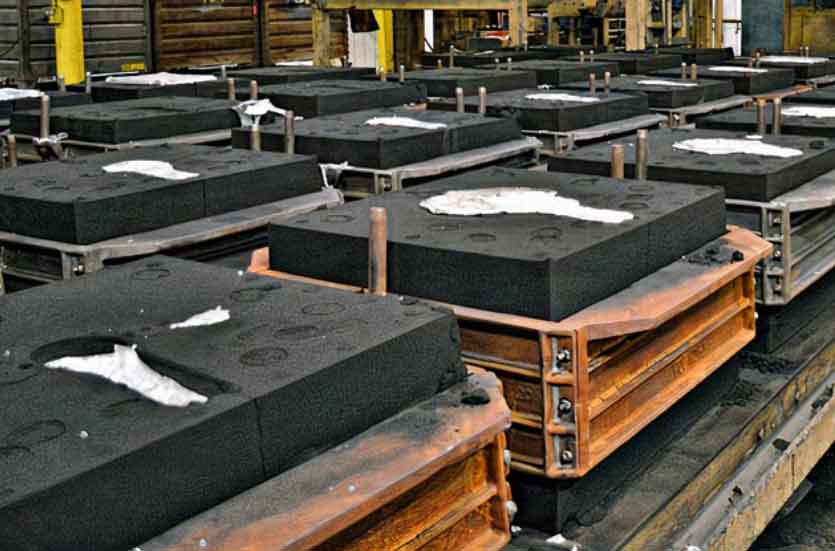
Process Overview:
- Pattern Creation: A pattern, typically made of wood, plastic, or metal, is created based on the desired shape of the final component.
- Mold Preparation: The pattern is placed in a flask, and a two-part mixture of resin and sand is prepared. The sand mixture is packed around the pattern, creating a mold cavity.
- Curing: The resin in the sand mixture is cured, either through chemical reactions or by applying heat. This solidifies the sand mold and creates a rigid structure.
- Pattern Removal: The pattern is removed from the mold, leaving behind a cavity that matches the desired component shape.
- Metal Pouring: The mold is preheated, and molten metal, such as iron, steel, or aluminum, is poured into the mold cavity.
- Solidification and Cooling: The molten metal solidifies within the mold, taking the shape of the cavity. The mold is allowed to cool, ensuring complete solidification of the metal.
- Mold Breakout and Finishing: The mold is broken away from the solidified metal component, revealing the final shape. The component may undergo further finishing processes such as grinding, machining, or surface treatment to achieve the desired specifications.
Applications:
- Automotive Industry: Resin sand casting is widely used in the automotive industry for the production of engine blocks, cylinder heads, transmission components, and other complex parts. Its ability to create intricate designs, achieve high dimensional accuracy, and handle high-volume production makes it suitable for automotive applications.
- Machinery and Equipment: Resin sand casting finds applications in various machinery and equipment industries. It is used to manufacture components such as gearboxes, pumps, valves, machine frames, and agricultural machinery parts. The process allows for the production of robust and precise parts that can withstand demanding operational conditions.
- Energy Sector: Resin sand casting is employed in the energy sector for manufacturing components used in power generation, including turbines, generators, and heat exchangers. The process ensures the production of parts with high integrity, dimensional accuracy, and resistance to extreme temperatures and pressures.
- Aerospace Industry: Resin sand casting is utilized in the aerospace industry for the production of critical components such as aircraft engine parts, landing gear components, and structural elements. The process offers the necessary precision, strength, and reliability required in aerospace applications.
- Construction and Architecture: Resin sand casting is used to create architectural and decorative metal components for building facades, sculptures, and ornamental designs. Its ability to produce intricate shapes and achieve high-quality surface finishes makes it suitable for artistic and aesthetic applications.
Resin sand casting provides a versatile and cost-effective solution for manufacturing complex metal components across various industries. Its ability to create intricate designs, achieve high dimensional accuracy, and handle both small and large production volumes makes it a popular choice for a wide range of applications.