Resin sand casting stands as a remarkable example of bridging the gap between tradition and innovation in the field of metal casting. This casting method combines centuries-old foundry techniques with modern materials and technologies to create intricate metal parts with precision and efficiency. Here’s how resin sand casting achieves this synergy:
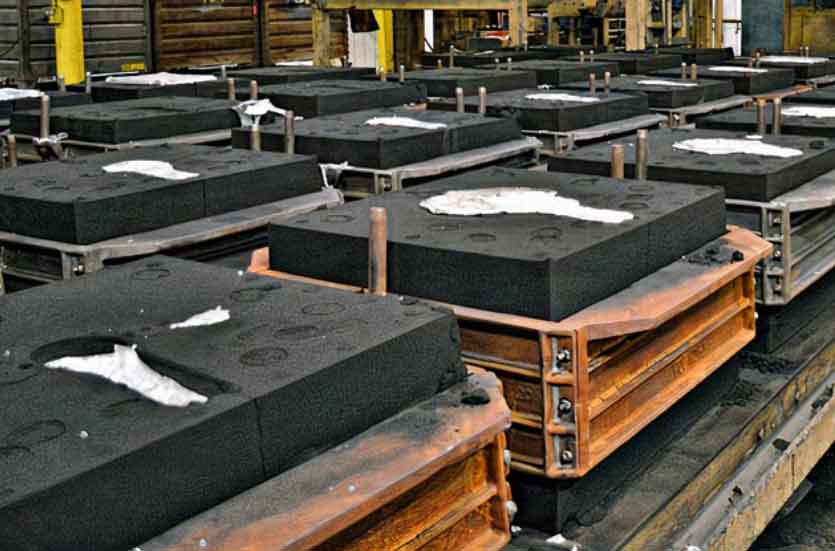
1. Traditional Foundry Techniques:
Resin sand casting draws from the long-established practices of sand casting, one of the oldest casting methods known to humans. Sand casting has been used for millennia to create metal objects, and it remains a fundamental process in the foundry industry. Resin sand casting preserves the core principles of sand casting, such as pattern making, mold preparation, and metal pouring, while enhancing them with modern advancements.
2. Modern Resin Binders:
The innovative aspect of resin sand casting lies in the introduction of modern resin binders to traditional sand molds. The incorporation of high-quality resins, such as phenolic urethane or furan resins, significantly improves the strength, dimensional accuracy, and surface finish of the molds. These binders ensure the molds can withstand the rigors of the metal casting process and produce higher-quality castings.
3. Improved Dimensional Accuracy:
While traditional sand casting can be prone to dimensional variations, resin sand casting offers improved dimensional accuracy. The precise control of resin-coated sand and advanced molding techniques results in castings that closely adhere to the intended design specifications.
4. Complex Geometries:
Resin sand casting enables the production of metal parts with complex geometries, including intricate internal features and undercuts. This flexibility is vital for modern industries that demand intricate and high-performance components.
5. Automation and Digital Tools:
Resin sand casting also embraces modern automation and digital tools to enhance productivity and efficiency. Advanced simulations and modeling software help optimize mold design, gating systems, and cooling processes, leading to better results and reduced trial-and-error during production.
6. Eco-Friendly Considerations:
In recent years, resin sand casting has embraced eco-friendly practices. Efforts have been made to develop more sustainable resin binders and to minimize waste during the casting process. Additionally, recycling and reusing sand are becoming more common in the industry.
7. Integration with Additive Manufacturing:
Another exciting innovation is the integration of resin sand casting with additive manufacturing (3D printing). 3D-printed patterns and cores can be used in the casting process, allowing for even greater design freedom and rapid prototyping.
8. Cost-Effectiveness and Versatility:
Resin sand casting remains a cost-effective and versatile solution for producing both small and large metal parts. Its ability to accommodate various metals and alloys while keeping production costs in check makes it a preferred choice for many applications.
Resin sand casting beautifully combines traditional craftsmanship with modern materials, technologies, and eco-conscious practices. By embracing innovation while respecting the legacy of foundry traditions, this casting process continues to play a crucial role in manufacturing industries worldwide. It empowers designers and engineers to bring their creative visions to life while meeting the demands of today’s dynamic markets.