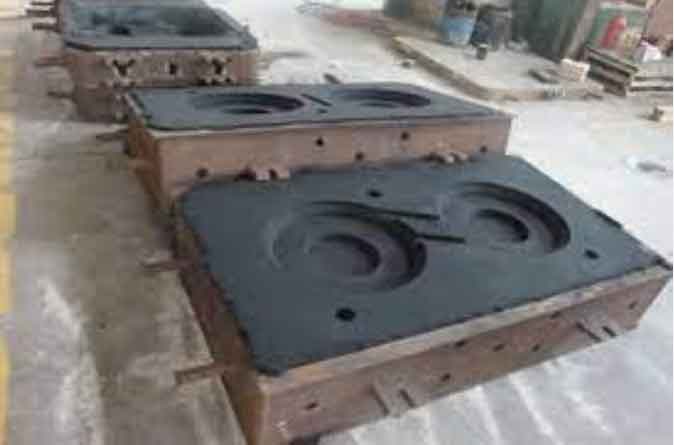
Resin sand casting plays a significant role in bridging the gap between prototyping and production in manufacturing. It offers a cost-effective and efficient solution for producing functional prototypes that closely resemble the final production parts. Here’s how resin sand casting serves as a bridge between prototyping and production:
- Rapid Prototyping: Resin sand casting enables the rapid production of functional prototypes. By using 3D-printed patterns or other rapid prototyping techniques, engineers can quickly create patterns and molds for resin sand casting. This allows for the timely evaluation of design concepts, fit, and functionality before committing to full-scale production.
- Design Iterations and Refinements: Resin sand casting allows for design iterations and refinements during the prototyping stage. As resin sand casting offers design flexibility and the ability to produce complex shapes, designers can make adjustments and modifications to the prototypes based on feedback and testing results. This iterative process helps optimize the design and enhance the final product’s performance and manufacturability.
- Verification of Manufacturing Feasibility: Resin sand casting helps verify the manufacturing feasibility of a design before scaling up to production. By using resin sand casting to create prototypes, engineers can assess factors such as moldability, parting line definition, gating system effectiveness, and potential manufacturing challenges. This verification process minimizes the risk of design flaws or production issues during full-scale manufacturing.
- Functional Testing: Resin sand casting produces prototypes that closely resemble the final production parts in terms of material properties and mechanical characteristics. This enables functional testing and validation of the prototypes to ensure they meet performance requirements and desired functionality. Any necessary design modifications can be identified and implemented during the prototyping stage.
- Cost Optimization: Resin sand casting offers a cost-effective solution for producing small to medium-sized production runs. As resin sand casting can closely mimic the production process, it allows manufacturers to estimate the production costs accurately. This helps optimize costs, evaluate manufacturing feasibility, and make informed decisions about scaling up to full-scale production.
- Smooth Transition to Production: The use of resin sand casting for prototyping facilitates a smooth transition to production. Since the prototypes produced with resin sand casting closely resemble the final parts, manufacturers can use the same molds or modify them as necessary for full-scale production. This continuity helps streamline the production process, reduce lead times, and ensure consistency in product quality and performance.
- Manufacturability Assessment: Resin sand casting provides insights into the manufacturability of a design. By using this method for prototyping, manufacturers can evaluate factors such as mold complexity, tooling requirements, material behavior, and production cycle times. This assessment allows for the identification of potential manufacturing challenges and optimization opportunities before proceeding to mass production.
Resin sand casting serves as a vital bridge between prototyping and production by enabling rapid prototyping, design refinements, functional testing, and manufacturability assessment. It helps reduce costs, mitigate risks, and optimize the final design for successful production. The ability to closely replicate production processes and materials makes resin sand casting an invaluable tool in transitioning from prototypes to full-scale manufacturing.